
Mechanical plating
Mechanical plating is accomplished by tumbling small parts in a drum with zinc, proprietary chemicals, and glass beads. The beads peen zinc powder on to the part, and the parts are then dried and packaged. Sometimes, the parts are then post-treated with a passivation film before being dried and packaged. Mechanical plating is limited to small iron and steel parts, typically no larger than 203 to 228 mm (8 to 9 in.) and weighing less than 0.45 kg (1 lb). Before placed in the plating barrel, the parts are cleaned and flash copper-coated.
The zinc coating thickness of mechanically plated parts ranges from 0.2 to 4.3 mils (5 to 109 µm), but the common thickness on commercial fasteners is 2 mils (50 µm). The thickness is regulated by the amount of zinc in the barrel and the duration of the tumbling time. The coating is mechanically bonded to the surface and the density is about 70 percent that of hot-dip galvanized coatings.
Mechanical plating is most commonly used on high-strength fasteners and other small parts unsuitable for hot-dip galvanizing. The coating application process will cause complex designs with recesses or blind holes to have inconsistent or non-existent coatings because the glass beads either cannot access the area to apply the zinc, or cannot peen with enough velocity to coat the surface consistently.
Zinc plating
Zinc plating is identical to electrogalvanizing in principle, as the coating is electro-deposited. However, zinc plating is used on small parts such as fasteners, crank handles, springs, and other hardware items rather than sheet metal. After alkaline or electrolytic cleaning and pickling to remove surface oxides, steel parts are loaded into a barrel, rack, or drum and immersed in the plating solution. Various brightening agents may be added to the solution to add luster.
The coating is a thin, pure layer of zinc with a maximum thickness of 25 µm (1 mil). The specification ASTM B633, Standard Specification for Electrodeposited Coatings of Zinc on Iron and Steel, lists four classes of zinc plating: Fe/Zn 5, Fe/Zn 8, Fe/Zn 12, and Fe/Zn 25, where the number indicates the coating thickness in micrometers (µm). Typically, zinc-plated coatings are dull gray with a matte finish, but whiter, more lustrous coatings can be produced depending on agents added to the plating bath or through post-treatments. Zinc plating is usually only used for interior or mildly corrosive conditions on fasteners, light switch plates, and other miscellaneous small parts.
Selection of zinc coatings
The architect, engineer, or specifier must evaluate the service environment, desired life, and initial lifecycle costs before determining the zinc coating best-suited for the project. Each zinc coating provides varying degrees of corrosion protection in a given exposure environment. The life of all zinc coatings is linear to the zinc coating thickness. However, zinc coating thickness cannot be evaluated without also considering the density, or zinc per unit volume. The zinc coating application process will dictate both the density and the thickness.
To compare the various zinc coatings, it is easier to convert all the coatings into an equal weight per unit area of zinc, which in theory would provide equal service lives. Figure 2 represents the coating thickness required by each zinc application method to equal 305 g/m2 (1 oz/sf) of zinc on the surface. So, according to the conversions, 1.7 mils (43 µm) of hot-dip galvanizing would give the same service life as 2.2 mils (43 µm) of mechanical plating, etc.
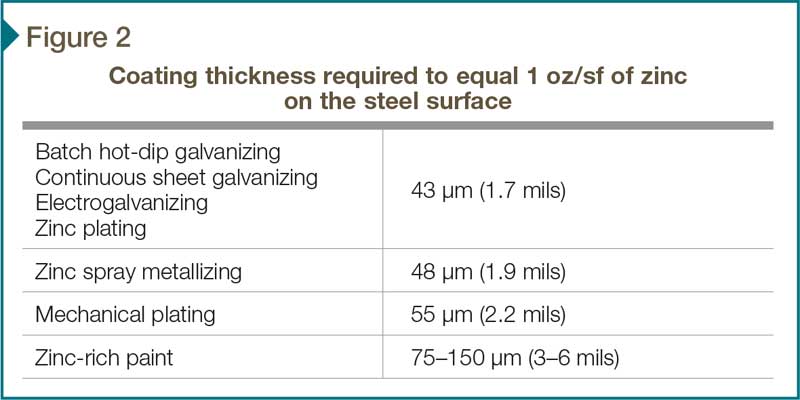
Conclusion
There are many ways zinc can be used to protect steel from corrosion. However, lumping all of these zinc coatings under the umbrella term ‘galvanizing’ is unfair, as each is very different in application, characteristics, and performance. Once a specifier evaluates the exposure condition of a project, he or she can select the zinc coating best-suited for that particular application, because not all zinc coatings are created equal.
Melissa Lindsley is the marketing director for the American Galvanizers Association (AGA), and educates architects, engineers, fabricators, owners, and other specifiers about the technical aspects and benefits of hot-dip galvanizing. Lindsley can be reached via e-mail at mlindsley@galvanizeit.org.