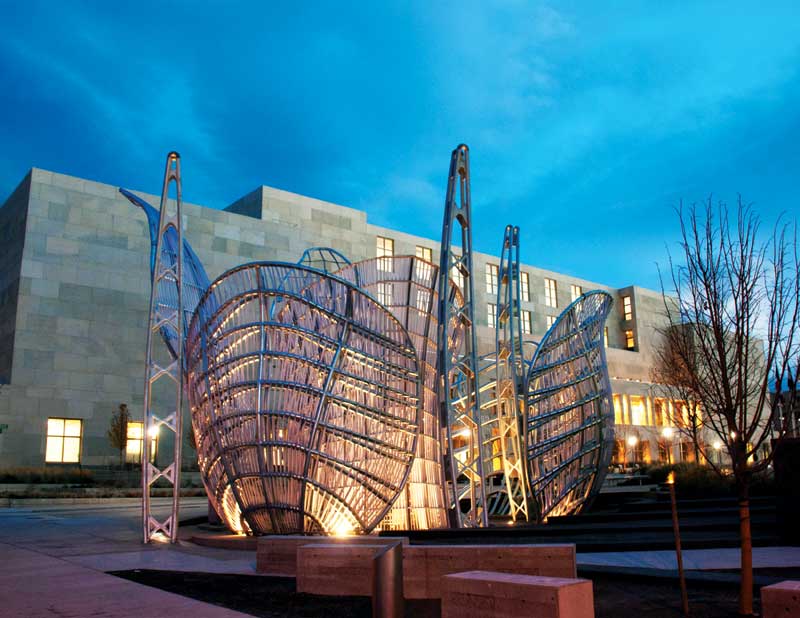
Photos courtesy AGA
There are a number of different sheet products produced in this process including:
- galvanized;
- galvannealed;
- two alloys of zinc and aluminum;
- two aluminum based alloys; and
- the terne coating.
Since the process is very similar to batch hot-dip galvanizing, the two coatings are often confused. The major difference is found in the zinc coating thickness. The continuous sheet process has greater control and precision of the zinc coating thickness, and the coating itself is mostly unalloyed zinc, though minimal alloy layers are present. Another key difference is the coating in this process is applied prior to fabrication, whereas batch hot-dip galvanizing is applied after.
Continuous sheet galvanizing is stocked in a variety of coating weights. One of the most common is Class G90 which has 274 g/m2 (0.9 oz/sf) of zinc (total both sides) or about 0.8 mils (20.6 µm) per side. Figure 1 lists available coating grades of continuous sheet galvanizing.
Continuous sheet galvanizing is most commonly used in car bodies, appliances, corrugated roofing, siding, and ductwork. The final coating is very smooth, allowing for it to be treated for painting. Most continuous sheet galvanizing is specified for indoor applications or where exposure to corrosive elements is mild. Some formulations including other alloys in addition to or besides zinc may be suited for other applications.
Electrogalvanizing
Electrogalvanized (electroplated) coatings are created by applying zinc to steel sheet and strip by electro-disposition. Similar to sheet galvanizing, the operation, often done in a steel mill, is continuous and the coating thickness is minimal. Prior to coating, the sheet or strip is fed through a series of washes and rinses, then into the plating bath. The coating develops as positively charged zinc ions in the solution are electrically reduced to zinc metal and deposited on the negatively charged cathode (sheet steel).
The coating is a highly ductile, thin layer of pure zinc, tightly adherent to the steel. The coating weight ranges from 61 to 152 g/m2 (0.2 to 0.5 oz/sf) for sheet products. The coating is thinner and smoother than the continuous sheet galvanized coating. The most common applications are in automobile and appliance bodies. The electrogalvanized coating can be treated with a wash primer, which leaves a passivation layer as well as cleans and etches the surface to make it suitable for painting.
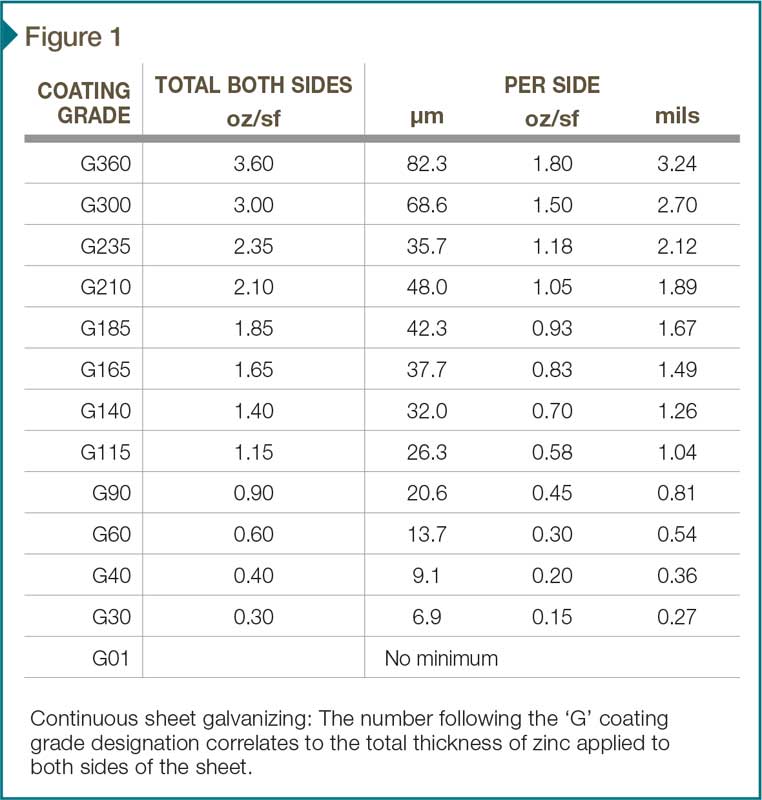