Potential with UHPC
One way to address the longitudinal cracking in adjacent box-beam bridges is to use an improved grouting material with enhanced tensile and bond strength. Ultra-high-performance concrete represents a new class of concrete that has high strength and durability characteristics. It has been defined as a cementitious composite material composed of an optimized gradation of granular constituents, a water-to-cementitious materials (w/cm) ratio less than 0.25, and a high percentage of discontinuous internal fiber reinforcement.
The mechanical properties of UHPC include compressive strength greater than 21.7 ksi (150 MPa) and sustained post-cracking tensile strength greater than 0.72 ksi (5 MPa). The material has a discontinuous pore structure that reduces liquid ingress, significantly enhancing durability compared to conventional concrete.
Due to its properties, UHPC has been investigated as a grouting material in connection joints. The continent’s first bridge relying on this application is a skewed 24.38-m (80-ft) single span overhead bridge in Rainy Lake, Ontario. UHPC was also employed elsewhere in Ontario with a non-corrosive glass-fiber-reinforced polymer (GFRP) rebar in the longitudinal and transverse joints of the three-span side-by-side Eagle River Bridge. Additional GFRP rebar was also added to the transverse joint to assist with load transfer. The UHPC was placed successfully and the required strength was provided after the curing period.
One of this article’s co-authors has investigated the behavior of a pair of box beams under live and temperature gradient loading using finite element modeling. Two shear key configurations (partial and full depth) containing dowel bars spaced at 102 mm (4 in.) on center (oc) were employed to connect the box beams. The partial-depth shear key model was calibrated using the laboratory results from two adjacent box beams tested at the Turner Fairbank Highway Research Center (TFHRC).
The full-depth shear key was modeled using the same parameters as the partial-depth key as no experimental data was available at the time of modeling. The maximum principle stresses in
the shear keys and dowel bars were investigated. The results showed the maximum principle stresses increased in the partial-depth shear key after applying the temperature gradients. However, there was a decrease in the maximum principle stresses for the full-depth key. Also, shear keys exhibited larger principle tensile stresses as dowel bar spacing increased, although the partial-depth shear key exhibited less tensile stresses than the full-depth key. The principle stresses in the dowel bars increased with the inclusion of temperature gradients for both shear keys. Both shear key configurations experienced differential deflection less than 0.51 mm (0.02 in.).
Based on the experimental results from the TFHRC and the finite element modeling, a UHPC shear key with the same shape and with 102-mm (4-in.) dowel bar spacing was used in the design of a bridge constructed last summer in Fayette County, Ohio. To understand the behavior of this bridge with a new longitudinal shear key joint, it was instrumented in multiple locations. The bridge was tested and monitored to investigate its behavior due to live and environmental loads.
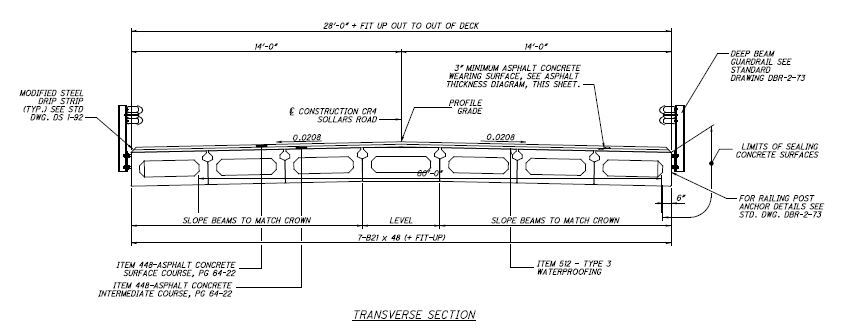
Bridge description
The bridge was constructed on Sollars Road, near the town of Washington Court House. The bridge consists of seven adjacent box beams and has a total length of 18.6 m (61 ft) and width of 8.5 m (28 ft). Each box beam is 1.22 m (4 ft) wide and 0.53 m (1 3⁄4 ft) deep (Figure 1).
Twenty-eight 13-mm (1⁄2-in.) diameter seven-wire low relaxation strands with a 1860 MPa (270 ksi) ultimate strength were used for prestressing in each box beam. The mild reinforcement (used primarily for shear) had 414 MPa (60 ksi) yield strength. The box beams have a diaphragm at each end that is 0.84 m (2 3⁄4 ft) in length. The ends of the beams rest on two bearing pads, and are connected to the abutments using a tie rod. The bridge did not have transverse tie rods which is common practice in Ohio. Further, neither transverse post-tensioning nor a composite deck were utilized.
The bridge incorporated the new shear key design developed and tested at the TFHRC. The new design consisted of using UHPC as the grouting material with equally spaced dowel bars in each joint. The new shear key was larger than the typical shear key. It employed used dowel bars that were threaded into the beams and staggered at 102-mm (4-in.) spacing.
The testing at TFHRC involved connecting two box beams together and applying a concentrated load. The results show the new design was sufficient to make the bridge behave as a unit, and no cracks were recorded in the shear keys even after numerous loading cycles. Finite element modeling, along with a parametric analysis, was also performed for the tested beams and it was shown larger spacing of the dowel bars could be used. However, the same dowel spacing was employed in the bridge in an attempt to replicate the laboratory conditions.
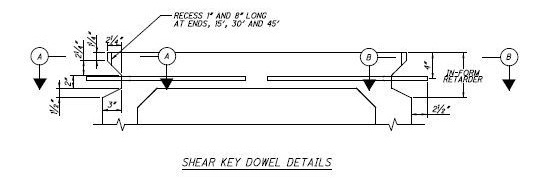
The dowel bar system had two parts, where the first part is embedded in the beam 460 mm (18 in.) and contained a female threaded end. The part embedded in the shear key had a length of 120 mm (4 3⁄4 in.) and had a male threaded end, allowing it to be screwed into the part embedded in the beam. Similar shear key designs have been used in bridges in Ontario, although no data exists to quantify the performance of this type of shear key design. Figure 2 shows details of the shear key.