Assessing aluminum’s LCA
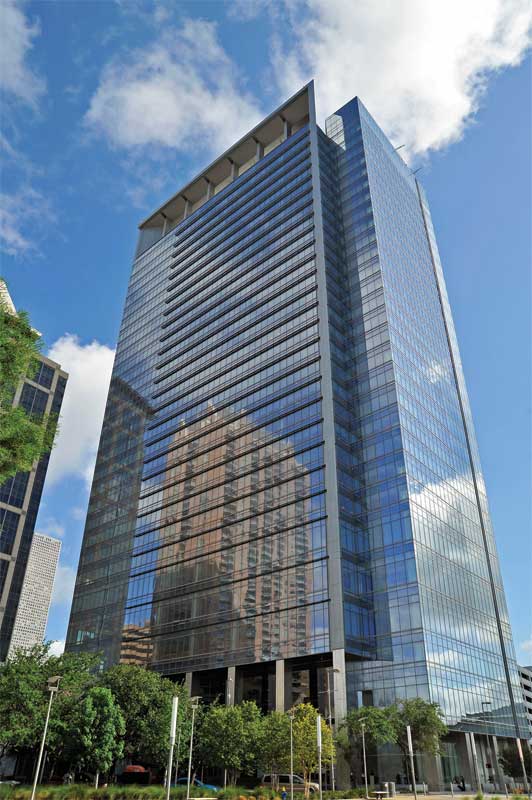
In-depth example: Aluminum building components and LCA
From curtain walls and façade cladding panels to commercial windows, sunscreens, and louvers, aluminum exterior building systems and components are widely used.
For glazed systems, common impact categories will include:
- resource use—renewable and nonrenewable material resources, freshwater consumption, and primary energy demand (i.e. inputs requiring renewable and fossil energy sources);
- global warming potential (GWP)—outputs leading to global warming (expressed as carbon dioxide [CO2] equivalents in kilograms);
- acidification potential—outputs leading to acid rain/forest decline (expressed as sulfur dioxide equivalents in kilograms);
- eutrophication potential— outputs leading to overfertilization of the soil or water (expressed as nitrogen equivalents in kilograms);
- smog formation potential—outputs with potential photochemical ozone creation (expressed as ozone equivalents in kilograms);
- ozone depletion potential—outputs leading to thinning of the ozone layer in the upper atmosphere (expressed as trichlorofluoromethane equivalents in kilograms); and
- waste—hazardous and nonhazardous waste disposed and materials for recycling.
Aluminum and resource use
Aluminum is the most commonly recycled postconsumer metal in the world. Recent decades have seen a notable increase in the material’s secondary production (the process of recycling aluminum scrap so it can be used again). According to the Aluminum Association, “Nearly 40 percent of the North American aluminum supply is now created through secondary production, up around 10 percent since the early 1990s.” (This information was derived from www.aluminum.org/industries/production/secondary-production.) In fact, approximately 65 percent of all the aluminum ever produced is still in use.
Recycled aluminum consumes only about five percent of the energy required to produce primary aluminum, leading to fewer greenhouse gas (GHG) emissions. Using postconsumer metal as opposed to raw materials also greatly reduces the environmental toll (and economic costs) associated with long-distance transport.
Even for extracted aluminum, numerous U.S. primary aluminum producers have participated in the Environmental Protection Agency’s (EPA’s) Voluntary Aluminum Industrial Partnership (VAIP) program to both measure and reduce perfluorocarbon (PFC) generation. (PFC traps heat in the atmosphere, contributing to the greenhouse effect.) U.S. emissions of perfluorocarbon (PFC) from aluminum smelting have been reduced by more than 50 percent from 1990 levels, according to the American Architectural Manufacturers Association (AAMA). (For more, visit www.aamanet.org/pages/environmental.)
Environmental impacts associated with the finishing and pretreatment of aluminum require particular consideration. Anodizing, for example, involves an electrochemical process that increases the thickness of the naturally occurring, protective oxide layer. This finishing option has some benefits—it is cost-effective, results in a very hard, mar- and scratch-resistant surface, and has a popular metallic look. However, it is also water-intensive, using millions of gallons a year. Additionally, it requires the use of corrosive acids and chemicals, along with extremely high electricity consumption (which is typically generated using carbon fuels).
Buildings employing architectural coatings avoid the problems associated with anodizing. The chromates used in coating pretreatment have historically had environmental costs, as they may contain hazardous materials. However, those costs may be mitigated by the adoption of trivalent chromium or chromium-free pretreatment methods. To eliminate the use of chromium in the pretreatment process, conversion coatings have been developed that use ‘dry-in-place,’ nonreactive coatings applied in a thin film on the metal.
This only refers to the pretreatment process, and has nothing to do with the paint chemistry—whether liquid, powder, acrylic, or polyvinylidene fluoride (PVDF). Coatings currently sold in this market have been tested and perform well over this pretreatment process. There are no significant advantages to dry versus wet coatings, as both have their environmental benefits. For example, one advantage of powder is it has no volatile organic compounds (VOCs) at application. With wet paint, on the other hand, the solvent is destroyed, and the heat generated from this process fuels the curing oven, so much less natural gas is needed to cure wet paint than powder.