Avoiding construction defects through quality control and assurance
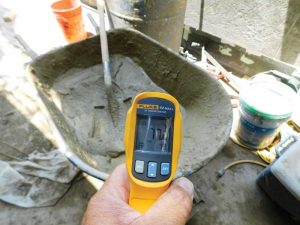
An important section of Part 1 is quality assurance (QA). This is where professionals can stipulate the quality of work, in terms of the installers and manufacturer requirements and training. This is where it should be specified that mockups are required and produced for approval, and there will be a QC plan which will be created and implemented during the installation process.
This is also where appropriate ASTM materials and test protocols are called out and require the specified materials to meet the minimum/maximum performance requirements for the intended application. For larger projects,
third-party laboratory testing should be required to verify not only the submitted samples of what is specified, tested, and meets the requirements, but also to test the actual material being supplied and installed on the job. This requires the specifier to be qualified on what are the appropriate products and performance criteria for the intended application, further verifying their suitability for the intended use. If the specifier does not have the knowledge to determine what is appropriate and suitable, they should retain an expert to consult along the way and only rely on the manufacturer’s recommendations which are in writing.
Also in Part 1, installer qualifications and experience with installing similar products in similar applications are established and required. It should state installers should have a minimum of five years of experience, and they also need to comply with the specified Tile Council of North America (TCNA) Handbook for Ceramic, Glass, and Stone Installation requirements. Doing so will help ensure quality installations. Specifications are used to stipulate quality and subcontractor qualifications in Part 1.
It should be required for the installers to demonstrate their crew of installers had training and have demonstrated their knowledge with the current installation standards. It should also be required for a non-working project foreman to be on the job-site full time, overseeing the work and implementing their own QC plan. The installation company should be required to verify all of these requirements with certificates of completion of training and with specific project references. A mock-up should be required as well, to further demonstrate execution and performance of the specified application, and to verify the aesthetic value as well.
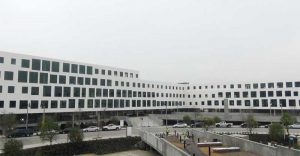
A very important requirement in the QA section is to require a QC plan, which will be implemented during the installation by a third-party inspector. There should also be a requirement for specific QA testing of installation materials to verify they are meeting the intended performance requirements. For instance, the International Building Code (IBC) requires exterior tile veneers to achieve a 344 kPa (50 psi) shear bond strength requirement for each applied unit. This should be tested early on during the actual installation, if not on the mockup. Further testing should also be considered periodically during the entire installation process. The reasoning behind this, is to identify a problem early on to avoid serious issues or delays; if it goes unnoticed, it can be a costly issue to resolve.