
by Chuck Knickerbocker
Curtain wall and window framing establishes the total possible area of unobstructed glazing, provides support for high-efficiency glass units, and can help improve thermal performance. With proper specification, it has the potential to help manage a building’s lighting, heating, and cooling energy consumption. However, there is a fine line between good daylighting and increased energy consumption.
A curtain wall with poor thermal and solar heat gain performance in an open, loft-style office building can be problematic. As interior temperatures rise in the afternoon sun, occupants close the window shades and turn on the air-conditioning, increasing HVAC systems loads. The energy consumed to cool the room offsets the lighting loads saved from the curtain wall’s natural light stream.
To avoid this heat exchange dilemma, much of the specification process focuses on the glazing material itself. Glass comprises a large portion of the curtain wall and window area. Bolstering its performance can help prevent adverse side effects like glare, heat loss, and undesired solar heat gain.
Less talked about—though equally important—is framing’s role in energy-efficient daylighting design. Framing anchors the glazing to surrounding building materials and establishes the foundation for numerous performance and design outcomes. With proper specification, it can help create a sound building envelope and support large, high-performance glazing.
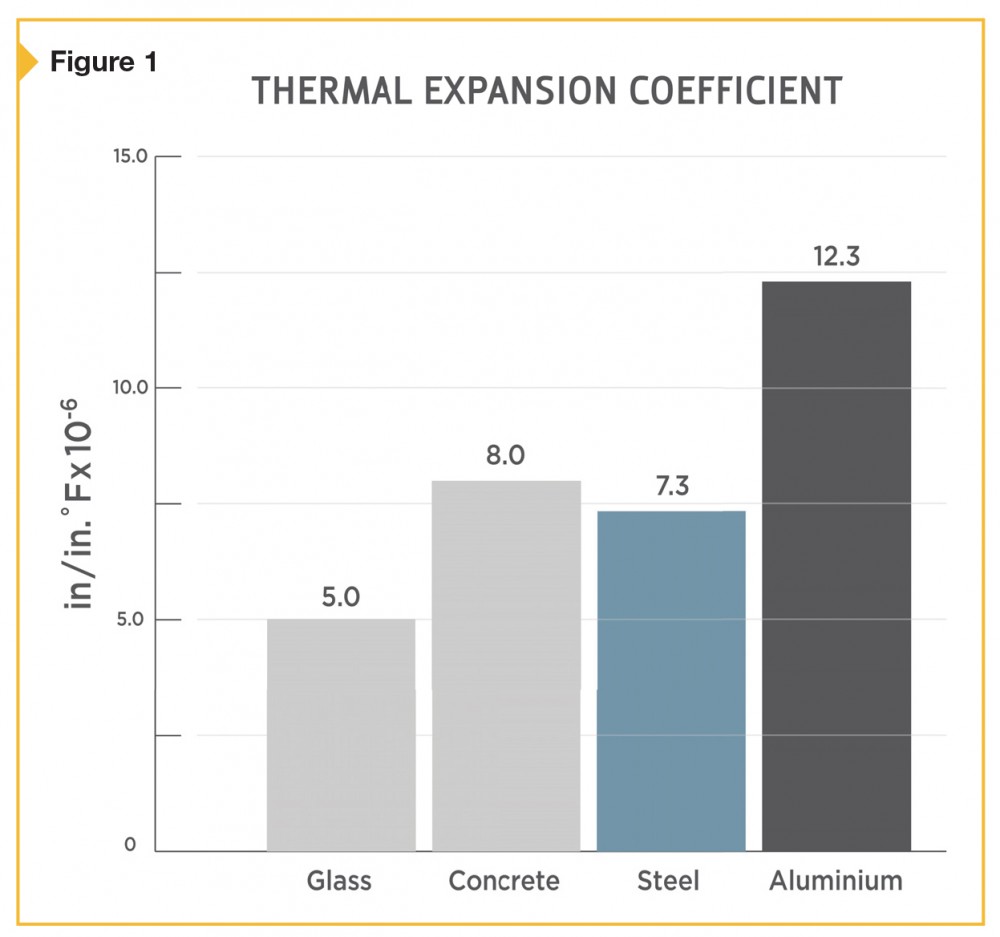
Thermal performance
As the connection point between the glazing and the perimeter details, curtain wall and window framing can help combat heat transfer.
Thermal conductivity
Many framing materials and systems have high thermal conductivity compared to other elements of the building envelope, creating assemblies susceptible to summer heat gain and winter heat loss. To overcome this challenge, design professionals often pair framing systems with low-emissivity (low-e) glass or other energy-efficient glazing. While center-of-glass (COG) thermal performance values improve, the system’s overall thermal efficiency remains substantially less effective where the captured or retained glass edge meets the supporting frames.
