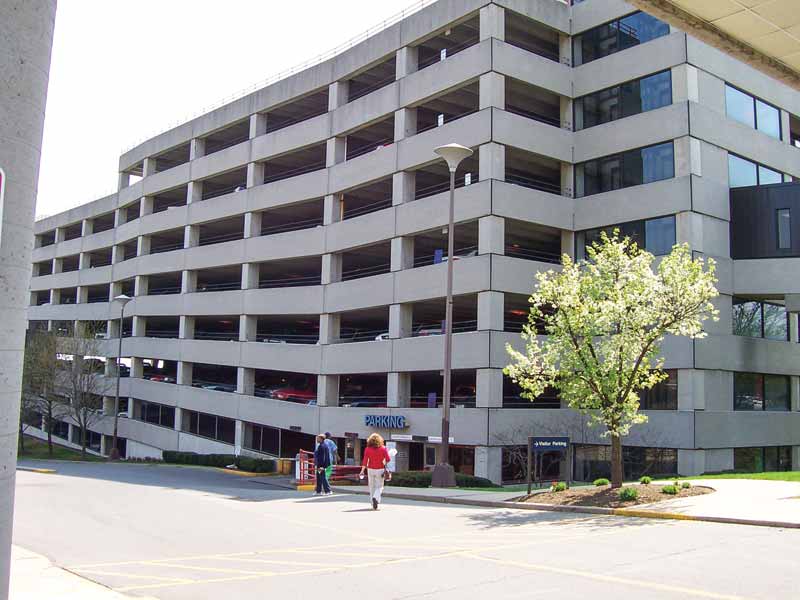
by Julie Holmquist, Casey Heurung, and Jessi Meyer
Parking garages are utilitarian structures designed to hold a large number of vehicles at one time on a comparatively small footprint of land. They must be built to withstand large amounts of weight and vehicle traffic. Durability is key as parking garages are often located in busy metro areas where closure, repair, or reconstruction can be disruptive. Time, labor, and material costs for renovation are also prohibitive. These structures are generally made from reinforced cast-in-place or precast concrete, making corrosion one of the most common challenges to durability.
Corrosion of embedded steel reinforcement in parking garages is brought on by a variety of causes. When new structures are built, the high pH of concrete causes the formation of a natural protective layer on the surface of embedded rebar. As time passes, carbonation eventually sets in and lowers the pH of the concrete, removing the natural protection. The rebar is then vulnerable to the ingress of water, chlorides, or various pollutants. After corrosion initiates, the following vicious cycle begins:
- Corrosion products cause the rebar to expand, putting pressure on the concrete and causing cracks.
- Cracks allow additional water, chlorides, or other contaminants to ingress and attack the embedded rebar, resulting in more corrosion.
- Corrosion on the rebar creates more cracks and eventual spalling, causing the concrete to fall off the surface of the structure, and eventually leave the reinforcing metal exposed.
- If not interrupted, the cycle eventually leads to structural deterioration and deficiency.
Corrosive attack is more severe in certain regions. In northern climates subject to harsh winters with snow and ice, municipalities combat slippery roads and surfaces by using deicing salts. This harsh application of chloride to the concrete surface accelerates the corrosion process and instigates early repairs.
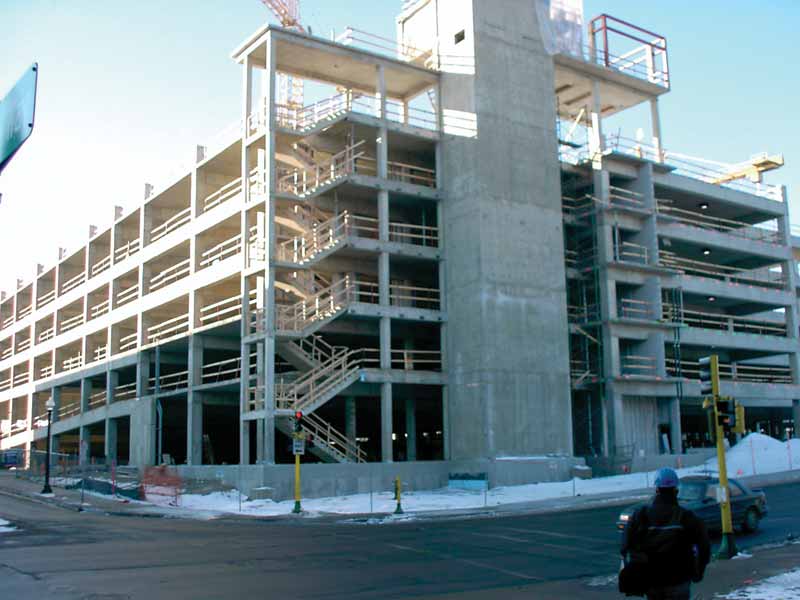
Photos courtesy Cortec Corp
In coastal environments, concrete structures are attacked by salt spray and high temperatures, intensifying corrosion problems. In coastal areas in the Middle East, the corrosion threat is heightened by high groundwater tables and chloride-rich soils, endangering concrete foundations and requiring special design considerations to provide a long service life.
