Are all zinc coatings created equal?
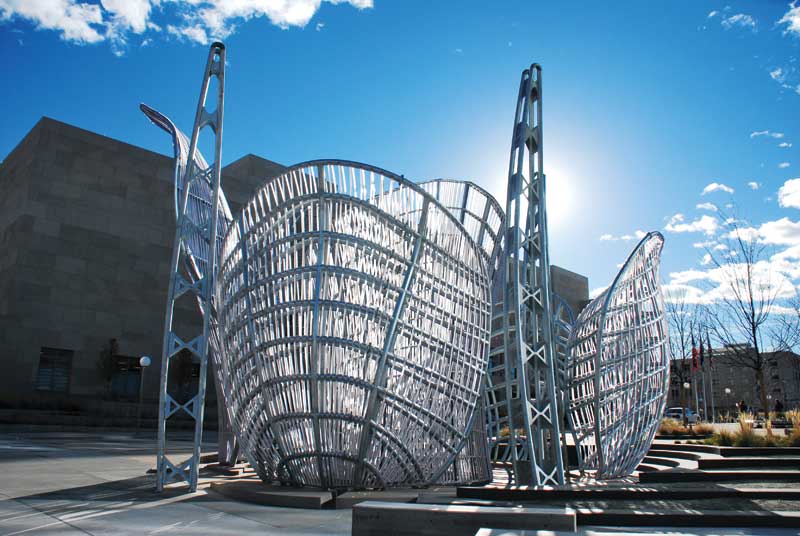
by Melissa Lindsley
Zinc is naturally found in elements such as air, water, and soil as well as in plants, animals, and humans. It is the 27th most abundant element in the Earth’s crust and is infinitely recyclable without the loss of its properties, making it a true renewable resource.
Zinc’s ability to protect iron and steel products from corrosion has been known for centuries as the material has been used in construction since the second century. More than 13 million tons of zinc is produced annually worldwide—70 percent of which is from mined ores and the remaining is from recycled sources. More than half of this annual production is used in zinc coatings to protect steel from corrosion.
Today, there are many types of zinc coatings, often referred to generically as ‘galvanizing.’ The most common used in construction applications are:
- batch hot-dip galvanizing;
- continuous sheet galvanizing;
- zinc-rich painting;
- zinc spray metallizing;
- mechanical plating;
- electrogalvanizing; and
- zinc plating.
All these coatings have unique characteristics, corrosion resistance, and performance—in other words, not all zinc coatings are created equal. This article will help architects, engineers, and other specifiers understand the differences between the zinc coatings, and therefore select the most suitable one for their project.
How zinc protects steel from corrosion
All zinc coatings provide basic barrier protection by isolating the steel from exposure to the environment. However, there are two additional protective benefits when using zinc to protect steel from corrosion: cathodic (sacrificial) protection and the zinc patina. Whenever two dissimilar metals are in contact, one metal (anode) will preferentially corrode while the other (cathode) is protected. Zinc coatings exploit this phenomenon by using zinc to protect steel.
The “Galvanic Series of Metals,” which lists metals in order of their electrochemical potential in the presence of salt water, defines which will be anodic when two metals are connected. Metals higher on the list will become anodic to those lower in the series. Zinc is higher than steel on the scale, and therefore, zinc will sacrificially corrode to protect the underlying steel.