Incorporating glass with warm-edge spacers and frames with thermal breaks can help address this problem. Containing few, if any, metal components, warm-edge insulating spacers further improve the glazing’s U-value and reduce heat transfer. The spacers also help keep the inside surface of the frames warm to reduce condensation.
Thermal breaks help reduce heat flow by separating the inner and outer frame with low conductivity materials, such as polyester-reinforced nylon. According to the Whole Building Envelope Design Guide,1 a separator is classified as a ‘thermal break’ if it is greater than 6 mm (1/4 in.) thick. Generally, wide thermal breaks outperform narrow ones.
While breaks and separators can improve thermal performance, another important consideration is the conductivity of framing materials. While aluminum has a high thermal conductivity (i.e. approximately 124,500 joule [118 Btus] per hour), it has long remained the standard for commercial fenestration systems because of its lightweight nature. Today, advanced steel frames have emerged as a new, high-performance alternative (see “Steel Framing in the 21st Century“).
Steel’s thermal conductivity is approximately 74 percent less than aluminum (i.e. approximately 32,700 joule [31 Btus] per hour), and is equivalent to that of thermally broken aluminum frames. Due to the design of steel profiles, some advanced steel frames do not necessitate a traditional thermal break. Steel frames without a thermal break require less metal to support the glazing than traditional aluminum frames; therefore, they reduce the pathway for heat transfer.
Thermal expansion
Selecting curtain wall and window framing materials with similar expansion and contraction rates can help ensure a sound building envelope as the temperature changes. This is a crucial specification consideration for buildings in climates with extreme morning-to-midday temperature and seasonal changes.
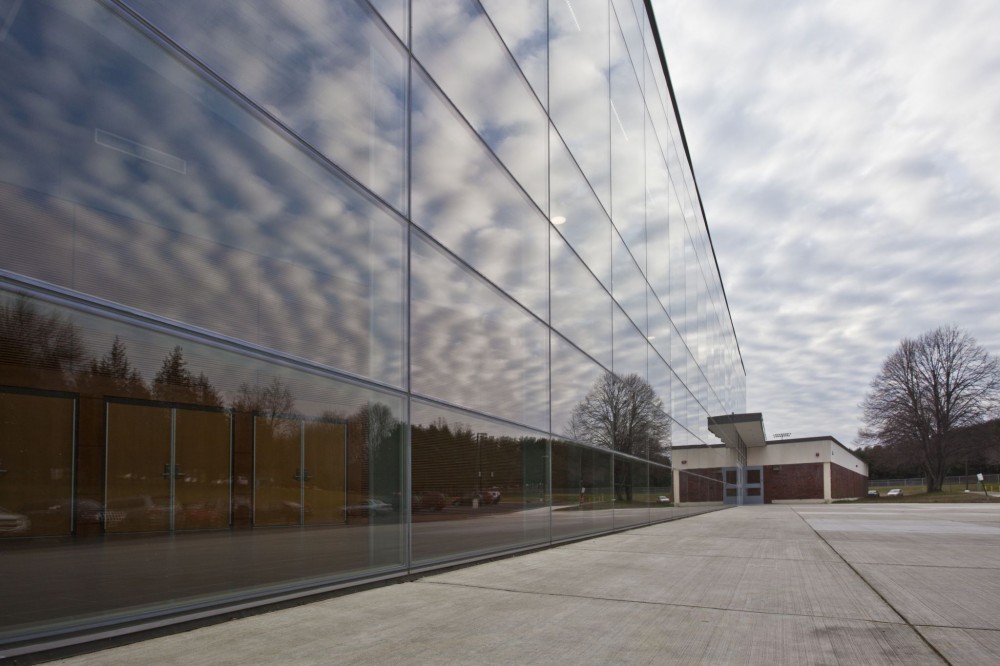
Between the two main types of curtain wall framing materials—steel and aluminum—the former’s thermal expansion coefficient of about 12 x 10-6 x 1/K is the most comparable to glass and concrete (which are approximately 9 and 10, respectively). Aluminum has a thermal expansion coefficient of about 24. It expands and contracts at a rate about 100 percent greater than steel (Figure 1). This difference can reduce the size of perimeter sealant joints, especially at locations where the expansion is being addressed.
Condensation resistance factor
Another important specification consideration is the condensation resistance factor (CRF), which is a ratio of the surface to ambient temperature difference. Curtain walls and windows with a CRF appropriate for the local climate and building design typically have less interior condensation (or ‘sweating’) on frames.
