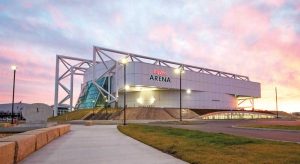
Before fenestration products arrive at the jobsite, they are finished under factory-controlled conditions to uphold the specified performance and warranty requirements. For complete coating coverage, an electrostatic spray application production line is used for architectural aluminum extrusions, flat sheets, and fabricated parts.
To ensure strong adhesion, the metal is first cleaned, pretreated, rinsed, and dried. After pretreatment, the material falling within certain size parameters is racked onto a carrier system and moved through the liquid paint finishing line. Oversized material requires off-line finishing, which can add extra time and cost.
Once the paint is applied to the aluminum, the solvent’s function is complete. Since some of the solvents used are considered volatile organic compounds (VOCs), they must be carefully managed within the finishing facility. Responsible liquid paint coating applicators use a 100 percent air capture system with a regenerative thermal oxidizer to carefully capture and safely destroy the VOCs, repurposing their energy within the factory. This process ensures there is no adverse environmental impact, and no VOC-related health risk for the product installer, building owner, or occupants.
Before it leaves the factory, the coated and racked material moves to the curing ovens where it is closely monitored to reach peak metal temperature. For proper cure of 70 percent PVDF resin-based coatings, the finished aluminum must reach approximately 232 C (450 F) for at least 10 minutes depending on the material’s thickness and each paint coating’s specific specifications.
Quality assurance (QA) tests coupled with reducing material handling through automation allow for an efficient, uniform, consistent coating application. Large finishing service providers invest in automated conveyer carriers, numerous spray booths with rotary atomization bells, and control panels. Automating these processes and color changes conserves paint, reduces waste, improves quality, and fulfills the order accurately and quickly.
Specification guidelines for performance and durability
The Fenestration and Glazing Industry Alliance (FGIA) published three industry standard specifications for architectural coatings on aluminum extrusions. These documents were updated in 2022.
- AAMA 2603-22, Voluntary Specification, Performance Requirements and Test Procedures for Pigmented Organic Coatings on Aluminum Extrusions and Panels (with Coil Coating Appendix). AAMA 2603 provides the least stringent specification, pertaining to one-coat baked enamel coatings without a primer. It usually is reserved for interior applications where color retention, chalk, fade, and weatherability is not required.