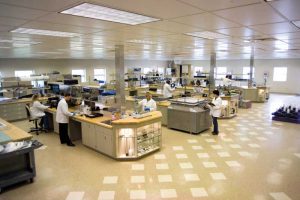
Increase safety
Think of material testing and inspections as extensions of safety gear. Just like helmets, goggles, vests, and so on, these tests are designed for protection. While the results may not seem immediate, ensuring the materials are structurally safe by testing and inspecting throughout increases the structure’s overall safety and integrity.
Asking the right questions
Frequently, manufacturers and owners request a specific test, believing it is all they needed to determine whether the product will succeed in its intended use. A quality testing lab should always challenge this assumption and ask questions such as: What are the company’s goals with the product? What market do they want to be in and why? How will the presented product perform in a particular market? What is the longevity of this product? The product approval process is likely different from what was originally envisioned.
Architects and general contractors are buying performance, not a product. The testing lab’s job is to assure the product will perform as promoted. By taking the long view, a manufacturer can save time and money as well and offer a certified product which can compete effectively in the desired construction material’s marketplace.
Component complexity simplified
Many of today’s new products are made from several components working together to achieve a singular performance goal. For instance, in a window, the glass may come from Europe, the aluminum from China, and the locking mechanisms from South America. Since all these products must first meet their own set of performance requirements, it is unreasonable to expect the window manufacturer to coordinate and oversee the testing of the components to comply with the performance objectives of the window as a whole assembly. Testing reports for each component will need to comply and reconcile as international regulations may vary. Such complicated details are better left
to the materials testing experts rather than the product manufacturer.
A sophisticated testing facility can coordinate these details into one testing plan which meets the objectives, eliminating the product manufacturer from the effort to “trace and chase” paperwork to sell their windows.
Wrangling the big idea
Product manufacturers are excellent at creating new and innovative solutions. However, for the whole product to align with each component’s capability,
it is critical to share the design with the component team. They are the experts in their own products, and they may offer solutions to avoid unforeseen problems. Ask them whether part A will work with part B, as there can be multiple points of failure.
Many manufacturers feel it is not their problem or responsibility to oversee components if their “part” works. However, most component manufacturers would be happy to provide their advice free of charge, which could save time
and money. Inviting them to the testing lab can be helpful as they are valuable resources and not just vendors.
Component compatibility
Component incompatibility is often the main problem when it comes to testing. Even after the advance work and partnering with the component team, no one knows how the product will perform until it is tested, because a single test is worth a thousand opinions. Testing exposes the weaknesses in the system, and a quality lab can pinpoint those weak spots and give ideas on a remedy.
If possible, test “beyond the code” of the minimum required standard. By exploring the outer limits of the product standards, manufacturers can sometimes elevate their products into new markets or meet previously unforeseen performance requirements. It is important to remember, tests are a great barometer of how a product will perform, but field testing is the final frontier. In conclusion, product testing above the required standard reduces the risk of failures in the field.