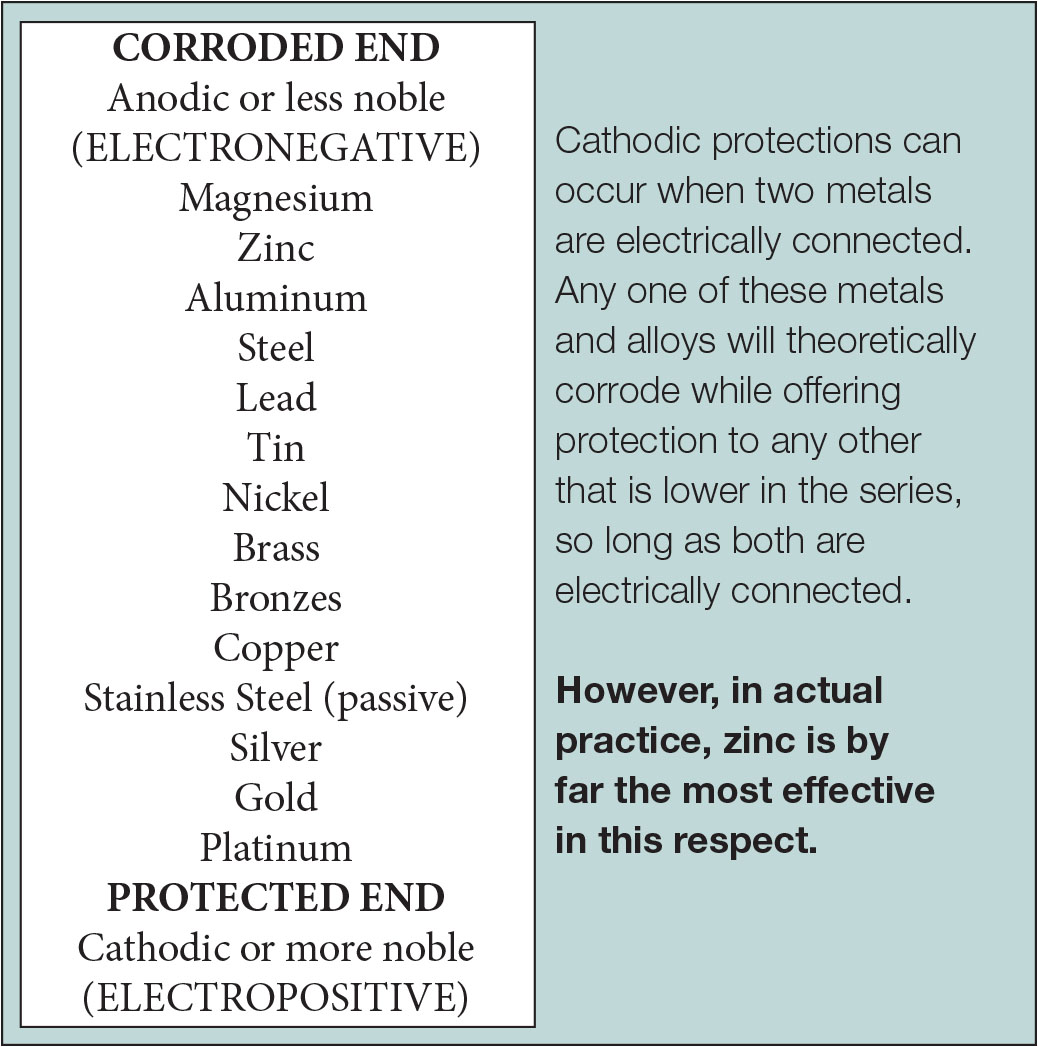
In addition to the natural barrier and cathodic protection, zinc also develops a protective patina when exposed to the atmosphere. Zinc, like all metals, corrodes when exposed to the air. Over time, it forms dense, adherent corrosion by-products as it is exposed to the natural wet and dry cycles of the atmosphere. These by-products, collectively known as the zinc patina, create a tightly adherent, insoluble protective layer on the surface of the zinc coating, lowering the overall corrosion rate. When the zinc patina is fully developed, the zinc will corrode 10 to 100 times slower than the rate of ferrous materials in the same environment.
There are seven zinc coatings commonly used in construction. Four of these—continuous sheet galvanizing, mechanical plating, electrogalvanizing, and zinc plating—can only be used on small parts such as fasteners, or sheet, strip, and wire. The other three—batch hot-dip galvanizing, metallizing, and zinc-rich paints—have much broader applications, but are predominantly used in structural steel applications.
Batch hot-dip galvanizing
Batch hot-dip galvanizing, also commonly called general galvanizing or just hot-dip galvanizing, produces a zinc coating by completely immersing the iron or steel product in a bath (kettle) of molten zinc. Prior to being dipped in the bath, the steel is chemically cleaned to remove organic contaminants, mill scale, and oxides. The final cleaning step also leaves a protective layer of zinc chloride on the surface to prevent oxidation before immersion in the kettle. This layer will evaporate from the surface when the steel hits the top of the bath, which consists of at least 98 percent pure zinc heated to approximately 443 C (830 F).
While the steel is in the galvanizing kettle, the zinc metallurgically reacts with the iron to form the hot-dip galvanized coating. This coating consists of a series of zinc-iron alloy layers and a surface layer of pure zinc. These intermetallic layers are tightly bonded (24,281 kPa [3600 psi]) to the steel, becoming an integral part of it rather than just a surface coating. The zinc-iron alloy layers are also harder than the base material, providing excellent abrasion resistance.