While the American Architectural Manufacturers Association (AAMA) and other associations provide guidelines for selecting systems with the appropriate CRF, it is important to note the condensation resistance factor is a weighted average. Since it does not take into account cold spots and other peripheral factors, thermal modeling software can prove valuable for projects where condensation control is a concern, including cold-climate, high-humidity applications. These programs factor in numerous variables, including proximity to perimeter heating elements, to help estimate the air temperatures along the inside surfaces of the glass and frames.
In general, thermally broken, thermally improved, and narrow steel frames can help reduce interior condensation by providing a smaller pathway for heat transfer.
Allowable free spans
When factors such as glare and heat gain/loss are adequately addressed, curtain walls and windows with large free spans can provide occupants with increased access to natural light. In turn, this can help reduce electricity consumption for interior lighting.
Aluminum framing can support many of today’s curtain wall free span load demands. Modern steel curtain walls are a suitable alternative for applications requiring greater areas of unobstructed glazing. This performance benefit is the result of steel’s strength. Steel has a Young’s modulus (E) of about 207 million kPa (30 million psi), compared to 69 million kPa (10 million psi) for aluminum. As such, it enables greater free spans than an aluminum system of similar dimensions and applied loads (Figure 2).
For example, given a 1.5-m (5-ft) mullion spacing at a 146-kg-force/m2 (30-lb/sf) wind load, an aluminum mullion of 64 x 191 mm (2 ½ x 7 ½ in.), including the glass and exterior cap, can span a total of 3.8 m (12 ½ ft). Using the same example, if that aluminum mullion was steel, sized at 60 x 192.5 mm (2 2/5 x 7 3/5 in.), it would only deflect one-third as much under the same conditions. In application, the steel mullion’s length can be increased to span almost 5 m (16 1/3 ft)—a 30 percent increase over its aluminum counterpart.
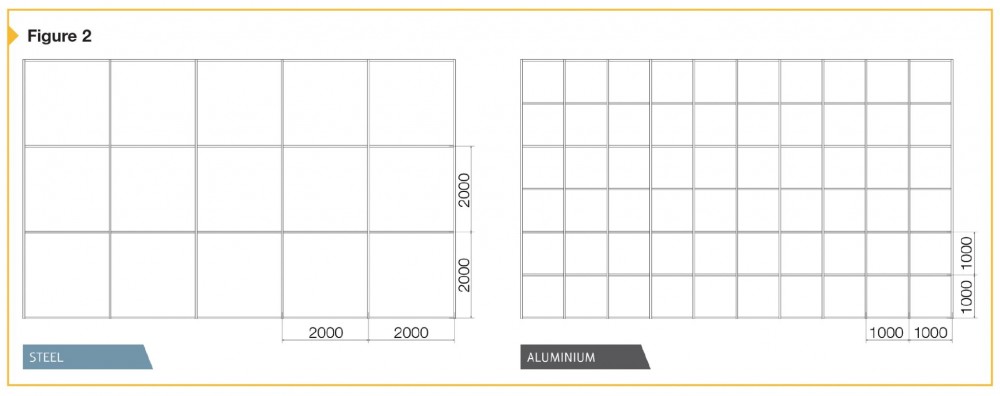
A second benefit of steel’s strength is the ability to meet curtain wall load and deflection requirements with less material. For example, in a typical two-story curtain wall, unreinforced steel frames can be 44 mm (1 ¾ in.) wide and 146 mm (5 ¾ in.) deep, versus 65 mm (2 ½ in.) wide and 203 mm (8 in.) deep for aluminum. This reduces frame dimension size by approximately 25 percent, and allows for a slight increase in the glazed area.
Support for high-efficiency glass units
Curtain walls incorporating high-performance double- or triple-glazed units can help balance the natural admission of light with energy costs. Due to the size and weight of such glazing, traditional framing may not be able to support the required loads, forcing design teams to reduce the glass lite size and modify free span distances, thus incorporating more framing, not less.
As an inherently strong material, steel can provide the necessary support for heavy triple- or quadruple-glazed units. Depending on product selection, some steel systems can support glazing infills up to 76 mm (3 in.) thick and weights up to 112.3 kg/m2 (23 lb/sf). This far surpasses the typical thickness (i.e. 45 mm [1 ¾ in.]) and weight (i.e. 48.8 kg/m2 10 lb/sf) of triple-glazed units. As a result, steel framing can support high-performance glazing to help offset solar heat gain in large glazed assemblies with marginal effects on the design intent.
