FAILURES
David Patterson, AIA, Deborah Slaton, and Kenneth Itle, AIA
Limestone at the base of a building façade is vulnerable to staining from various sources, including planting beds or soil adjacent to the wall, water or snow collecting against the building, and ice-melters used on sidewalks and paving.
Alkali stain is caused by alkali-containing moisture moving through the limestone from the back side or bottom edge, depositing minerals on the face of the stone as the water evaporates. It can also be caused by ground moisture absorbed through the face or edge of the stone. Sources of alkali in new construction include poured-in-place concrete, newly placed concrete block, or other cementitious construction materials such as mortar. (In the example shown, the limestone column cladding extends below the paving system into the sand setting bed, both of which retained moisture against the stone and provided a source of alkalis, resulting in staining.) While mild alkali staining is primarily a cosmetic problem, deposits of high alkalinity can lead to significant distress.
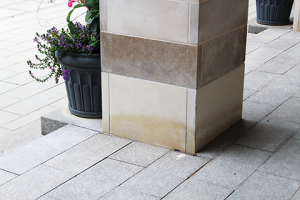
The process by which alkali staining of limestone occurs is similar to that of efflorescence, although in the latter, moisture transmits minerals such as sodium sulfate and calcium sulfate from sources within the wall and deposits them on the stone surface. Efflorescence typically appears white in color, while alkali staining often appears brown. It also tends to be less water-soluble than efflorescence deposits, and although alkali stains in new construction will disappear when sources of moisture are removed, staining related to ground moisture tends to be ongoing.
Generally, to avoid alkali staining of limestone cladding, the stone at the base of the wall should be separated from soil or paving systems. Careful detailing incorporating through-wall flashing, raised curbs (or plinths), sill courses of an alternate material, or similar elements can prevent the limestone’s contact with soil.
Indiana Limestone Institute (ILI) also recommends dampproofing the back and edges of the limestone where used below-grade by application of a coating (such as a bituminous product). Application of a coating should be performed in the field by the stone installer to ensure any field-cut edges are coated and the coating is not damaged during shipping and handling. ILI guidelines note the coating should be applied to all concealed surfaces and edges of the stone masonry to a height of 0.3 m (1 ft) above grade.
Avoiding alkali staining in limestone depends on reducing or eliminating exposure of the stone to alkali-bearing moisture; therefore, the recommended approach is to adjust detailing to prevent limestone from extending below grade or being in contact with soil.
David S. Patterson, AIA, is an architect and senior principal with the Princeton, New Jersey, office of WJE, specializing in investigation and repair of the building envelope. He can be contacted at dpatterson@wje.com.
Deborah Slaton is an architectural conservator and principal with Wiss, Janney, Elstner Associates (WJE) in Northbrook, Illinois, specializing in historic preservation and materials conservation. She can be reached at dslaton@wje.com.
Kenneth M. Itle, AIA, is an architect with the Northbrook, Illinois, office of WJE, specializing in investigation and preservation. He can be reached at kitle@wje.com.
Hi, my name is Igor and I’m a sales representative at KREITMAKER Building Supply store.
We are supplying Indiana Limestone for different projects and in couple of month our clients coming back to us and asking for solution how to clean this alkali staining. Most of the problems appear on steps and pavers installed on top of concrete pad. Is there is any solutions for it ???
always install limestone on white ( or whitish ) color mortar, make sure limestone has no contact with dark color mortar.