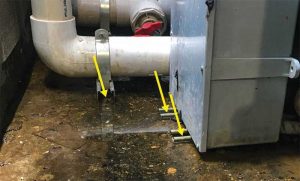
The authors recommend the use of geofoam as a method to construct and support the wearing surface. Though not unreasonable for a ramp, it is not preferable to be employed to support large areas of the raised deck on an amenity roof. This is because, even if a drainage composite is provided between the geofoam and waterproofing and the waterproofed zones include a sufficient quantity and layout of drains, future access into the interstitial space (e.g. to repair or maintain the waterproofing) would be restricted by the presence of the foam.
Child care and playground surfaces
Child care and playground facilities are incorporated, for their functional and business opportunities, on some larger-scale amenity rooftops. With child care and playground facilities, designers often specify a poured-in-place rubber-wearing surface, not only for comfort and minimal maintenance, but also for compliance with playground safety standards such as ASTM F1292, Standard Specification for Impact Attenuation of Surfacing Materials Within the Use Zone of Playground Equipment. The use of monolithic rubber-wearing surfaces, however, requires close coordination with the overall drainage design strategy of the rooftop amenity space. The authors investigated a building with a rooftop rubber-wearing surface experiencing water leakage into the lobby below during heavy rain. The authors’ found the waterproofing at the structural deck level appropriately included drains integrated with the waterproofing, but the presence and relative impermeability of the rubber-wearing surface over the drain products precluded surface water from readily reaching the drains (Figure 7). Since the perimeter base flashing around the amenity roof area only extended 203 mm (8 in.) above the waterproofing elevation (which was approximately 15 mm [1/2 in.] above the wearing surface elevation), ponding rainwater against the perimeter wall easily overtopped the hot-rubberized asphalt base flashing. Although the base flashing would have some ability to resist hydrostatic pressure, the seams of the self-adhered membrane weather barrier above it were no match for exposure to standing water.
In this case, the provisions for water to bypass the rubber surfacing and reach the drains should have been included in the design, and the base flashing detailed to reach a reasonable height (e.g. 203 mm [8 in.]) above the wearing surface, not the structural deck. Regarding surface drainage, designers should carefully navigate the design options. Simply specifying a bi-level promenade drain, though appropriate for similar applications (e.g. split-slab construction), may be inappropriate for the child care/playground application given the ‘hard point’ (and associated risk for injury) associated with the exposed body of the drain frame and grate. One option to consider would be to slope the rubber surfacing (to the extent permitted by applicable regulations) away from areas of the playground accessible to children and below a guardrail that permanently cordons off the exposed components of the drain product to playground occupants other than maintenance personnel.
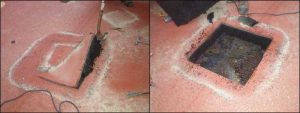
Athletic-wearing surfaces, putting greens, and pet relief areas, also popular selling points of amenity roofs, warrant similar design attention from the standpoint of providing unimpeded surface and structural deck level drainage. Additionally, these amenities warrant design attention toward protecting the waterproofing-level drain inlets of the drain product from clogging (e.g. from crushed rubber athletic surface overburden) using a filter fabric with appropriate permeability to wrap the perforated drain extension.
Conclusion
Coordination among design professionals is vital in the context of amenity roofs. Going forward, this coordination will become increasingly challenging, as some jurisdictions begin to adopt regulations directly applicable to amenity roofs such as stormwater retention performance and vegetated areas (already common in the authors’ market of Washington, D.C.). Such regulations will cause design professionals to further broaden the scope and duration of coordination exercises, especially since the amenity features described above are conventionally procured with delegated design (i.e. very late in the design phase if not during the construction phase) and will have disparate design development schedules with amenities like stormwater/green area ratio, that require finalizing of design prior to project permitting. Additionally, hydraulic-related regulations such as stormwater retention are bringing new parties like the civil engineer to the rooftop amenity design process. Finally, intense weather events, which impart heavy demands on the complex waterproofing and drainage systems associated with amenity roofs, show no signs of abating.
John Karras, PE, is a senior project manager at the national engineering firm, Simpson Gumpertz & Heger (SGH). Karras’ expertise encompasses building envelope design, consulting, and construction phase services. Karras is well experienced in roofing/waterproofing consulting and creatively collaborating with construction teams to navigate complex field challenges. He can be reached at jnkarras@sgh.com.
Thomas F. Chmill is a senior staff member at Simpson Gumpertz & Heger (SGH). He is experienced with the investigation and remediation of existing low-sloped roofs including the design of repairs and construction oversight for a variety of owners, architects, and general contractors (GCs). He can be reached via e-mail at tfchmill@sgh.com.