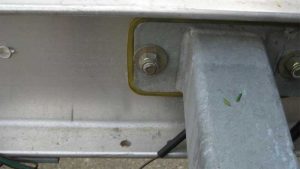
Preventing galvanic corrosion
Once the potential for and associated severity of galvanic corrosion is addressed, what are typical measures to avoid accelerated corrosion of any galvanized steel components? In theory, preventing galvanic corrosion is simple because it is achieved by interrupting only one component of the galvanic cell: the anode/cathode, the electrical connection, or the electrolyte exposure. In practice, the preferred solution will depend on project or design constraints.
Although it appears straightforward to specify the use of a single metal type within a project, often this is impractical because of availability or the material properties required for various building construction members. Where the direct combination of two different metals cannot be avoided, it is sometimes possible to select metals where the electrical potential between the anode and cathode are minimized. If evaluating the connection of aluminum-framed glass curtain walls to structural steel framing, hot-dip galvanizing the structural steel framing would reduce the electrical potential between the building frame and the glass curtain walls because aluminum and zinc surfaces are closer together on the galvanic series of metals than aluminum and carbon steel.
When reducing the electrical potential between the two metals in contact is unachievable, it is also possible to interrupt the electrical connection between them. This method involves placing electrically inert spacer materials with low moisture absorption between the metals such as neoprene, rubber, plastic, or nylon. Alternatively, the corrosion-inhibiting pastes, dried adhesives, and sealants can be used to separate the different metals (Figure 6). Spacer material selections should consider differences in design life and thermal expansion coefficients when compared to the base metals to avoid negative impacts on overall design life or intended performance. Specific to the specification of bolted structural connections, dielectric washers and bolt sleeves can be specified to achieve full isolation of the bolt, but all dielectric materials should be evaluated for compatibility with the loading condition (read “Opposites Attract: A Primer on Galvanic Corrosion of Dissimilar Metals,” by Christopher Hewitt, Alan Humphries, and Eric Twomey). For high strength connections, the impact on connection design and installation should be evaluated and quantified prior to the use of shims and washers if unaddressed by an existing standard (consult RCSC Research Council on Structural Connections, Specification for Structural Joints Using High-Strength Bolts, August 1, 2014).
As a third option, a galvanic cell can be interrupted by application of a durable liquid coating system to minimize exposure of the connected metals to the electrolytes in the environment. This method may be specified when electrical isolation is infeasible (slip critical connections, welded connections, etc.). Theoretically, painting only one of the exposed metals is enough to interrupt the galvanic cell. However practical measures often necessitate painting both metals to avoid accelerated corrosion concentrated in the areas of any coating imperfections on the anodic metal (such as the galvanized members). Although a viable method of preventing galvanic corrosion, regular maintenance of the paint is required to maintain barrier protection and minimize exposure of the more active metal.
Conclusion
Though galvanic corrosion has a reputation for being a very dangerous and complex corrosion phenomenon, the options for mitigation and prevention are straightforward: utilize compatible metals and/or favorable surface area ratios, provide barriers to break electrical contact between metals, or isolate the metals from the environment. It is best to not let the fear of galvanic corrosion prevent design professionals from achieving long-term corrosion protection and multifaceted metallic aesthetic using HDG steel. Understanding the causes of galvanic corrosion and when to implement the preventive measures will allow hot-dip galvanizing to be specified in an imaginative and sustainable way that can be preserved for generations to come.