by Robert C. Haukohl, PE, Bartosz Lipinski, PE, SE, and Matthew L. Wagner, SE
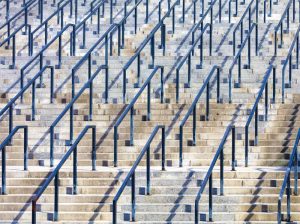
Railing systems are ubiquitous in the built environment, and as such, their appearance is more highly considered than functionality. Minimum loading requirements for railing systems have been part of codes for about as long as these standards have been in existence, and although railing systems may be built and tested to meet code loading requirements, and manufacturers provide generic mounting details, rail post anchorages still need to be formally designed either by the designer of record or by a specialty engineer who is retained through the delegated design process.
Rail post anchorage design is often not properly emphasized, or is altogether forgotten during the design process. The design and installer/manufacturer teams often see anchorage design as the others’ responsibility. Critical design and coordination issues are either not considered or left to be resolved in the field. Someone needs to verify the anchorage is capable of supporting code required loads, coordinate the trades involved so the anchorage does not interfere with other construction, and ensure post holes will not explode (Figure 1). This person can be the architect, engineer of record (EOR), delegated designer, contractor, or all of the above depending on project size and delivery method.
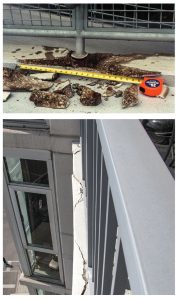
Images courtesy Raths, Raths & Johnson, Inc.
The authors see the same design and construction errors made repeatedly, including:
- the use of expansive grout or grout that weathers or disintegrates with repeated exposure to water;
- lack of consideration of detail-specific design constraints, such as edge distance and anchor size; and
- absence of coordination with embedded items, mostly reinforcement steel.
If the drawings and/or the specifications are incomplete or unclear, or if not clarified through the request for information (RFI) process, the anchorages may not meet code, resulting in spalled concrete, loose railings, or severed reinforcing steel.
EOR or delegated design
The root cause of most rail post anchorage issues is a failure to identify the team responsible for anchorage design, or even that rail post anchorages need to be designed at all. It is not enough to simply specify a railing system without consideration for anchorage and without the EOR’s input on whether loading from the selected system can successfully be transmitted to the structure. No one seems to want to do the design for capability, liability, or cost reasons.
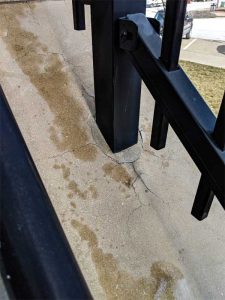
A disconnect between the design and installer/manufacturer teams often occurs because the language in the specification or referenced standard either does not mention anchorage design directly or implies the inclusion of anchorage design in the manufacturer’s installation instructions. ASTM E985, Standard Specification for Permanent Metal Railing Systems and Rails for Buildings, provides guidance specific to metal railing design. It says, railings shall be installed per product manufacturer’s specifications. However, do those project specifications include anchorage design? Manufacturers generally make sure the railings themselves meet code loading requirements and provide generic mounting details, but do not offer anchorage design.
One option the architect may select is to delegate the anchorage design to a licensed specialty structural engineer retained by the installer, supplier, or fabricator of the railing system. Before rail post anchorage design can be delegated, the EOR should review the proposed rail post architectural details, locations, and spacing to confirm a proper load path is present and the structure is capable of supporting the code-required railing loads. Although a delegated designer may be able to identify potentially problematic anchorage configurations, they are not required to confirm the structural capacity of the supporting members the railing assemblies are being anchored into. As the EOR has a better understanding of the structure as a whole, and his/her specifications and reviews are in many ways redundant to the specialty engineer’s design, it may be simpler and more cost effective to have them perform the anchorage design, thereby reducing overall effort, mishaps, and miscommunication.
● International Building Code (IBC), International Code Council (ICC), 2018. ● The American Concrete Institute (ACI) 318-14, Building Code Requirements for Structural Concrete. “Embedded Structural Steel Connections” by Charles H. Raths for PCI Journal, May-June 1974. ● ASTM E985, Standard Specification for Permanent Metal Railing Systems and Rails for Buildings. ● ASTM C1107, Standard Specification For Packaged Dry, Hydraulic-Cement Grout (Nonshrink). ● ASTM E1481, Standard Terminology of Railing Systems and Rails for Buildings. The National Association of Architectural Metal Manufacturers’ (NAAMM’s), AMP 521-01 R2012, Pipe Railing Systems Manual including Round Tube, fourth edition (2001, revised 2012). ● The United States Code of Federal Regulations (CFR), Title 29 Part 1910.23, Guarding Floors and Wall Openings and Holes. |
I would love to post this story on my website. Is that possible?