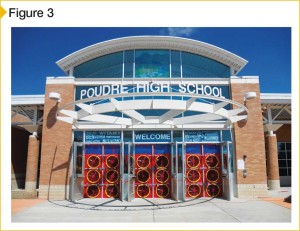
Establishing the OPR and levels of BECx
The newly created ASTM E2813 Annex A1, “OPR Development Guideline,” outlines the establishment of the owner’s project requirements in consideration of energy, environment, safety, security, durability, sustainability, and operation. This guideline is a prescriptive method that includes a series of questions representing “the minimum range of issues and concerns that must be considered under this practice during the development of the OPR to determine the level of commissioning and functional performance testing.” These queries cover general building characteristics, including:
- use and occupancy classification;
- construction type;
- anticipated service life;
- geographic location;
- energy performance requirements;
- project delivery method; and
- budget considerations for BECx activities and the overall project.
From this process, the owner, AOR, building enclosure commissioning agent (BECxA), and commissioning agent (CxA) create a scope of consulting and testing services.
ASTM E2813 establishes two levels of building enclosure commissioning: fundamental and enhanced. These levels are similar in terms of the BECxA’s role, and both are defined as architecture/engineering-related technical services performed on the owner’s behalf. In fundamental BECx:
- BECxA becomes involved in the project no later than the design development phase;
- preliminary OPR is reviewed and documented;
- there is a single design review of enclosure-related drawings and specifications; and
- limited number of lab and field performance tests are required, including:
– American Architectural Manufacturers Association (AAMA) 501.2-2009, Quality Assurance and Diagnostic Water Leakage Field Check of Installed Storefronts, Curtain Walls, and Sloped Glazing Systems;
– ASTM E783, Standard Test Method for Field Measurement of Air Leakage Through Installed Exterior Windows and Doors; and
– ASTM E1105, Standard Test Method for Field Determination of Water Penetration of Installed Exterior Windows, Skylights, Doors, and Curtain Walls, by Uniform or Cyclic Static Air Pressure Difference.
In enhanced BECx:
- BECxA is involved in the project no later than commencement of the schematic design phase;
- technical assistance and documentation are provided for development of preliminary OPR;
- at least three design reviews of enclosure-related drawings and specifications are accomplished; and
- additional lab and field performance tests are conducted beyond those in the fundamental process—examples include:
– ASTM E966, Standard Guide for Field Measurements of Airborne Sound Insulation of Building Facades and Façade Elements;
– ASTM E779, Standard Test Method for Determining Air Leakage Rate by Fan Pressurization; and
– AAMA 501.1, Standard Test Method for Water Penetration of Windows, Curtain Walls, and Doors Using Dynamic Pressure.
Core competencies
Successful commissioning of the building enclosure requires specific areas of expertise and experience in areas generally outside the capabilities of most mechanical/electrical/plumbing (MEP) commissioning firms. ASTM E2813 recognizes the need for qualified BECx firms, and the standard therefore requires agents to demonstrate a level of proficiency in the following building and materials science areas:
- enclosure-related materials, components, systems, and assemblies (with respect to durability, serviceability, interaction with other building elements, and performance characteristics);
- heat transfer;
- air infiltration/exfiltration (Figure 3); and
- moisture storage, transport, and diffusion.
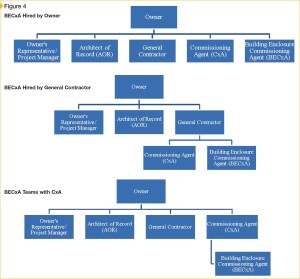
Firms must also be adept in understanding procurement and project delivery, along with performance test standards and methodologies for laboratory, mockup, and in-situ field tests.
While ASTM E2813 does not provide strict guidelines for what constitutes the “level of proficiency” in each of these core competencies, caution should be taken when selecting potential BECxA firms. Those companies with years of project experience in the core competencies generally possess the knowledge and abilities to contribute to a successful project. Potential BECx firms should be carefully vetted as part of the selection process to ensure a successful installation and performance of building components that are arguably the highest risk area of design and construction.
Phase descriptions
ASTM E2813 outlines a BECx process similar to those described in ASHRAE 0 and NIBS Guideline 3, and defines it in each of the project phases. The roles and responsibilities of the BECxA evolve as the project progresses; close communication with the owner, AOR, and general contractor is paramount to the commissioning agent’s successful integration with the project team. Depending on various factors, including the contract delivery method and OPR, the BECxA could be positioned in several locations within the project team. Possible scenarios are show in Figure 4.