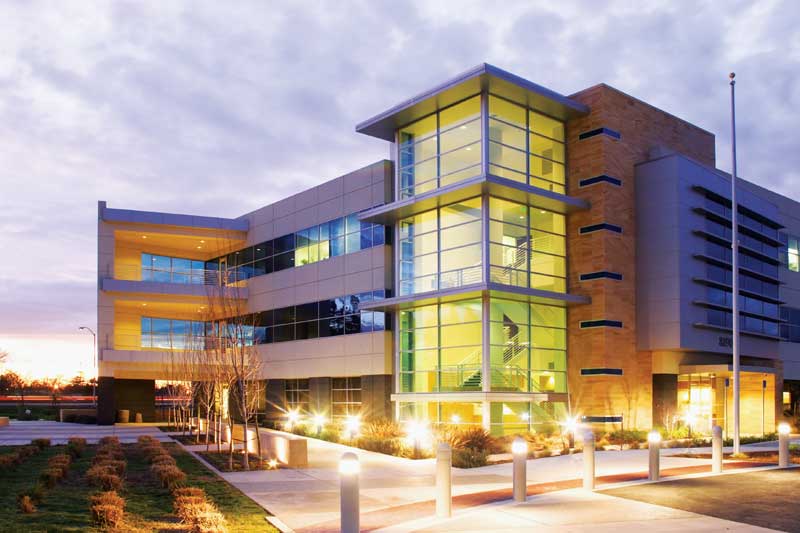
by David Cook, RA
Among its many functions, the exterior envelope typically must control the movement of heat, air, bulk water, and water vapor both in and out of a building. Over time, various systems and components have been developed to control this movement.
In a properly functioning envelope, these systems work together to maintain the building’s temperature and allow components to dry quickly if they become wet. While these systems contribute to overall performance, they also contribute to the complexity of the envelope design and sensitivity to error.
Recent editions of the model codes have increased requirements for thermal insulation, and heightened the base level of acceptable performance for air barriers and vapor retarders. Increasing energy costs have also caused building owners to demand better performance. If one of an envelope’s systems is improperly designed or installed, the increased performance of the other systems may reduce the resulting envelope’s capacity to dry. This may heighten the potential for problems to occur (Figure 1).
An exterior envelope usually contains the following four systems:
- thermal insulation to control the movement of heat through the envelope;
- air barrier to control air leakage through the exterior envelope;
- bulk water-resistant barrier (WRB) to prevent uncontrolled water leakage into the building; and
- vapor retarder to reduce moisture diffusion through the building envelope components.
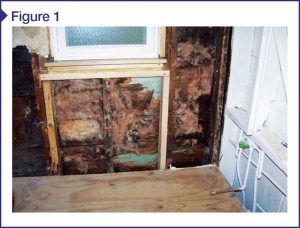
Images courtesy CTLGroup
Preventing uncontrolled bulk water leakage into a building has long been recognized by the model codes, which contain verbiage addressing this requirement. While bulk water penetration remains a common problem, the causes associated with this construction anomaly are fairly well understood. Moreover, the code bodies have made little to no changes regarding this subject. Therefore, this article does not detail components associated with the control of bulk water (except as they pertain to the other three systems).
Concentrating on the thermal, air barrier, and vapor retarder systems, this article details recent changes in the International Building Code (IBC) or the International Energy Conservation Code (IECC), along with potential design and installation problems. In referencing the code, the prescriptive requirements will be noted because they offer the clearest comparison of the changes—the alternative compliance options are unlimited, but the prescriptive requirements serve as their basis.
Thermal performance
Heat moves through a building envelope through both opaque and transparent portions. While code requirements for thermal performance of fenestration products—including solar heat gain coefficient (SHGC), visible transmittance (VT), and U-value of the glazing—have increased, this article concentrates on opaque areas of the building envelope.
Thermal energy’s movement through the opaque envelope portions are resisted by insulation. All materials have some thermal properties, but some are better insulators than others. Thermal insulation material is measured by its R-value—the inverse of thermal conductance, which is the number of Btus transmitted through a 305-mm (12-in.) square piece of 25-mm (1-in.) thick material, with one degree of difference between the two sides of the material. In the United States, the R-value is measured in Imperial units, therefore it is an abbreviation of hr*sf*F/Btu.
The higher the R-value, the better its resistance to heat flow. For example, 25 mm (1 in.) of concrete has an R-value of 1, while 25 mm of foil-faced polyisocyanurate (polyiso) rigid insulation has an R-value of 7.2. Un-faced fiberglass batt insulation has an R-value of 3.14 per inch. Since R-values are additive, the resulting R-value of 89 mm (3.5 in.) of fiberglass batt insulation in a 2×4 stud wall cavity would be approximately R-11. When the R-values of the exterior sheathing and interior gypsum board are added, the R-value of an unclad 2×4 frame wall can approach R-13, depending on the sheathing material and thickness.
From 2006 to 2012, IECC increased the required R-value in most portions of the building envelope in all zones. For example, the requirement for above-grade wall insulation in Zone 6 went from R-19 to R-21 +R-5. The +5 is a requirement for continuous insulation (ci) with a rating of R-5 on the exterior of the framing.
The call for ci in the building envelope has made a large impact on exterior wall design and construction. The requirement was added to help eliminate thermal bridging caused by framing members or other wall components extending through the insulation in a conventionally insulated wall cavity. Thermal bridging was shown to reduce the cladding’s overall thermal performance.
Good article but any discussion about wall assemblies with continuous insulation that do not include any mention of NFPA 285 are missing a key consideration when developing wall types. The requirements for 285 and potential solutions, strategies, materials, assemblies, etc. would be a good subject for future discussions.
Including discussion of Passive House Institute of the United States (PHIUS) metrics specifying standards for building performance would be an appropriate addidition to this article. A key component in Passive House construction is the use of energy recovery ventilation systems (ERV). These devices provide continuous 100% outside air to habitable spaces and neutral pressure differential between inside and outside conditions important in extremely tight; 0.6 ACH air barrier construction required by PHIUS certification. I applaud the reference to the use of WUFI software to access the hydrothermal performance of wall systems over time.