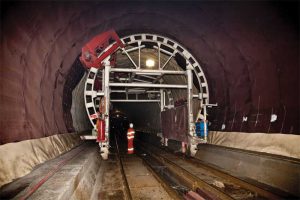
Images courtesy Dörken Systems
The type of protection clients can expect depends on the quality of the drainage membrane. The dimple height, sheet thickness, and compressive strength vary between manufacturers. Understanding the true requirements for the project will allow the selection of the appropriate drainage board. However, none of these moisture-resistive steps address the problem of moisture migrating from the footings into the foundation wall. Only proper capillary breaks on footings can stop this undesirable movement of water.
Waterproofing the world’s longest, deepest tunnel
The Gotthard Base Tunnel runs beneath the Alps as part of a new north-south railway in Switzerland. At 56.8 km (35.2 mi), it is the longest tunnel in the world, surpassing the Seikan Tunnel in Japan. The total is 152 km (94 mi), when service tunnels and other shafts are included. With an expected service life of 100 years, and without the need for major repairs for at least 50 years, this can be a challenging environment for drainboards.
The Gotthard Base Tunnel is a double-shell tunnel with a combination of waterproofing system and drainage layer between the shotcrete outer shell and the concrete inner shell. This design continuously drains away seepage water to protect the concrete shell against hydrostatic pressure, and to transfer high loads onto the concrete support structure.
Dealing with water seepage
Tunnel engineers faced prodigious challenges on this project, including dealing with hydrostatic pressure.
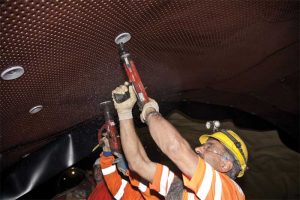
At points where the tunnel burrows under 2286 m (7500 ft) of mountain cover, geothermal processes send alkaline and acidic seepage water that could be as hot as 45 C (113 F).
To handle these intense conditions, the world’s longest tunnel uses HDPE drainboards manufactured specifically for the project. These drainboards improve waterproofing by relieving hydrostatic pressure that builds up against subterranean surfaces.
Although installed in a relatively harsh environment, HDPE drainboards can retain their integrity for many decades despite unprecedented physical, mechanical, chemical, and biological demands. Since the tunnel is engineered to not require major maintenance for 50 years, the aging processes of polymeric products must be minimal.
Higher performance demands new testing
The anticipated challenges for the tunnel’s drainage systems were such that new testing methods had to be developed to address the unique qualities of the Gotthard base tunnel.
Traditional testing methods were reinforced by newly developed procedures that evaluated:
- aging characteristics in oxygen-enriched, high-temperature water;
- the simultaneous impact of horizontal shear and lateral loads;
- compression creep involving rough surfaces; and
- installation issues that are related to concrete outer shell construction.
The testing was conducted by a third-party using the International Organization for Standardization (ISO) tests, and was subject to the approval process of the tunnel authority.
The Gotthard Base Tunnel was a demanding project with extreme conditions. The test program comprised existing test methods that were augmented by additional procedures, such as aging resistance in oxygen-enriched water at elevated temperatures, compression creep tests between rough surfaces, tests under combined lateral loads and horizontal shear, as well as installation tests including the construction of the concrete support shell.
The selected drainboard was exposed to a variety of extreme conditions, including water heated to temperatures of up to 70 C (158 F). The drainboards were also tested using 50 C (122 F) acidic water containing ½-percent sulfuric acid and 50 C alkaline water saturated with calcium hydroxide. Oxygen-enriched water circulated at 70 C further tested the durability of the drainboards.
Samples were aged over a period of 24 months. During the aging period, the specimens had been submerged in acidic and alkaline solutions and in oxygen-enriched water before retesting. All required product specifications needed to confirm the aging properties could be met.
Conclusion
A water-managed foundation system prevents moisture buildup at the foundation wall. When there is no hydrostatic pressure, there is no need to worry about water seeping through potential cracks and pores in the concrete that will lead to mold and other moisture-related problems.
The read above very educative throws more light into waterproofing in foundation which is a common experience around Lagos.
I must agree with you that this piece is quite enlightening.