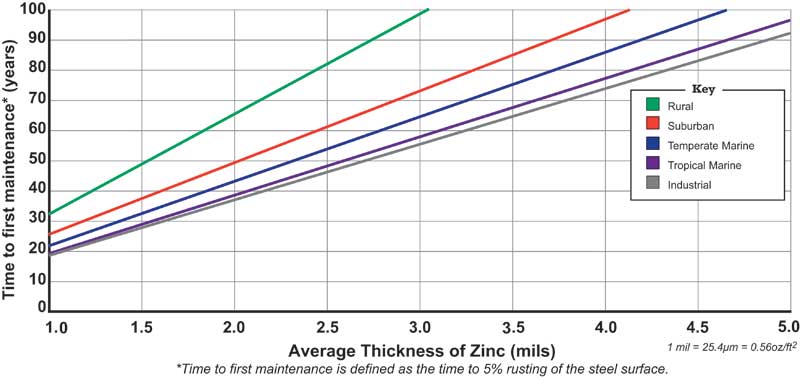
Another unique characteristic of batch hot-dip galvanized coatings is its uniform, complete coverage. During the diffusion reaction in the kettle, the intermetallic layers grow perpendicular to all surfaces, ensuring edges, corners, and threads have coating thicknesses equal to or greater than flat surfaces. Additionally, because hot-dip galvanizing is a total immersion process, all interior surfaces of hollow structures and difficult to access recesses of complex pieces are also coated. While the steel articles are in the zinc bath, they float, move, and vibrate around to ensure areas where the steel is in contact with racks or wires are able to be coated. However, it is common to see cosmetic marks when the steel is withdrawn from the galvanizing kettle, but these can be touched up for aesthetic purposes.
The governing specifications for the hot-dip galvanized coating are:
- ASTM A123, Standard Specification for Zinc [Hot-dip Galvanized] Coatings on Iron and Steel Products;
- ASTM A153, Standard Specification for Zinc Coating [Hot-dip] on Iron and Steel Hardware; and
- ASTM A767, Standard Specification for Zinc-coated [Galvanized] Steel Bars for Concrete Reinforcement.
These standards contain minimum coating thickness requirements based on steel type and thickness. The hot-dip galvanized coating is thicker and/or denser than other zinc coatings. The Time to First Maintenance (TFM) chart shows the linear relationship between zinc coating thickness and maintenance-free service life in atmospheric exposure. For example, ASTM A123 requires structural steel that is 15 mm (5⁄8 in.) thick or greater to have a minimum coating thickness of 0.1 mm (3.9 mils). In an industrial environment, this would provide a TFM of 72 years.
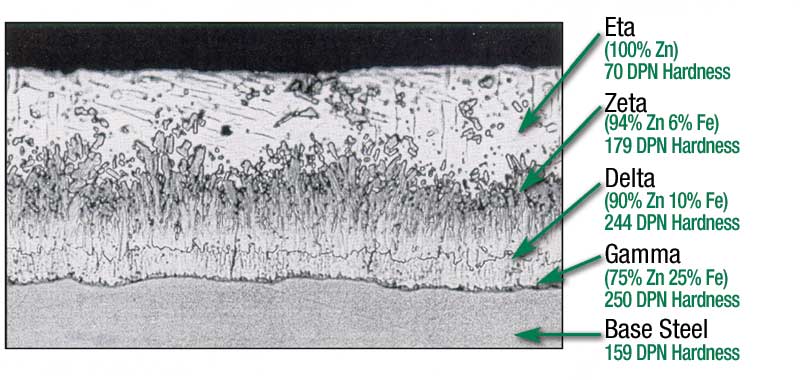
Hot-dip galvanizing is used in myriad applications, from electric utility to artistic sculptures, and on
a wide range of sizes from nuts, bolts, and nails to large structural beams and other shapes. Size can be a limitation for batch hot-dip galvanizing, but the average kettle length in North America is 12 m (40 ft), and 16 to 18-m (55 to 60-ft) kettles are common. Employing progressive dipping practices (immersing one portion of a product and then the other) increases the maximum size to nearly one and a half times the bath size. Batch hot-dip galvanizing is most common for protection of atmospherically exposed steel, but it is also frequently used in fresh and saltwater applications as well as embedded in soil and/or concrete.