Countering corrosion
A variety of options exist for countering corrosion on both new and existing structures. Their cost and benefits should be weighed when selecting the right corrosion protection for the job.
Epoxy-coated rebar
Rebar coated with epoxy can be placed in new structures. While this can be very effective as long as the coating lasts, it can also add significant costs to the structure. It is mainly beneficial for new structures, since the idea of replacing the entire network of rebar in existing buildings is impractical, if not impossible. Further, improper application or damage to the epoxy coating can result in accelerated corrosion at localized points, leading to earlier-than-expected failure. (For more information, read the report, “Corrosion of Epoxy Coated Rebar in Florida Bridges,” by Alberto A. Sagüés, et al. here.)
Calcium nitrite admixtures
Another strategy employed in new structures is the use of calcium nitrite (CNI) admixtures. These raise the chloride threshold by competing with chlorides for a place on the surface of the rebar. Practically speaking, this means the structure must reach a higher chloride content before a corrosion site can be initiated. However, larger doses (up to 30 L/m3 [6 gal/cy]) of the admixture must be applied to counter the expected rates of chloride exposure. If the threshold is surpassed, corrosion can take place at the same or accelerated rates compared to untreated reinforced concrete. While this treatment can be effective at sufficient doses, it also causes some undesirable side effects. For instance, CNI admixtures accelerate set time and increase shrinkage cracking, making it more difficult to lay and properly finish fresh concrete. As dosage rates increase to compensate for higher chloride exposure, the shrinkage and set time problems are exacerbated, creating more hassle for both the ready mix company and contractors placing the material. CNI also raises health concerns because of its nitrite-based makeup. It is not considered acceptable for use in potable water structures.
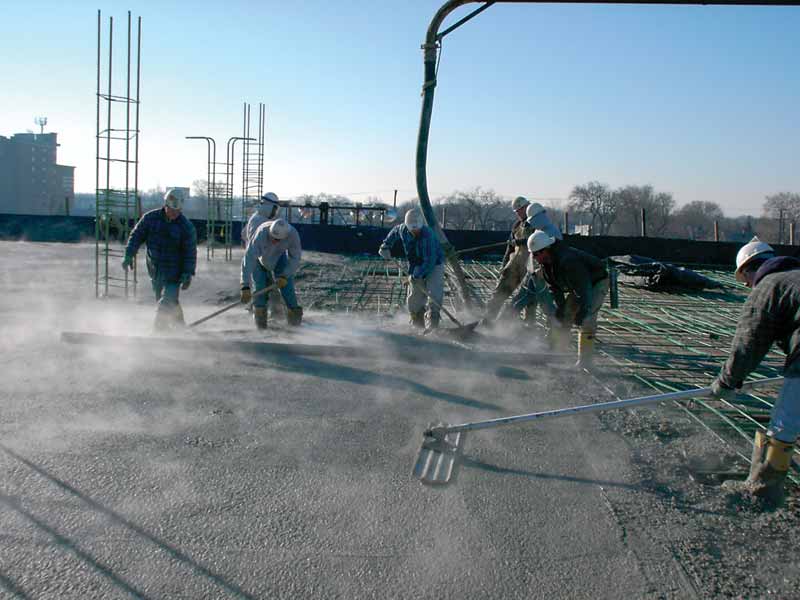
Cathodic protection
Cathodic protection (CP) is another strategy for protection against corrosion. It can be accomplished by redirecting corrosion to a sacrificial anode, or by sending an electric current (impressed current cathodic protection [ICCP]) though the rebar to reroute the normal electrochemical corrosion processes. However, for full effectiveness of CP, all rebar must be continuously connected. In the case of ICCP, the extra cost and maintenance of a constant electrical current has to be taken into consideration.
Concrete water repellents
Applying water repellents to both new and existing structures is a good maintenance practice. These materials discourage corrosion by significantly reducing moisture and chloride ingress into the structure. However, once the repellent layer is compromised, through age or cracking, corrosive elements can work their way to the rebar surface and initiate the corrosion reaction.
