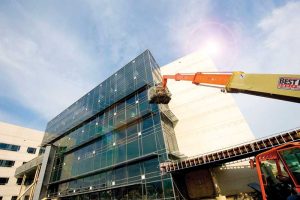
Soil testing
- Moisture content
- Specific gravity test
- Dry density test
- Atterberg limits test
- Sieve analysis
- Modified or standard proctor
- Bearing ratios
- Chloride or sulfide testing
- pH testing
- Permeability testing
Asphalt testing
- Mix evaluation
- Stability
- Flow
- Bulk specific gravity
- Extraction
Masonry/Concrete testing
- Flex strength testing
- Compression strength testing
- Unit weight, tensile testing
- Absorption
- Efflorescence testing
- Mix design
- Structural masonry testing
Whether performed in the field or laboratory, the key takeaway is that applicable testing performed at appropriate intervals during construction provides an important complement to pre-testing, and a final assurance of the quality and performance of the critical materials and assemblies that make a sound project. Both types of testing in tandem with regular inspections to monitor the progress are ways to perform quality checks on the project.
Regulatory requirements
Construction material testing is a regulatory requirement for most large-scale building projects. Specific codes and regulations applicable to building materials vary from state to state, but there are common oversight organizations, including the American Society for Testing and Materials (ASTM) International, United States Army Corps of Engineers (USACE), Federal Aviation Administration (FAA), and the American Association of State Highway and Transportation Officials (AASHTO). To gain approval for a project, contractors work with licensed and accredited construction material testing professionals before breaking ground.
Ensuring the use of the right materials
Building codes, location, and the land being built upon can impact the quality of materials. To reiterate, product testing is completed on finished products prior to being shipped to a construction site. Material testing is done on the construction materials on-site, then tested and inspected periodically throughout
the process for both quality control (QC) and quality assurance (QA).
Highlight risks
By testing materials in the field, starting with the foundations, project managers can be immediately notified of any problems, allowing them to take corrective action with limited cost impacts and schedule delays.
If material testing and inspections are not performed, unseen deficiencies may result in failures long after construction is completed, leading to litigation and other serious consequences. Potential problems include non-compliance with building codes, mold, rust which could lead to material deterioration, and moisture, which could cause serious structural failures.
Avoid costly mistakes
Think of material testing and inspections during the construction process as an “ounce of prevention.” The efficacy of periodic testing throughout the building process and the upfront costs are small compared to the potential cost of failures. Such precautions will save the time and expense of redoing any work, avoid litigation, and worst-case scenario, building malfunction or collapse.