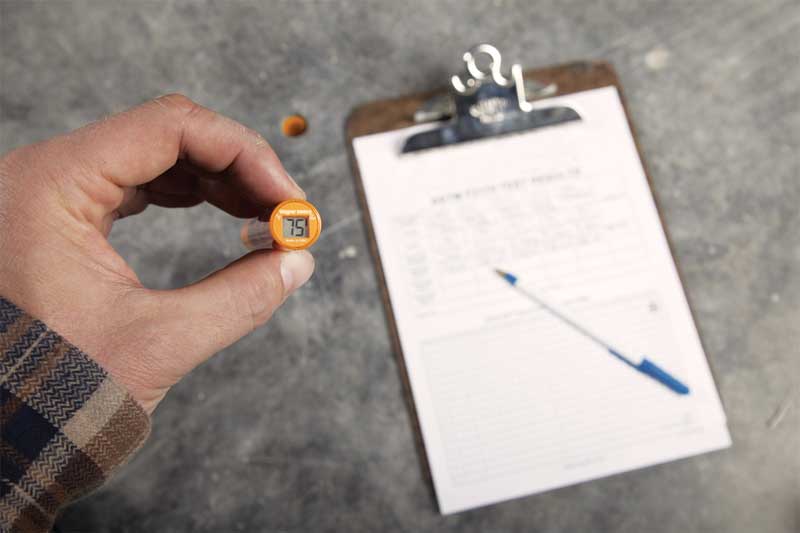
Specifying the concrete moisture test
All the planning related to concrete and drying times is intended to help control the future as much as possible. However, the project team’s choices, predictions, and estimations must still come face-to-face with reality. This is why it is fundamentally important to specify the most proven and reliable concrete moisture test to get an accurate assessment of actual conditions. Without the right moisture test, the project team cannot be confident regarding the true moisture condition of the concrete; design professionals simply cannot make good decisions about how and when to move forward.
Several methods of concrete moisture testing exist. The two most commonly used are:
- the moisture vapor emission rate (MVER), or calcium chloride test, using ASTM F1869, Standard Test Method for Measuring Moisture Vapor Emission Rate of Concrete Subfloor Using Anhydrous Calcium Chloride; and
- the aforementioned in-situ RH test method, using ASTM F2170, Standard Test Method for Determining Relative Humidity in Concrete Floor Slabs Using In-situ Probes.
Each of these tests is used to evaluate the moisture condition of the concrete, but they actually measure different things. This makes them quite distinct from one another.
The MVER test measures the moisture absorption rate of calcium chloride crystals that are placed on the surface of the concrete slab. In contrast, the RH test uses electronic sensors placed at a specific depth in the slab to measure RH within it. Studies at Lund University in Sweden and elsewhere have shown the RH percentage at 40 percent depth (for a slab drying from one side) predicts the slab’s moisture condition once it is sealed by a finished floor product. (In the 1940s, this was a qualitative test for concrete moisture. Two decades later, it evolved into a quantitative test, but with no documented scientific basis for going this direction. The MVER test is still employed today simply because it is what a number of people have customarily used. However, with the growing awareness of the test’s inherent problems and lack of a scientific pedigree, it has increasingly gone out of favor.) So, do these different approaches to testing for concrete moisture actually matter?
It is important to consider where each test is taking its measurements. Measuring moisture at the surface of the slab, as is done with the MVER methodology, can be unreliable for several reasons. The surface of the slab is disproportionately affected by ambient conditions. Measurements taken at the surface also ignore what is known about how concrete dries—that is, as the moisture moves up through the slab, a gradient forms in which moisture levels typically rise with increasing depth. Measuring surface moisture is essentially taking a superficial measurement that fails to account for conditions deeper in the slab.
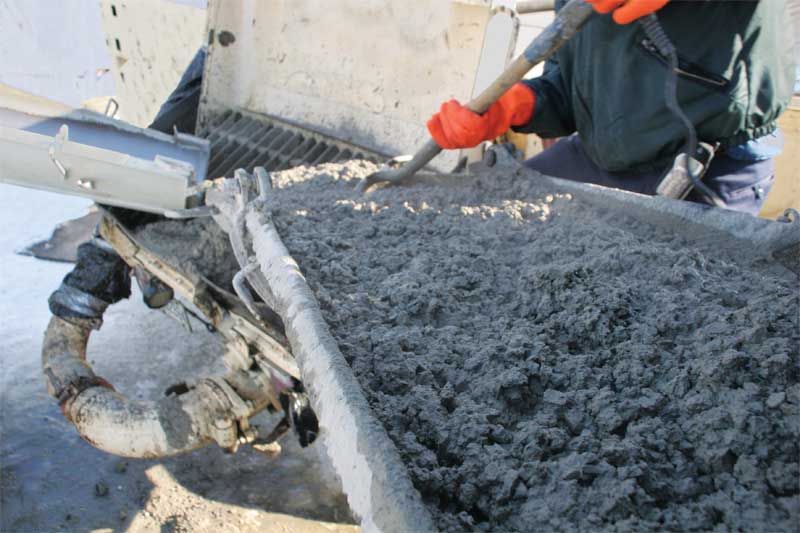
Photo © iStock. Photo courtesy Wagner Meters
The RH test, on the other hand, fully accounts for the moisture gradient by measuring at a specific, proven depth inside the slab. The location of the RH test—inside the slab and not at the surface—also minimizes the influence of ambient conditions.
Another critical difference is that the MVER test returns an estimated emission rate at a specific point in time. However, unlike the RH test, this emission rate has not been shown to be a reliable predictor of the overall moisture condition of the slab once it is sealed with a finished floor product. The RH test is actually measuring how much moisture the finished floor experiences once the slab is sealed. This is because it is taken at a proven depth for measuring the slab’s moisture ‘equilibrium point.’
The moisture gradient typically existing before the flooring installation tends to disappear and then move toward this equilibrium point after installation. Since the RH test can rightly be considered an accurate predictor of the slab’s moisture equilibrium point, it has increasingly become the assessment tool of choice for indicating when a slab is sufficiently dry.
Typically, project specifications include the manufacturer’s requirements regarding acceptable moisture condition of the slab for each finished floor product to be employed. Although this is valuable information, merely inserting the manufacturer’s specs does not commit the general contractor or anyone else to a particular method for knowing when the concrete is within the acceptable moisture range.
It is not sufficient to specify the goal (i.e. the acceptable moisture condition of the concrete); one must also specify how it will be known when that point is reached. Failing to specify the in-situ RH test in the documentation leaves the project open to using faulty or misleading methods of testing for concrete moisture.