Migrating corrosion inhibitor technology
An advantageous strategy for protecting against corrosion on both new and existing structures is the use of migrating corrosion inhibitor technology, introduced into commercial use in the 1980s. This technology is generally safer than calcium nitrite admixtures, and its ability to migrate through the concrete pore structure increases its versatility and effectiveness. It offers standalone protection, but has shown compatibility with other forms of protection, such as CP and water repellents, thereby allowing a multilayered approach to corrosion mitigation in especially rigorous situations. (Consult the presentation, “Evaluation of Interactions between Cathodic Protection and Corrosion,” by Khalil Abed, et al. at the National Association of Corrosion Engineers (NACE) Concrete Service Life Extension Conference in New York City, New York, in June 2017.)
Migrating corrosion inhibitors are based on a blend of salts of amine alcohols (first generation) or amine carboxylates (second generation) with the ability to migrate through concrete and form a protective film on metal surfaces. They can be admixed into new concrete or applied as a liquid surface treatment for penetrating existing concrete. The resulting molecular layer can act as a “mixed” inhibitor to protect against both anodic and cathodic reactions of a corrosion cell.
Migrating corrosion inhibitors can delay the onset of corrosion and also reduce corrosion rates that have already started. For example, one six-and-a-half year independent test of amine carboxylate corrosion inhibiting admixtures concluded time to corrosion was generally two times longer for one migrating corrosion inhibitor (Inhibitor A) and three times longer for another migrating corrosion inhibitor (Inhibitor B). Inhibitor A reduced the total corrosion fourfold, and Inhibitor B reduced the total corrosion as much as 16-fold during the test. The “Report of Concrete Corrosion Inhibitor Testing, Comparative Study” was prepared by American Engineering Testing (AET) in Saint Paul, Minnesota, in August 2002.)
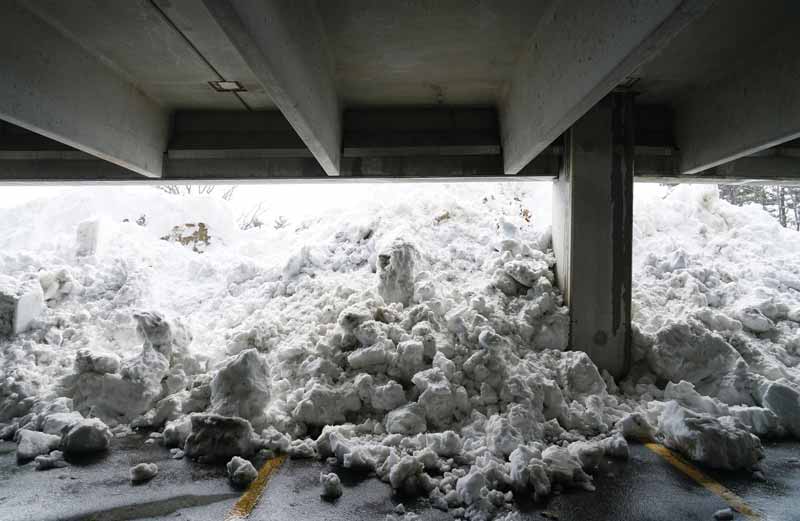
Photo © BigStockPhoto.com
A first-generation migrating corrosion inhibitor was used on the Randolph Avenue Bridge in Minnesota. The admixture was employed in a 1986 repair on one side of the bridge, while the other side was left untreated. Periodic testing was completed, and by 2011, the untreated side had entered a state of active corrosion, while the treated side was still considered passive with average corrosion rates more than 60 percent lower than the control. (See, “Organic Corrosion Inhibitors – New Build and Existing Structures Performance,” by J. Meyer for the Brian Cherry International Concrete Symposium held in July 2017.)
The difficulty of gathering data on new structures and comparing it to typically non-existent control (untreated) structures of the same type and environment leaves users mainly dependent on standardized test data to estimate the benefit a migrating corrosion inhibitor admixture has on a new structure’s service life. The process is simplified by using service life prediction modeling software. An accessible prediction software available as a free download has been developed by a consortium headed by the American Concrete Institute’s (ACI’s) strategic development council (SDC). The research-based model provides estimates of how design, temperature, chloride exposure, and other factors impact concrete’s service life. (See, “Organic Corrosion Inhibitors – New Build and Existing Structures Performance,” by J. Meyer for the Brian Cherry International Concrete Symposium held in July 2017.) Using inputs based on standardized testing of migrating corrosion inhibitors, engineers can predict an estimated design life for different concrete mix types and climates.
