What’s wrong with my precast concrete garage?
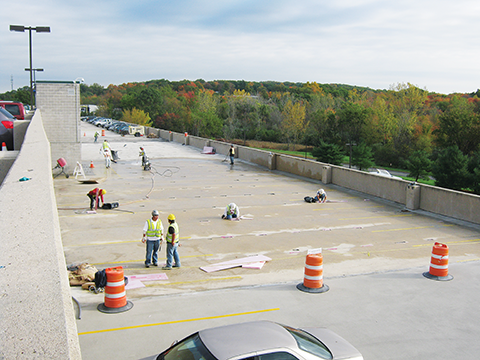
by Lawrence E. Keenan, PE, AIA
Precast double-tee construction has become a dominant method for building parking garages in North America. The double-tee beam deck system of this construction type provides a finished wearing surface, supports vehicle loading, and forms an integral part of the lateral force-resisting system. However, maintenance and repair of deck connections is a common problem with this type of construction. The most common cause is perhaps the least considered.
Connections between double-tee beams are subject to a varied array of loads from seismic events and from the deck’s temperature-induced expansion and contraction. Loading from vehicles is often regarded as small and insignificant in comparison with seismic loading—unfortunately, the effects of this cyclic deflection are not often addressed in typical precast concrete garage construction. However, over time, vehicular loading can cause widespread failure of these connections and, as such, the building codes require it be considered in design.
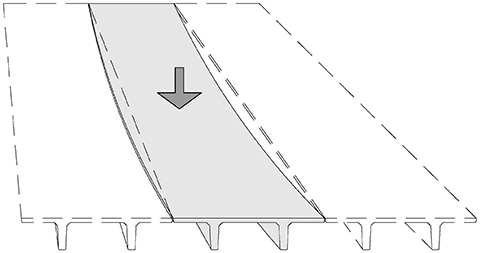
The rhythmic thumping of tires while driving through a precast parking garage is a familiar experience of modern life. As the wheel traverses each beam, load is applied, and the double-tee beam deflects downward (Figure 1).
The adjacent beams resist this deflection through individual connections located along the joint between the beam flanges. Each connection shares a portion of the load proportional to the deflected shape of the beam.
As connections close to the beam’s center resist a greater amount of deflection, they transfer more load. As the vehicle traverses across the joint, loading of the connections is abruptly reversed (Figure 2).
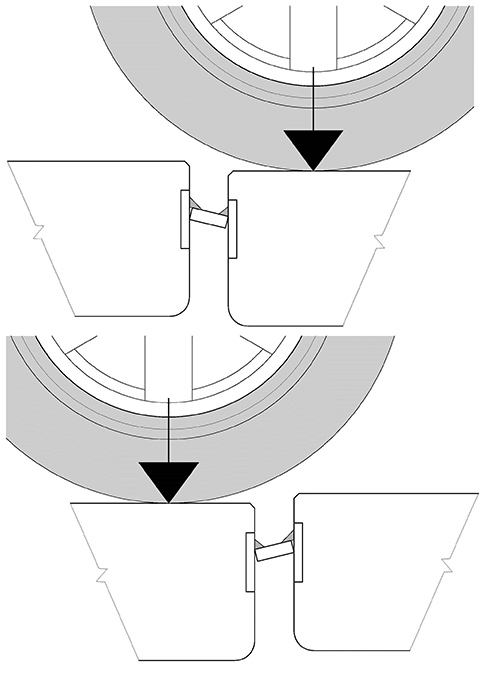
As load is applied to the connection, relative deflection of adjacent concrete flanges is resisted by a field-installed erection bar. This erection bar is fixed on either side by welds, and bending moment is applied to the welds about an axis parallel to the joint (Figure 3). This moment creates a concentration of tensile stress at the root of the weld, followed immediately by compression stress as the wheel traverses the joint. With enough cycles, this stress reversal leads to fatigue failure of the weld (Figure 4).
Fatigue
Fatigue is the process by which a material becomes weakened through cyclic loading. Over time, repeated loading leads to the development and propagation of cracks, and the eventual failure of the weld. At the microscopic level, fatigue failure occurs in three steps.
1. Crack initiation
The configuration of connections creates a severe notch at the root of the weld that is the precipitating point for crack initiation. Surface discontinuities typically cause a localized increase in stress and a nucleation point for cracks. In a welded connection, the root of the weld provides a highly irregular crevice that precipitates crack formation. In fact, many industry standards and model codes prohibit the root of the weld from being subject to tension for this very reason.
2. Crack propagation
The crack grows at this stage in a slow, stable manner—the rate of which depends on the magnitude of the stress cycle. As microscopic cracks grow into macroscopic cracks, the intact area of the weld is reduced, increasing stress on the remaining cross-section and accelerating the rate of propagation.
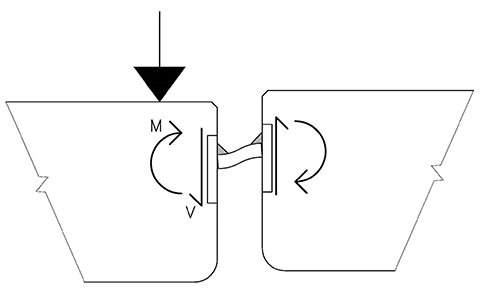
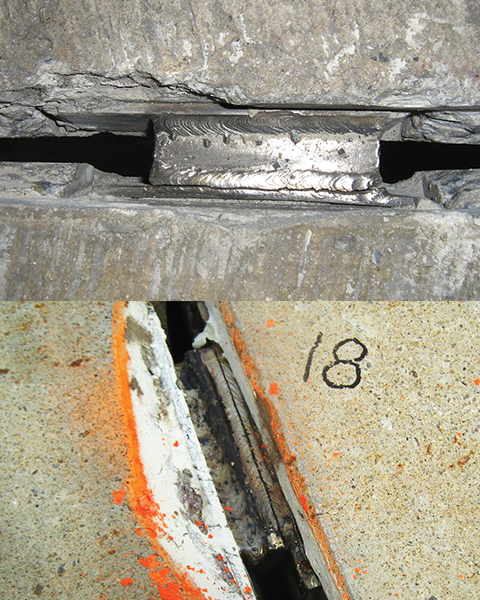