Product selection factors
When deciding which waterproofing product to select, it is important to consider the following job-specific factors.
Water table height
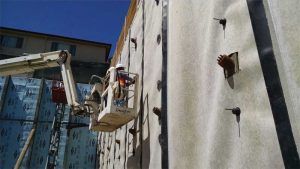
If the jobsite has a high water table, the lower part of the waterproofing membrane will have immediate contact with water. An asphaltic spray-applied product may erode with long-term exposure, so the project will require a different chemistry in a sheet-applied membrane for the entire height of the structural walls, or a sheet-applied membrane toward the bottom and an asphaltic product on higher levels where the risk of degradation is minimal.
Hydrostatic pressure
Some areas have greater hydrostatic pressure than others. Most spray-applied membranes are unable to handle these forces. In these instances, an alternative technology should be considered. It is best to confirm with the manufacturer the selected membrane can handle the anticipated hydrostatic pressure.
Construction method
Whether the project is utilizing a cast-in-place or shotcrete method will dictate which technology can be used in blindside waterproofing. If insulated concrete forms (ICFs) are used for the foundation and above-grade walls, a peel-and-stick membrane is recommended to avoid penetrating the insulation with a mechanically fastened product.
Soil characteristics
EPDM should be avoided when soil has high-methane content. Instead, it is recommended to use a more robust solution such as an asphaltic-based, bentonite, or HDPE product for greater density to prevent the methane gas from entering the building.
The presence of hydrocarbons in the soil can also impact product choice. If there is high hydrocarbon content, EPDM and some spray-applied products must be avoided. The manufacturer may recommend a different technology or a greater mil thickness of the spray-applied product.
Saltwater in the soil, present predominantly near coastal regions, can impact bentonite membranes as it will not expand as anticipated with fresh water. Talk to the manufacturer about alternate saltwater-specific products for this condition.
Temperature restrictions
If the jobsite faces extreme high or low temperatures, check for application limitations of the below-grade waterproofing products. Sheet-applied membranes are often recommended as they offer design flexibility and do not have temperature restrictions.
Code requirements and regulations
There are varying code requirements across the United States. Some regions will necessitate a protection course over the waterproofing membrane for redundancy. Review codes with the design/build team to ensure compliance.
In many urban areas, flooding is a major concern, so bioretention requirements are emerging to control and limit water runoff. Here, commercial projects may need to redirect drainage or install underground water retention tanks to collect water and control the exit flow into the city sewage.
Ease of installation
Every technology has its pros and cons and their ease-of-installation can be a large contributing factor. Bentonite sheets, for example, are heavy and require more manpower to move the rolls, while EPDM and other rubber sheet membranes are less dense and, therefore, lighter to work with. Spray-applied products need specialized equipment, but tend to be easier to install to fill voids and complex geometries.
General weather
The construction team should review upcoming weather conditions before installing a waterproofing membrane. After a period of rain or snow, some waterproofing materials can be applied to damp concrete, which can speed up construction. Others may need to wait until the substrate is completely dry, resulting in project delays. During high winds, bentonite sheet membranes can be difficult to work with and will prematurely expand with exposure to any precipitation, if unprotected. If bentonite is hydrated before the concrete is poured, the sheets will need to be removed and replaced.
Testing
Before selecting a technology or material, it is advisable to check adherence to ASTM testing standards to ensure it fits project requirements. Some important performance characteristics related to physical properties include:
- hydrostatic head resistance, per ASTM D5385, Standard Test Method for Hydrostatic Pressure Resistance of Waterproofing Membranes;
- low temperature flexibility, per ASTM D1970, Standard Specification for Self-adhering Polymer Modified Bituminous Sheet Materials Used as Steep Roofing Underlayment for Ice Dam Protection;
- peel strength of adhesion bond, according to ASTM D903, Standard Test Method for Peel or Stripping Strength of Adhesive Bonds;
- elongation/strength at break, per ASTM D412, Standard Test Methods for Vulcanized Rubber and Thermoplastic Elastomers—Tension;
- puncture resistance, per ASTM D4833, Standard Test Method for Index Puncture Resistance of Geomembranes and Related Products;
- permeance, according to ASTM E96, Standard Test Methods for Water Vapor Transmission of Materials; and
- resistance to microorganisms, per ASTM D4068, Standard Specification for Chlorinated Polyethylene (CPE) Sheeting for Concealed Water-containment Membrane.