The Princess Tower (the tallest residential-only building when completed in 2012) in the United Arab Emirates was able to upgrade from an estimated 48-year service life for a foundation that did not use inhibitors to a 103-year estimated service life with the use of Inhibitor A. This was at an additional cost of 0.07 percent compared to the rest of the tower’s construction expense. In this case, the modeling software predicted a doubled service life.
Another software model involved a seawall constructed in 2017 on Longboat Key in the Gulf of Mexico. The software was used to help find a mix design with the ability to provide an estimated service life of at least 100 years. The first standard seawall mix input showed an estimated service life of 15.2 years before the first repair would be needed. The addition of Inhibitor A admixture tripled the prediction to 46.9 years of estimated service life before the first repair would be needed. Other mix designs were subsequently tried to find a combination that would meet or exceed the ambitious requirements of the project owner. Eventually, the team settled on a mix design that brought the estimated service life up to more than 100 years on its own. With the addition of Inhibitor A, this estimation increased to more than 150 years.
Using inhibitors in new structures
Migrating corrosion inhibiting admixtures have a lot to offer when constructing new parking structures. They tend to have minimal effect on concrete setting properties and allow good workability. Whereas the ASTM C1582, Standard Specification for Admixtures to Inhibit Chloride-Induced Corrosion of Reinforcing Steel in Concrete, requires admixtures meet at least 80 percent of the compressive strength of a control sample not containing corrosion inhibitors, testing showed that Inhibitor A was able to achieve more than 100 percent of the compressive strength of the control at three and 28 days, six months, and one year (Figure 1). Some versions delay concrete mix set time, allowing more time for finishing. However, they can also be prepared as normal set admixtures that neither accelerate set time (a problem with CNI admixtures) nor extend it. Both normal- and extended-set migrating corrosion inhibitor admixtures meet the physical property results regarding set time, compressive and flexural strength, shrinkage, and freeze/thaw durability of ASTM C1582. Also unlike CNI, migrating corrosion inhibitor admixtures of the amine carboxylate blend have been certified by Underwriters Laboratories (UL) to meet NSF International/American National Standards Institute (ANSI) 61, Drinking Water System Components for Use in Potable Water Structures. (For a listing, visit the Underwriters Laboratories (UL) Online Certifications Directory.) Many contain bio-based material (derived from corn), and one has officially been designated as a U.S. Department of Agriculture- (USDA) certified bio-based product under the USDA BioPreferred Program. (For more, click here.) Typical dosage is 0.6 to 1 L/m3 (1 to 1.5 pints/yd3), much lower than CNI dosage, which varies dramatically based on expected chloride loading.
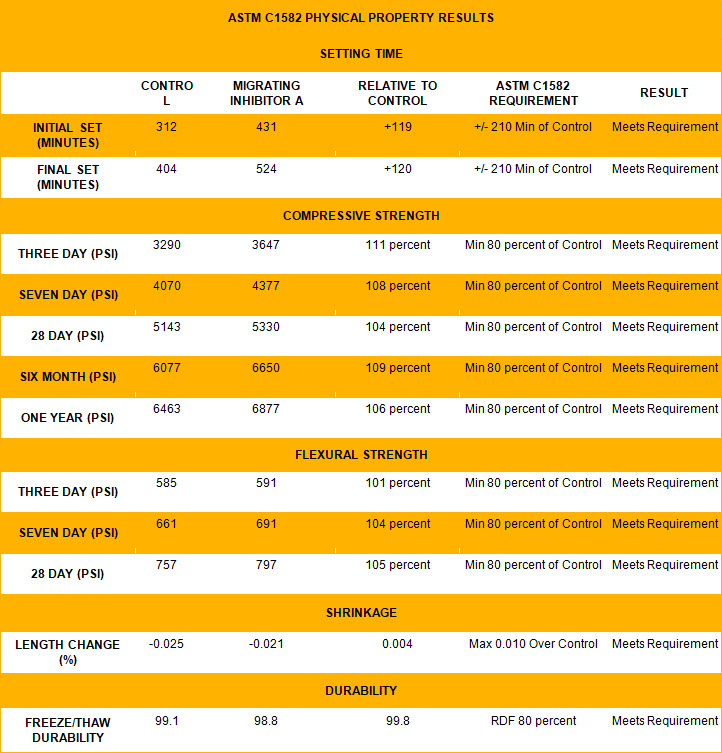
Image courtesy Cortec Corp