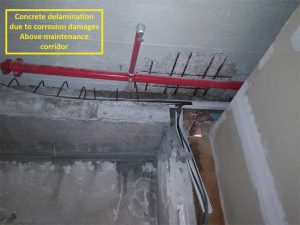
Impact of local climates and chlorides on concrete
Service life prediction modeling software can offer a snapshot of how various climates and chloride levels can affect concrete structures differently. Inputting the same hypothetical concrete mix into the program yields a variety of different results based on expected risk factors and surface chloride concentration for each location. For example, in one modeling session, a parking garage in either Minneapolis or San Diego was expected to reach its maximum surface chloride concentration in 13.3 years at either location. However, corrosion initiation was predicted after 10.8 years in Minneapolis (in the middle of the continent) and more than two years earlier in San Diego, an overall warmer climate near the coast.
Modeling for marine spray zones showed even more extremes. In these locations, the software assumes surfaces will reach maximum surface chloride content (one percent) sooner than in other environments. For a hypothetical marine spray zone structure in Boston, Massachusetts, corrosion initiation was predicted in 8.1 years, while heading south to the warmer subtropical climate of West Palm Beach, Florida, brought a prediction of corrosion initiation in only 5.5 years (see Figure 1).
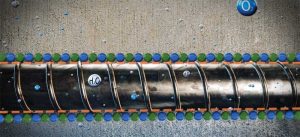
Strategies to counter corrosion
There are many approaches to countering corrosion and extending the service life of concrete structures in corrosive water environments. These include the concrete mix design, the type of reinforcement used, corrosion inhibitors, and the thickness of the concrete cover.
According to Penn State College of Engineering, extremely low water-cement ratios result in dense concrete, making it more difficult for chlorides to penetrate.7 However, this type of concrete enhances thermal cracking which lessens the actual concrete cover. Penn State also notes denser concrete can be more difficult to work with, and requires water-reducing admixtures. Adding more pozzolans such as silica fume and fly ash is another way to reduce permeability. Epoxy coated rebar offers protection from water and oxygen by means of a physical barrier but can experience accelerated corrosion where coating imperfections, such as cracks and holes, are present.
Corrosion inhibiting admixtures, often calcium-nitrite (CNI) based, are another option. CNI reacts with free iron ions to form a protective oxide layer on the rebar and raise the chloride threshold; but they must be dosed based on expected chloride loading, requiring increasingly higher dosage rates that can be ineffective if predictions are wrong. Theoretically, a thicker concrete cover will also delay time to corrosion, but additional concrete can be prohibitively expensive and does not solve the problem of corrosion once cracks allow an access point to the rebar embedded within the concrete.