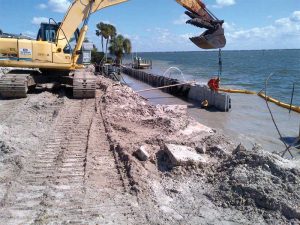
Use of MCIs in seawalls
A recently built seawall in Longboat Key, Florida, also had to face the severe challenge of direct contact with seawater in a warm subtropical climate where corrosion quickly accelerates. Modeling software predictions for a standard seawall concrete mix forecasted a service life of only 15.2 years before the first repair would be needed. Adding an MCI admixture to the design tripled the projected service life to 46.9 years before repair.
However, the owner had an even stronger vision in mind to construct the wall with a 100-year service life (time before first repair) so it would last for future generations. The first mix design was replaced with a concrete mix used by the Florida Department of Transportation (FDOT), which brought the service life prediction beyond the required 100 years. The addition of MCI extended the prediction even farther to more than 150 years.
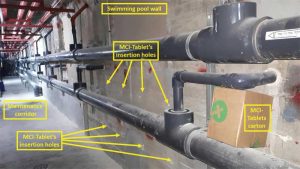
One port wall in Tel Aviv, Israel, is a perfect example of what can happen to normal seawalls with constant exposure to seawater and marine conditions. The wall has already reached the end of its service life and is set for repair later in 2021. It is showing signs of deterioration with an exposed network of rusted reinforcement in some places clearly revealing an underlying problem. Due to the corrosiveness of the environment, a corrosion consultant has been involved in the project, and both a topical MCI and an MCI admixture have been specified for use in the 150-m² (1615-sf) repair. MCI chemistry will be a critical factor in delaying and reducing corrosion, so the next repair does not have to happen so soon.
“The considerations in projects like these usually focus on longevity with minimal maintenance, since shutting down for repairs is extremely difficult,” said Halperin, whose firm was called on to supply MCI technology for the damaged wall.
Addressing root causes of swimming pool damage with MCI
The potential benefits of MCI chemistry are now being sought after in the case of the Wingate pool deterioration although previous repairs may have overlooked long-term corrosion mitigation. The consultant involved in the 2016-2020 repair took a different tack by incorporating MCI technology into the repair mortar to enhance its durability. Further, MCI was inserted in tablet form inside the walls of the pool and beyond the rebar depth to leave an ongoing source of MCI diffusing throughout the concrete pores and protecting adjacent reinforcement from future corrosion. By going beyond the surface issues of temporary patching, this repair is much more forward-looking with the intent to slow corrosion and delay time to the next repair. As a tribute to the practicality of this approach, the project was completed during 2019-2020 without having to close the pool.
Conclusion
MCI technology is an important option for concrete structural designers to consider. MCI has shown itself to be a viable tool to reduce corrosion and extend service life. Its benefits in terms of practicality, cost-effectiveness, ease of use, and service life potential make it worthy of further investigation by any engineer, contractor, builder, or construction professional seeking time-tested, innovative ways to enhance concrete longevity in corrosive water handling environments.