IAQ goals and performance-based material selection
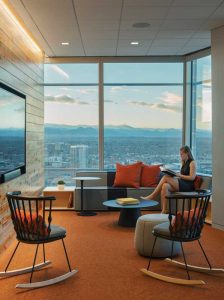
When selecting and specifying ceiling systems to support IAQ goals, consider the material’s properties and performance.
For commercial interior ceiling systems, the most common material choices are often selected first for their appearance:
• Wood—warm, inviting, natural look with tactile qualities, enhanced with stains and coatings.
• Metal—modern, high-tech appeal in metallic tones, painted in a full spectrum color, or finished to mimic natural wood.
• Gypsum and plaster—smooth, monolithic, modern aesthetic; mostly in white.
• Fiberglass—slightly textured surface with yellow substrate; mostly in white.
• Wet-felted mineral fiber—fissured surface; mostly in white.
• Stone wool—smooth or lightly textured surface; mostly in white.
If appearance was the only consideration, most design professionals would prefer the smooth, white plaster ceilings. It is often impractical because it provides no access to the plenum above it, and it is highly sound reflective. Acoustic ceiling panels installed in a ceiling suspension system create a gridwork with access to the plenum.
Within the suspended ceiling system, design and specification professionals then weigh the panels’ aesthetic attributes against their four key IEQ elements and other performance requirements.
Light reflectance
White ceiling panels, especially those with smooth surfaces, have a high light reflectance. This means natural light from an exterior window can be reflected more deeply into a building’s interior. Maximizing daylight reduces the demand for electric lighting, which improves energy efficiency and lessens the associated costs and emissions for lighting and cooling the building.
Whether from natural or electric sources, the light reflected off the ceiling panel will be diffused. This helps reduce glare on monitors and screens. Glare can cause eye strain, headaches, and other stress-related issues. Diffused light aids in a more comfortable, productive environment that supports people’s well-being.
In most commercial settings, including those projects seeking LEED v4.1 certification, ceiling panels with a light reflectance of 0.85 or more is the preferred specification.
Flame and smoke spread
The National Fire Protection Association (NFPA) notes “most fire deaths are not caused by burns, but by smoke inhalation.”
Two key measurements are used for interior ceiling products and assemblies in helping protecting people and properties by minimizing the effect of fire, smoke, and related hazards: flame spread index and smoke developed index.
The highest performance specification as required by the 2021 International Building Code (IBC), Section 803, is a Class A fire rating with a flame spread index of zero to 25 and a smoke developed index of less than 450. Materials with a Class A designation may ignite, but will not spread a flame and will not release excessive smoke that could obscure visibility during an emergency egress event.
Prioritizing performance
Selecting and specifying ceiling materials considers all four elements of good IEQ—acoustics, IAQ, lighting, fire protection—and more. As examples: fiberglass ceiling panels have an acceptable appearance, good sound absorption, and are lightweight, but if there was a fire, they would melt at a low temperature. Wet-felted mineral fiber panels’ acoustic fissures help with sound absorption, but are considered by most designers to have a dated, unattractive look, and need added chemicals to resist fire and mold.
Stone wool ceiling panels have a smooth non-fissured surface and provide high sound absorption. The panels are manufactured with natural basalt rock and recycled materials. Further, because it is made of stone, there is no need to add flame retardants or antimicrobials to achieve the desired performance. Stone wool withstands temperatures up to 1200 C (2200 F) and has a smoke developed index of 5. Similar to stone wool’s properties, metal also does not need additional chemicals to resist combustion or potentially harmful microorganisms.
Mold and moisture
Ceilings composed of organic fibers and water-based materials need to add a biocide, fungicide, or antimicrobial to help protect against the mold and mildew. With the added chemicals, these materials may become a potential pollutant source contributing to poor IAQ.
Keep in mind products that add antimicrobials are inhibiting the growth of microbes, such as mold spores. There is little evidence antimicrobial surface treatments prevent or reduce the spread of viruses or result in healthier populations. The disadvantages of using antimicrobials can include increased resistance to antibiotics, a false sense of security, and increased costs.
Mold also has a cost. Left to propagate, mold can negatively affect people’s health, products’ performance, and appearance, and eventually, buildings’ structural integrity and long-term value. Mold thrives when a spore lands on a surface where organic food (such as fibers, starches, and cellulose) and moisture are present, and temperatures are 5 to 38 C (40 to 100 F). Mold can grow rapidly in as little as 24 hours.
Stone wool and metal are inherently mold-resistant materials, and easy to clean without harsh chemicals. They are not organic and, therefore, they do not provide sustenance to mold, mildew, bacteria, fungi, and other microorganisms. They also do not absorb water, moisture, or humidity.
Beyond mold mitigation, ceiling panels that resist moisture and humidity do not sag, warp, rot, or fall out because of water absorption. Hydrophobic materials like stone wool support good IAQ by alleviating concerns associated with supplemental natural ventilation from operable window systems, or when HVAC systems are turned off when the building is unoccupied. This moisture-resistant attribute also can assist during buildings’ construction schedules by allowing ceilings to be installed prior to the envelope being completely sealed or the HVAC system made operational.
VOCs and low-emitting products
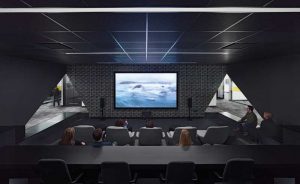
Water, mold, viruses, and bacteria are all naturally occurring challenges. Volatile organic compounds (VOCs) are also released from many natural sources. These organic chemical compounds are used in thousands, possibly millions, of products.
According to the EPA, “Concentrations of many VOCs are consistently higher indoors (up to 10 times higher) than outdoors.” The health impacts of long-term exposure to high levels of VOCs may include:
• Eye, nose, and throat irritation;
• Headaches, loss of coordination, and nausea;
• Damage to liver, kidney, and central nervous system; and
• Cancer.
To reduce the risk of these health impacts and bioaccumulation on building occupants, design and specification professionals are selecting materials and products with the lowest level of VOC emissions. Two trusted resources are the UL Environment’s GreenGuard certification program, and the ILFI’s Declare Label 2.0 transparency platform and product database.
Thank you for highlighting the important role of acoustic ceilings on the health of occupants. Their insights are invaluable in creating spaces that prioritize both comfort and functionality.