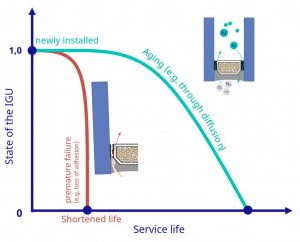
By Helen Sanders, Ph.D.
Building lifetime and building components’ service life are often-overlooked drivers of low-carbon design. Replacing components frequently compounds embodied carbon emissions, and operational carbon performance is only as good as their lifetime.
Insulating glass units (IGUs) are key building envelope components. Replacing single-pane glass to reduce operational carbon emissions also means glass with a 1000-year lifetime is replaced by an IGU with a 25- to 30-year lifetime. Increased embodied carbon has been traded for reduced operational carbon emissions.
Since the operational carbon and comfort benefits of IGUs are needed, the focus should be on specifying material to maximize their lifetime. Several factors affect an IGU’s lifetime:
• Edge seal material choice and design;
• Climate stresses and other application-specific loads;
• Manufacturing quality; and
• Installation quality and conditions
Edge seal material specification is critical. Dual-seal polyisobutylene (PIB)/silicone systems are ubiquitous in commercial applications because of silicone’s water- and ultraviolet (UV)-resistance and structural strength. Since silicone does not provide a gas or vapor barrier, a high-quality spacer with excellent barrier properties is important as there is no back-up. Ensuring excellent adhesion to the spacer is also crucial to prevent failures due to water pooling next to the PIB, spacer movement (for flexible systems), and over-extension of the PIB.
For these reasons spacer with solid metal vapor barriers—like aluminum, stainless-steel, and plastic hybrid stainless steel (PHSS) box spacers—serve as the benchmark for IGU durability. PHSS warm-edge spacers have the added benefit of matching non-metal spacers’ high thermal performance. It is tempting to incrementally reduce spacer system thermal conductivity by replacing the metal vapor barrier with plastic metalized films. When compared to PHSS spacer, this has a minor effect on the fenestration assembly U-factor, when simulating the appropriate sealant height. However, removing the metal barrier brings greater risk to service life, especially when used with silicone secondary sealant.
Loads on the edge of the glass caused by temperature and barometric pressure changes, and wind loads, causing IGU cavity pressure variations, can elongate the PIB. The higher the PIB elongation, the greater vapor and gas permeation, and the higher risk to service life. This can be mitigated with application-specific edge seal analysis, although this is rarely done.
Triple-pane IGUs are at a comparatively higher risk for high edge loads than dual-pane units because of their larger effective cavity. Controlling seal quality is also more difficult when manufacturing triple-pane glazing because two seals are not visible for inspection. Since the third pane also adds 50 percent more embodied carbon, a holistic view of operational carbon, embodied carbon, and service life should be employed during fenestration design and specification.
It may be possible to achieve the desired thermal performance without triple-pane glazing using wider thermal barriers in the frame, PHSS spacer, and/or a fourth-surface low-e in a dual-pane instead. These alternatives are low-embodied carbon solutions with low-risk to service life.
Manufacturing quality can be managed by specifying fabricators who make IGUs under robust certification programs like the IGCC®/IGMA® and IGMAC programs. Specifying contractors certified through the NACC program further supports a quality installation.
Helen Sanders, Ph.D., is a general manager at Technoform North America. She has more than 25 years of experience in glass technology, market development, and manufacturing, especially in functional coatings, insulating glass, and thermal zone technology for fenestration. Sanders has a doctorate in surface science from the University of Cambridge, England and is an active member of many industry organizations and in codes and standards development. She can be reached at helen.sanders@technoform.com.
I was so excited to see this article! Having worked in the historic preservation field for over 20 years, I can say that the subject of window replacement is a hot topic and what is at the core of this article is a subject that concerns me greatly–that is the short life expectancy of insulated glass–and that subject just not at all being considered by most people when they decide to rip out replace their old windows with new, only to find themselves in a new trap of having to replace windows every 20 years where the old ones were still fine after 100 years! I remain extremely cautious to new window technology and frankly, about to the point in my career where we will specify single glazed windows–get your efficiency from storm windows or curtains–and hire an architect that knows how not to put large windows on south facing facades in southern climates.
You should always consider restoring any wood window. Does not matter the condition. A restored window With a high-efficiency low E storm window will last 50 years and has the same efficiency or better than an insulated window
Quite apart from the appalling quality of some IGU components used (don’t let the bottom edge of your IGU become waterlogged or the lifespan of the IGU will be severly compromised) I have seen nothing that addresses the problems posed by the changes in pressure of the gas within the IGU. No attempt appears to be in the offing that reduces this change in internal pressure to zero. That’s right, no change in the internal pressure regardless of temperature, humidity, the owners name beginning with the wrong letter, the window being exposed to different weather, facing the wrong direction, being installed upside down, or any other of the unumerable “excuses” that limit the expectd life of the IGU to one or two decades. It seems any quick fix will do as long as it contributes (in the short term) to a reduction in carbon emissions.
When will some research become evident into allowing the IGU to breathe, say into an external bladder made of gas impermeable material that inflates from flaccid (in very cold conditions) to a swollen condition during hot weather.
Are we destined to dispose of IGU’s every decade or so simply because the sun shines or it rains.