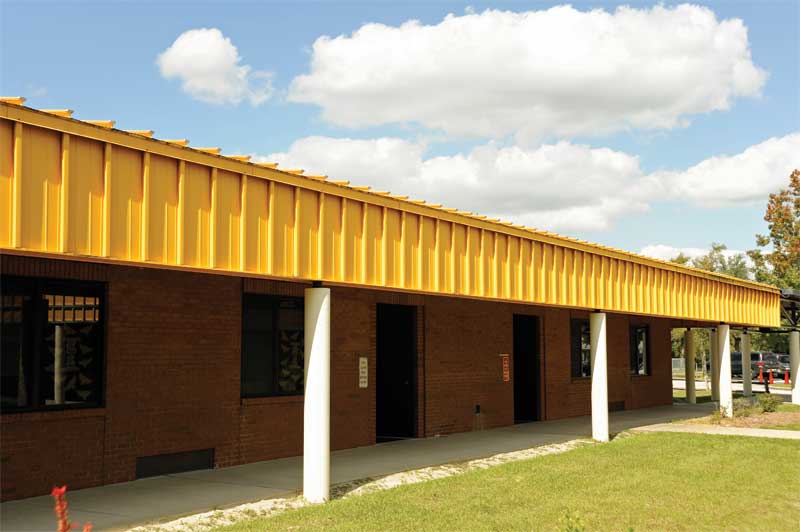
Aluminum and building use phase
Other life cycle benefits associated with aluminum are conferred during building service life, and stem from recent technological improvements to enclosure systems. Historically, glazed openings were major points of unwanted heat loss or gain for building interiors. However, the advantages of glazed aluminum fenestration products ensured their continued popularity and drove several advancements in their technology. Most recently, engineered systems—polymers or structural plastics set into specially designed channels—were incorporated into the framing of glazed curtain wall units to successfully interrupt thermal bridging and prevent energy transfer. Given the proliferation of high-rise structures involving curtain
wall construction, new improvements in curtain wall energy performance represent a major positive contribution in terms of life cycle performance.
For low-rise commercial or residential structures, metal-coil roofing can lower air-conditioning costs, reduce peak energy demand, and help mitigate urban heat island effects. In addition to the environmental benefits conferred by the roofing’s aluminum or zinc/aluminum-coated steel substrate, some specialty coatings contain ceramic and inorganic infrared (IR) reflective pigments, designed to reflect IR energy while still absorbing visible light energy. Reflective pigments appear the same color as traditional variations, but stay much cooler, lowering attic temperatures by up to 19 C (35 F).
For buildings of all sizes, modern aluminum alloys are structurally capable of supporting large expanses of glass, improving daylighting within buildings and reducing the need for electrical lighting.
Another common measure of a product’s environmental impact is durability. The strength of aluminum framing members can meet standards for both impact resistance (against windborne debris, etc.) as well as for blast loads (tested to 40,000 psi [275,790 kPa] without steel reinforcement). Metal roofing is durable enough to be specified (along with other nonflammable materials) by some local codes, especially in areas prone to forest fires.
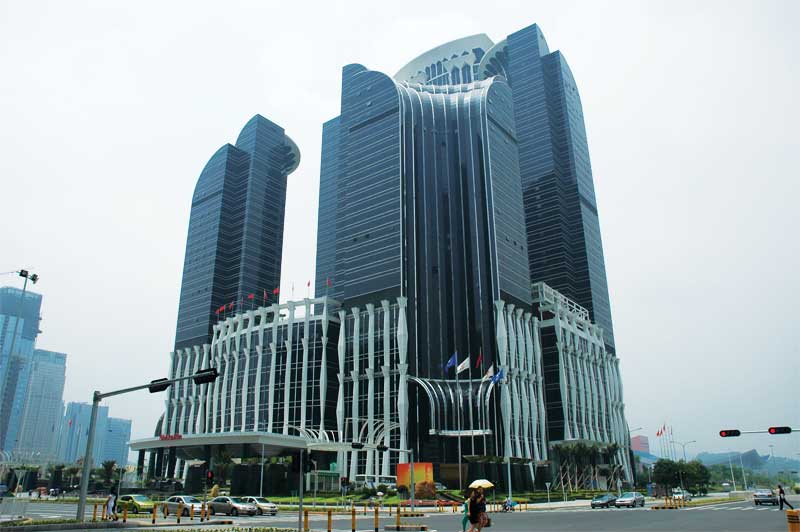
Any aesthetic or functional deterioration of a coated metal risks shortening the service life of a building or creating the need for extensive repairs. The extent of building surface area involved in high-rise architecture can make repair and refurbishment particularly challenging. Therefore, considerations such as the building finish become crucial.
Standards established by AAMA are voluntary and include specifications, performance requirements, and testing procedures for pigmented organic coatings on aluminum extrusions and panels (for factory-applied organic coatings only). As defined by AAMA:
- AAMA 2603, Voluntary Specification, Performance Requirements, and Test Procedures for Pigmented Organic Coatings on Aluminum Extrusions and Panels, identifies pigmented organic coatings that will provide a good level of performance, highlighted by one year of South Florida weathering exposure at a 45-degree angle;
- AAMA 2604, Voluntary Specification, Performance Requirements, and Test Procedures for High-performance Organic Coatings on Aluminum Extrusions and Panels, focuses on high-performance organic coatings that will provide and maintain a high level of performance, and requires five years of South Florida weathering; and
- AAMA 2605, Voluntary Specification, Performance Requirements, and Test Procedures for Superior-performing Organic Coatings on Aluminum Extrusions and Panels, focuses on organic coatings that will provide and maintain a superior level of performance, and requires a 10-year South Florida exposure.
Coatings meeting AAMA 2605 are appropriate for use on high-end building exteriors and are expected to last the lifetime of the building.
A related consideration when choosing a coating is the use of conflict minerals (i.e. those extracted in a geographic conflict zone and believed to fuel continued conflict.) It is advisable to work with a coating supplier able to provide a policy statement on its product in accordance with the U.S. Securities and Exchange Commission (SEC) final rule on conflict minerals.
Aluminum and waste
At the end of a building’s service life, aluminum is 100 percent recyclable. It can be repeatedly reused without any loss in quality or physical properties. Given recycling aluminum, as opposed to using new raw materials, reduces energy use
by more than 90 percent, the aluminum recycling industry has tripled in recent decades. The increasing popularity of and demand for aluminum also enhances the profitability of aluminum recycling.
Conclusion
Understanding PCRs, EPDs, and LCAs—as well as the software tools that assist in their implementation—is now critical
for any designer. LEED and other green programs are rewarding LCA more heavily, and as with other sustainability efforts, owners are becoming increasingly aware of LCA’s value. Fortunately, the demand for standardized life cycle information is being met by industry participation and disclosures.
Ben Mitchell is the extrusion coatings sales and marketing manager for AkzoNobel, a global paints and coatings company and producer of specialty chemicals. He has a bachelor’s degree in comprehensive science, as well as an MBA from Urbana University in Ohio. Mitchell started at AkzoNobel in 1990 as a lab chemist formulating polyvinylidene fluoride (PVDF) coatings, and moved into product management. He can be reached at ben.mitchell@akzonobel.com.
Vikas Ahuja is a senior account executive with Thinkstep, a company offering life cycle analysis (LCA) consulting, sustainability software development, and life cycle inventory databases. Ahuja holds degrees from the University of Chicago and University of South Florida, and has expertise in LCA, sustainable construction, and environmental transparency programs. He is based in Chicago and can be reached at vik.ahuja@thinkstep.com.