-
For Washington University’s James M. McKelvey, Sr. Hall, to safely remove the volatile organic compounds (VOCs) in the liquid paints’ solvents, the finishing service provider used a 100 percent air capture system and regenerative thermal oxidizer.Photo by Paúl Rivera/courtesy Apogee, Linetec, Tubelite, and Wausau Window and Wall Systems. AAMA 2604-22, Voluntary Specification, Performance Requirements and Test Procedures for High Performance Organic Coatings on Aluminum Extrusions and Panels (with Coil Coating Appendix). AAMA 2604 provides intermediate performance, pertaining to 50 percent PVDF resin-based, two-coat systems with a primer and color coat. The resulting finish offers good color and gloss retention, hardness, and abrasion resistance suitable for storefront, entrances, and other high-traffic areas.
- AAMA 2605-22, Voluntary Specification, Performance Requirements and Test Procedures for Superior Performing Organic Coatings on Aluminum Extrusions and Panels (with Coil Coating Appendix). AAMA 2605 provides the highest performance, pertaining to 70 percent PVDF resin-based coatings. This includes two-coat systems, and three- and four-coat systems for metallic and exotic colors that require a clear topcoat and sometimes, a barrier coat. The resulting finish offers outstanding color and gloss retention, hardness, and abrasion resistance, suitable for curtain wall and monumental architectural projects.
High performance PVDF coatings and warranty considerations
Finishes that meet AAMA 2605 exhibit exceptional durability and resistance to humidity, color change, chalking, and chemicals. They perform as specified when exposed to ultraviolet (UV) radiation, pollution, and weathering. The rigorous testing of these PVDF coatings includes more than 4,000 hours of accelerated exposure to salt spray. In addition, 70 percent PVDF painted aluminum samples have been placed on an outdoor test site in South Florida. These test panels are monitored under actual coastal conditions for years, even decades.
The shape and machining of aluminum can affect how it responds to salt-spray in coastal areas. Issues are more likely to occur at grain lines and flaws in fabricated metal. Seams, hems, cut holes, and ends also are potentially vulnerable. For best results, ensure the metal is machined, bent, and shaped before it is finished.
Once installed, any fabricated aluminum that holds moisture and prevents drainage also can create prolonged exposure to salinized solutions that may expedite corrosion. Be aware of concave components where water can collect, or insufficiently sized or blocked weepholes on curtain wall, storefront, and window systems.
Finishes applied to meet AAMA 2605 should last several years beyond, and in some cases, beyond the warranty period. Warranties for finishes typically address color fading, chalking, adhesion, and gloss loss, but they do not mention corrosion. This is because the warranties are for the finish itself, not the underlying metal where corrosion could take place. PVDF 70 percent resin-based architectural coatings applied by an experienced finishing service provider can help protect fenestration products’ architectural aluminum framing from corrosion, even if it is not explicitly stated in the warranty.
Care and maintenance
With an architectural-grade factory-applied coating, aluminum requires little maintenance to uphold its appearance and performance. Regular cleaning helps remove accumulated deposits from salt-spray, soil, and pollution.
Usually, finished fenestration should only require a rinse with clean water, or at most, a rub with a soft cloth and mild soap solution. Specification professionals should inform building owners that strong alkaline or acidic cleaners and abrasive metal scrapers should be avoided, as they can damage the finish and expose the underlying aluminum to future salt spray. When a finish is compromised, the negative effects to the metal substrate may become significant within weeks.
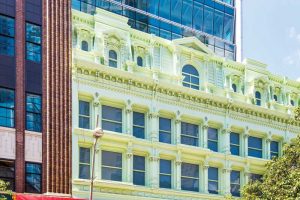
For small scratches, touch-up paint may be used. Experienced finishing applicators retain the paint formulation of customers’ orders and may be able to match the finish on the original material. Specialty colors, micas, metallics, textured finishes, and spatter coat may not be possible to match and could require replacement. Some factory finishing service providers also provide qualified field service, restoration, and repair teams to assist with projects in need of on-site attention or renovation.
Specified and applied to meet AAMA 2605, 70 percent PVDF resin-based architectural finishes for aluminum-framed fenestration allow for nearly unlimited aesthetic options with the highest available performance, as well as a long service life.