A balancing act
While steel curtain wall and window systems can support high-efficiency glass units, it is crucial they account for changing sun angles and solar heat gain. Incorporating shading devices—such as sunshades and sunscreens—can help protect against direct sun penetration. This is important since even strategically positioned curtain wall assemblies are subject to direct sunlight during certain hours of the day.
While selecting the appropriate framing can help optimize a curtain wall or window’s energy performance, it is just one component of a multi-dimensional system. Building layout, site orientation, construction materials, and lighting systems all affect how well a fenestration system transmits light without undesirable side effects.
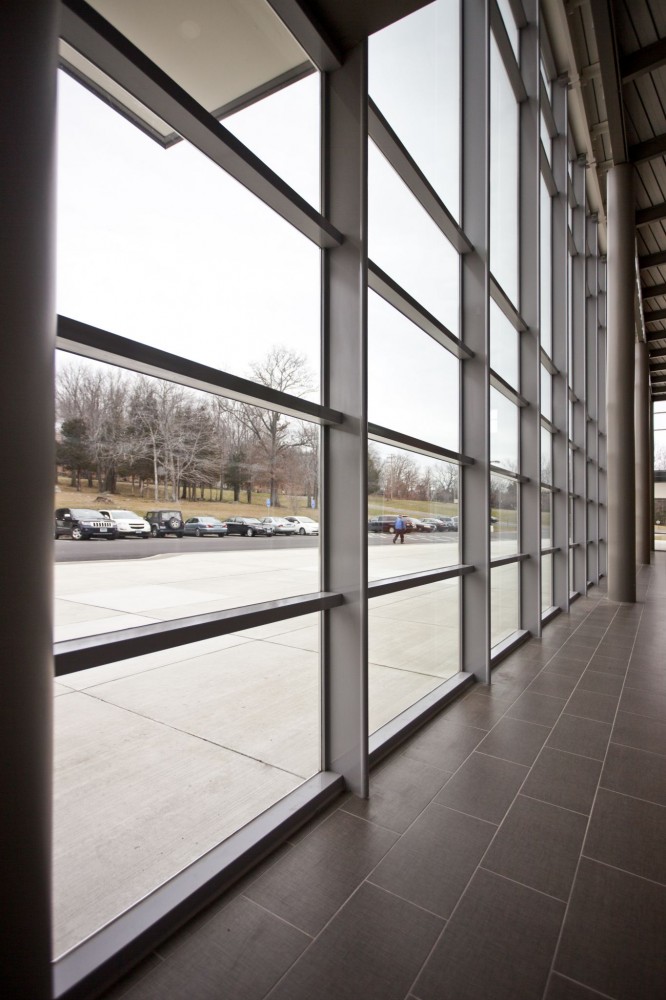
From supplemental devices to glazing options, methods for mitigating heat loss and undesired solar gain include:
- daylight-optimized footprint;
- high-performance glazing coatings;
- triple-glazing;
- photochromic and electrochromic (EC) glazing;
- double-skinned façades;
- daylight-redirection devices;
- solar-shading systems;
- daylight-responsive electric lighting controls; and
- daylight-optimized interior design.
As technology advances, design professionals will increasingly use high-performance curtain walls and windows to do more than create an energy-efficient building envelope. Building-integrated photovoltaic (BIPV) panels, for instance, can harvest daylight and help generate electricity. Manufacturers and suppliers of these specialized products can provide the necessary resources and support during the design and specification process.
Conclusion
With the push towards net zero energy, and with associations such as the American Society of Heating, Refrigerating, and Air-conditioning Engineers (ASHRAE) calling into question the effectiveness of large glazed areas, the benefits of pursuing more efficient fenestration systems extend beyond energy savings (see “The Window-to-wall Ratio Dilemma”). They help ensure future buildings will have large windows and curtain walls, be filled with warm, natural light, and provide occupants with views of cityscapes and nature.
Notes
1 See Nik Vigener, PE; and Mark A. Brown’s “Curtain Walls,” by visiting www.wbdg.org/design/env_fenestration_cw.php. (back to top)
Chuck Knickerbocker is the curtain wall manager for Technical Glass Products (TGP), a supplier of fire-rated glass and framing systems, along with specialty architectural glazing products. With more than 30 years of curtain wall experience, he has successfully worked with numerous architects, building owners, and subcontractors from development of schematic design through installation. Knickerbocker chairs the Glass Association of North America (GANA) Building Envelope Contractors (BEC) Division Technical Committee. He can be contacted via e-mail at chuckk@tgpamerica.com.