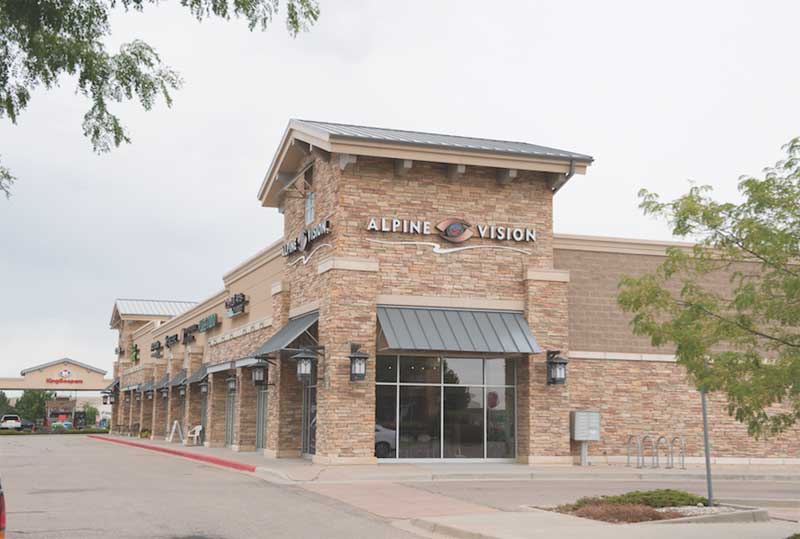
Minimizing saturation time
All cladding is exposed to water or snow at some point. AMSV, like other masonry products, is designed to stand up to normal precipitation and seasonal weather. However, for an installation that performs well in wet and freezing weather, minimizing saturation and providing adequate drainage are vital.
Kickout and other flashings
Kickout flashing is critical in the installation, as it keeps roof runoff rainwater from being directed at the wall. If kickout flashing is installed improperly (or not at all), the roof water force is such it can penetrate the cladding and enter the wall. (Further information is available through International Association of Certified Home Inspectors, at www.nachi.org/kick-out-flashing.htm.) In general, flashing should be used at any penetration, termination, or transitions of the wall.
Capping
Good water management principles govern the transitions between materials. Caps provide a protective sloped surface for different levels and indents along the exterior, and shelter the wall from harsh weather effects such as rain, snow, and ice. (More on coping is available via PaverSearch’s “About Wall Caps and Coping,” at www.paversearch.com/coping-caps-introduction.htm.) For example, if lap siding such as cedar or vinyl is used on the top half of an exterior wall with the bottom portion installed as AMSV, a cap and flashing should be installed that overhang the veneer installation by 38 to 51 mm (1 ½ to 2 in.) to divert water and minimize saturation. If possible, there should be a drip edge or drip kerf feature on the cap to force water to drop off promptly at the cap’s outer edge.
Moisture management
Rising damp can occur when AMSV is installed in contact with the ground. Moisture rises up through fine pores in masonry, including manufactured stone, in a wick-like fashion, known as capillary action. It is not uncommon for wicking water to rise as much as 1016 to 1270 mm (40 to 50 in.). Rising damp can result in crumbling mortar, efflorescence, and damage to AMSV, and if extensive, it can cause structural failures. (Learn more by consulting the article, “Rising Damp: How to Recognize It and What to Do” at dengarden.com/cleaning/Rising-Damp-Overview.) To prevent rising damp, a 101-mm (4-in.) clearance from grade and 51-mm (2-in.) clearance from paved surfaces should be maintained.
Water, snow, and repeated freeze-thaw cycles can all cause spalling, hairline cracks, and general deterioration of AMSV if the proper installation techniques are not followed. Running AMSV to or below grade invites failure—while it might make the installation look more realistic, this may affect warranty coverage and is a potential violation of the International Building Code (IBC), which has clearance requirements for adhered stone veneer under Section 1405.10. Clearance is required to allow drainage to occur, prevent moisture from wicking up the wall, minimize soil staining and efflorescence, and—in some areas—provide termite inspection zones.
Even when AMSV is installed properly above grade, standing water can wick into and behind the siding, causing extensive damage. Eliminating standing water—for instance, by sloping the grade away from exterior walls—prevents this type of moisture issue. Swales are also a simple way to direct water away from exterior walls, and underground drains in low-lying areas are effective in preventing water from accumulating near the foundation.