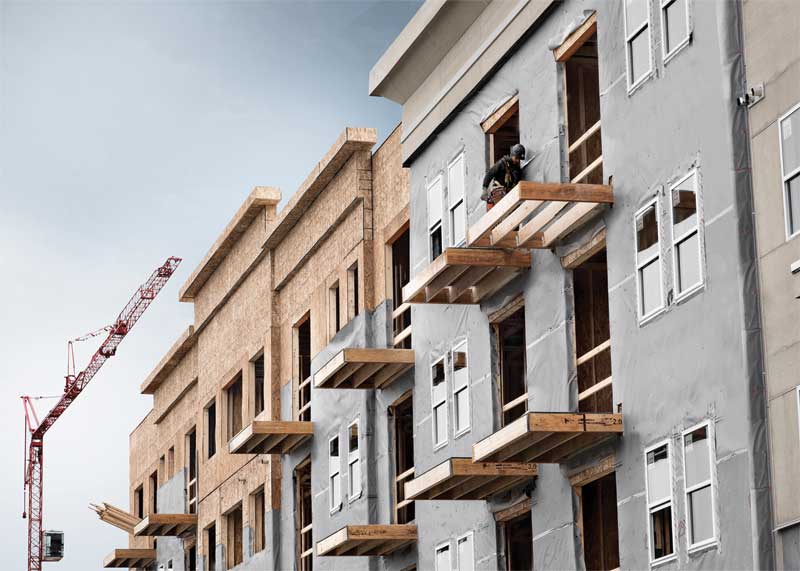
by Bijan Mansouri
In the building industry’s ever increasing pursuit of tighter and more waterproof structures, is there a point at which a wall is built too tight? While a watertight assembly is vitally important for wall controlling issues such as mold growth and protecting indoor air quality (IAQ), some building practices may be inadvertently making it easier for moisture-related issues to fester. After all, no matter how tightly a wall is constructed, water is inevitably going to find its way in. There is no such thing as a “waterproof” wall, just one built so tightly it is almost guaranteed to get and stay wet.
The highest performing wall assemblies are the ones designed to realistically manage moisture and dry out, and not those designed with the unachievable goal of completely locking out all moisture. The good news is there are a growing number of methods for managing moisture, driven by advances in material technology, evolving building codes, and a growing awareness among end-users for mold prevention, IAQ, and energy efficiency.
Finding the “sweet spot” for material permeability
Water can find its way into a wall in numerous ways. High humidity and extreme temperatures can cause vapor diffusion when warm, indoor air causes condensation on colder, outside surfaces. Wind-driven rain can be forced into small openings in the exterior cladding at joints, laps, and utility cutouts, and wind blowing around the building can create a negative pressure within the wall assembly, which siphons water into the wall.
One of the most challenging situations in which to manage moisture is when a reservoir cladding like fiber cement, brick, or stone is specified in a region where air-conditioning is often used and with an annual rainfall of 508 mm (20 in.) or more. Most of the country falls within these conditions, and a growing preference for reservoir claddings require more careful attention to managing moisture.
When reservoir claddings become wet from rainwater or condensation and are then warmed by the sun, the vapor pressure of the stored water increases, driving it both inward and outward from the cladding material. Where the moisture goes from there—and how quickly it gets there—is largely a function of the permeability of the adjacent building materials within the assembly.
Permeability measures the amount of vapor transmission a building material will allow over a period of time. ASTM E96, Standard Test Methods for Water Vapor Transmission of Materials, addresses two testing procedures for measuring permeability—the desiccant method and the water method.
In the desiccant method, the material to be tested is sealed to a test dish containing a desiccant, or drying agent, and the assembly is placed in a controlled atmosphere. Periodic weighing determines the rate at which water vapor has moved through the specimen into the desiccant. In the water method, the dish contains distilled water, and periodic weighing determines the rate of vapor movement through the specimen from the water.
In most wall assemblies, outwardly driven moisture will not cause many problems (unless one is dealing with a material like stucco painted with a low-perm paint, in which case bubbling and cracking would be visible). However, the inwardly driven moisture presents a problem, especially in situations where conditioned indoor air is much cooler than the warm, moist exterior.
Typically, this inwardly driven moisture vapor is managed by separating the cladding from the rest of the assembly with a capillary break, which can be a gap or a sheathing material able to shed water or not absorb or pass water. Impermeable sheathing, such as extruded polystyrene (XPS), is one option for halting inward vapor drive. In these types of assemblies, the inwardly driven moisture condenses on the surface of the XPS sheathing and drains downward.
However, in situations where a reservoir cladding is paired with a highly permeable sheathing like gypsum board (which can be as high as 50 perms) or a moisture-retentive material like oriented strand board (OSB), an air gap may not be enough to slow down inward moisture intrusion. In these applications, an added weather-resistant barrier (WRB)—commonly referred to as a building or house wrap—is needed to reduce unwanted moisture intrusion.
In the paper, “Inward Drive – Outward Drying,” building scientist Joseph Lstiburek identifies the “sweet spot” for the permeance of this WRB layer as between 10 and 20 perms. (For more, click here.) Too high, he writes, and the moisture driven out of the back side of the reservoir cladding into the air space will blow through the layer and the permeable sheathing and into the wall cavity. Too low, and the outward drying potential of the cavity is compromised. Thankfully, advances in building wrap technology are adapting to meet this need.