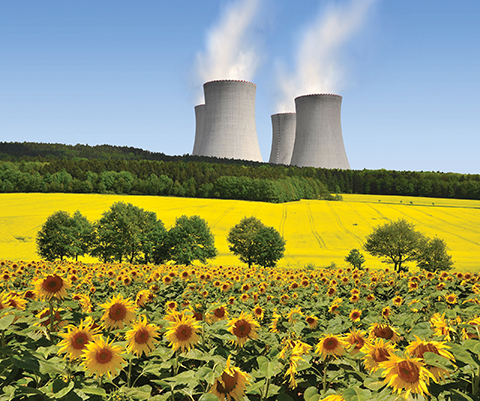
by Cheryl Higgins
The average hospital uses three times the energy of typical commercial buildings, and U.S. medical facilities spend $8.8 billion annually on energy. Between lighting, medical equipment, HVAC, and plumbing, energy consumption in medical facilities outpaces any other type of building. For large hospital systems, annual costs can reach into the tens of millions of dollars—no small amount in an industry of thin margins.
With these startling statistics it is no wonder hospitals are searching for ways to lessen their energy costs. Hospitals recognize energy conservation is a priority and also realize the benefits, both to their bottom line and the environment. One initiative that may be implemented is upgrading the fan motors in cooling towers to more efficient systems, reducing costs and maintenance.
Cooling a campus
Below a campus’ sidewalks and streets lies a vast network of interconnected pipes that carry chilled water to buildings. This water flows through the pipes seven days a week, 365 days a year, but is especially important during the hot and humid summer months, when it helps to keep a diverse array of campus buildings cool.
Larger buildings and multiple campuses usually use a chiller plant to provide cooling. In such systems, chilled water is centrally generated and then piped throughout the building to air-handling units (AHUs) serving individual tenant spaces, single floors, or several floors. Ductwork then runs from each air-handler to the zones that are served. Chilled water-based systems result in far less ductwork than all-air systems because chilled water piping is used to convey thermal energy from the point of generation to each point of use.
Having a chilling process centralized is easier and more sustainable to maintain and operate as opposed to air-conditioning units on each campus building.
The cooling tower’s primary function is to remove heat from the condenser water system transferred from the campus electric chillers. During the air-conditioning cycle, heat is removed from the campus buildings via the chilled water loop; that heat is then transferred to the condenser water system and ultimately removed by the cooling tower.
Efficiency, sustainability, and conservation are important considerations for all buildings, not just healthcare facilities. At the core of many utility operations are cooling requirements calling for the use of a cooling tower. If allowed to operate in an uncontrolled environment, the water and energy efficiencies for such additions can be costly. Further, an uncontrolled cooling tower puts the asset at risk for high repair costs and downtime for production operations. One thing is for certain, for any business the cooling tower is a significant source of capital and operational expenditures.
The cooling tower is responsible for rejecting unwanted heat from the condenser water loop to the air outside the building. Proper sizing and control of cooling towers is essential to efficient chiller operation.
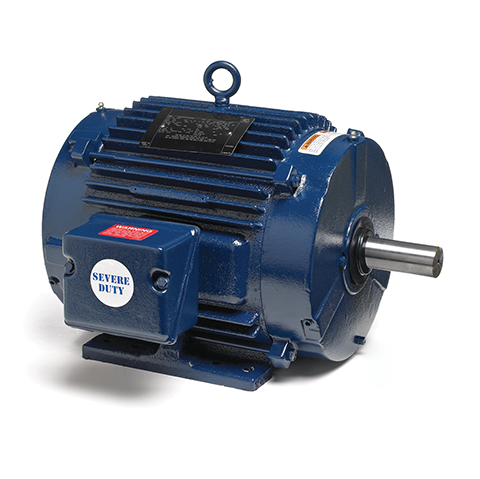
In spite of the impact on facilities, cooling towers are among the most neglected equipment. Maintenance and engineering managers might understand a cooling tower’s role, but they may not fully realize the importance of keeping them operating at peak performance levels.
Reducing costs
One of the areas where overhead can be contained or reduced is in the operation of the chilled-water systems that support air-conditioning throughout the campus or facility, specifically the cooling towers.
Mechanical-draft cooling towers consist of one or more mechanically driven fans. These fans usually have multiple blades ranging from 0.6 to 10 m (2 to 33 ft) in length. An electric motor runs the blades at relatively low speeds through reduction gearing so they move large volumetric flow rates at relatively low static pressures.
Although cooling towers are relatively inexpensive and normally consume around 10 percent of the whole system’s energy, their operation has significant effect on the energy consumption of other related subsystems. Optimizing cooling tower performance will not only increase the tower efficiencies, but also have a direct affect on other subsystems.
Thanks for sharing this advice on having the cooling tower fans replaced to make the transfer of energy more efficient. I had no idea that changing the fan could even have such a huge effect even though they are a simpler mechanic of the tower. Plus, if the replacement fans are efficient enough to reduce costs, then I think it is worth it to at least investigate that option.
Thank you for all of the helpful information you give about cutting costs on energy and cooling. That being said, you talk about how using an electric motor for cooling towers runs the blades a low speed, which allows them to move large flow rates at a low pressure. This seems like a really easy and simple way to reduce costs and keep airflow efficient.