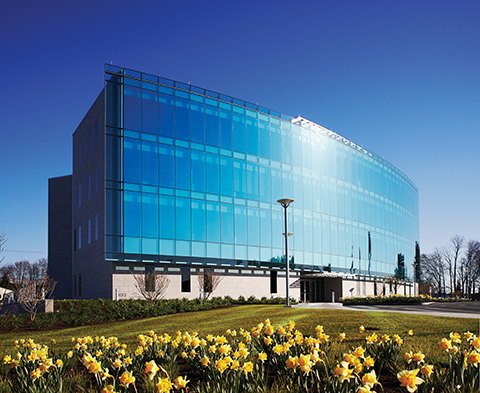
by Dean Lewis
Curtain walls are often the focal point of aesthetic design for a multi-story building. Behind the attractive façade are the pedestrian, yet arguably more important, functional components that ensure safety and reliability—fasteners that transfer loads both imposed and experienced by the assembly to the building’s structural framework.
Being key elements of the load path, all fasteners should be analyzed to ensure their material, thickness, and quantity are adequate. In doing so, designers must quantify both dead and live loads on the wall system—which translate to bending, shear, bearing, and pull-out loads on the connections.
Fasteners must have the hardness, along with the yield, tensile, and shear strength to appropriately withstand these loads without compromising the wall’s integrity and weathertightness. Different anchorage configurations are also required for the various substrates typically encountered in commercial or institutional-type structures, featuring concrete, masonry, or steel frame.
Fastener guidelines
Numerous organizations have developed specifications, performance testing methods, and design guides for wall cladding fasteners, including:
- Aluminum Association;
- American Institute of Steel Construction (AISC);
- American Iron and Steel Institute (AISI);
- ASTM International;
- Industrial Fasteners Institute (IFI); and
- Society of Automotive Engineers (SAE).
Compiling, applying, and in some cases reconciling the data from these various sources to produce a viable fastener specification is a formidable task.
That task is made easier by the American Architectural Manufacturers Association (AAMA) Technical Information Report (TIR)-A9-14, Design Guide for Metal Cladding Fasteners, which provides the data necessary to select fasteners for anchoring the curtain wall to the building structure. Metals used in fasteners covered by TIR-A9 include various types of carbon steel and stainless steel alloys. It should be noted aluminum fasteners are not recommended for curtain wall anchoring systems.
A complete specification must include fastener size and type, as well as material, calculated minimum mechanical properties (e.g. bending, shear, bearing and pull-out loads, thickness), and type of protective coating required. Fastener quality and corrosion resistance also should be addressed by specifiers.
“Fastener Specification Checklist” adequately defines the parameters for a given application including proposed anchorage arrangement, which defines the number and location of the fasteners, as well as determination of the forces acting on the attachments and the maximum design load per attachment.
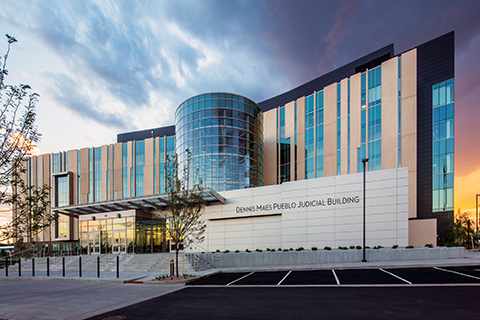
A recommendation of attachment devices to resist the determined forces should also be included as the number and spacing must be sufficient to meet the loads. Additionally, fastener length should be sufficient to penetrate the substrate to a depth designed to meet applicable building codes, manufacturer recommendations, and structural calculations.
Confirmation the curtain wall frame can resist the forces at the attachment points is required. The installation of fasteners or fastening systems must limit distortion of any framing member and must not in any way impede the action of operable components. It is also necessary to specify the required anchorage and/or fastener quantity, spacing, type, material, strength, embedment, edge distances, and other parameters as appropriate.
The mode of potential failure for the material and fasteners along the load path should be considered. This includes the fastener itself, as well as the material being fastened to the substrate, which can fail by bending, buckling, or pull-out (i.e. the force required to pull the fastener out of the base material), and/or pullover (i.e. the force to pull the material over the head of the fastener). TIR-A9 tables give allowable pull-out values for different aluminum thicknesses of various alloy designations (e.g. 3003-H14, 5005-H34, 6061-T6, 6063-T5, 6063-T6, and 6005A-T61) for UNC (i.e. threads designated as ‘coarse’ under the United Thread Standard [UTS]) and spaced threads for different screw diameters.