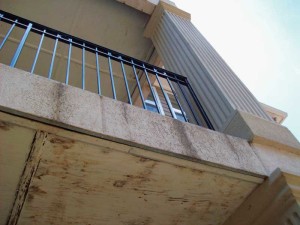
Photos courtesy Duradek
Waterproofing
Based on projects this author has seen, there seems to be a great lack of understanding of this step’s importance. To determine the best practice, several questions must be answered:
- Is this deck serving as the roof over habitable space?
- Does it require a roofing membrane to meet the local building code?
- Should that membrane be applied by trades who specialize in roofing details or by tile-setters?
- Is the membrane suitable for tile to be applied to?
- Is it compatible with polymers that are part of the thin-set bonding adhesives?
- Is it firm enough to prevent cracking of the tiles?
- Will it soften in the heat while still supporting the tile assembly?
- Has it been tested to meet the traffic requirements of the job?
- Does the manufacturer guarantee it for this end use?
Many beautiful tile jobs have failed partly because they were installed directly over modified-bituminous (mod-bit) roofing—a material that is incompatible with the bonding adhesives, too soft, has no testing to support its use for this application, and not guaranteed by any of the manufacturers for this end use.
Thin-set bonding adhesive
The desire to save money by choosing a less expensive thin-set bonding adhesive (i.e. a polymer-modified mortar) has been a large source of failure. Not all products are equal, and certain properties are required for outdoor tile installations.
Higher-priced thin-set mortars tend to have better polymer additives, allowing for more movement. With the constant movement resulting from changing temperatures, the thin-set is trying to hold the tile in place. The better quality the thin-set, the longer it continues to provide adhesion.
Outdoor installations are obviously susceptible to dramatic temperature and humidity fluctuations; the thin-set must be capable of performing even under wet and freezing conditions. Some experienced tile-setters will not do an outdoor job unless it can be tarped off to keep it out of direct sun and rain for a significant period, allowing for proper curing of the materials. There are fast-setting thin-set adhesives available for cooler temperature installations—manufacturer recommendations should be followed.
An improperly built and prepared surface may provide small areas that allow water to pond. Prolonged dampness may promote the re-emulsification of the mortar that would impact the adhesion. Manufacturers should provide guidance on this issue.
With respect to efflorescence, the white stains that seem to ooze out of the grout joints or from the outer edge of the tiled surface might be a result of the wrong choice of thin-set or grout material.2 (For more on this topic, see the article, “Why Red Brick Turns White: Understanding Efflorescence,” by Joseph “Cris” Crissinger, CSI, CCS, CCCA, ASQ, which can be found in the November 2012 issue of The Construction Specifier. To read it, visit www.constructionspecifier.com and select “Archives.”The manufacturer will recommend the correct materials to be used to reduce or eliminate efflorescence.
Choosing the tile or stone
Some of the failures of outdoor tile jobs are caused by wrong product choices. Freeze-thaw resistance and water absorption characteristics must be researched to ensure the product is matched to the climate in which it will be installed. For instance, this author has seen slate tile installed in a region that experiences many annual freeze/thaw cycles. The stone was flaking apart, which is something that could have been predicted considering the properties of the particular product. If the supplier does not have the information, another product or supplier should be chosen.
Tile installation techniques
The tile-setter’s skill is extremely important to the eventual success of the job. Voids in the thin-set coverage will provide space for moisture to collect. While difficult to completely avoid air spaces, the goal is to get at least 95 percent coverage of the bonding adhesive.
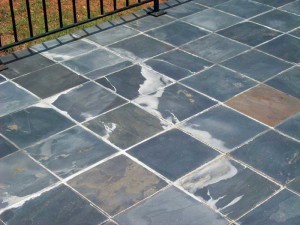
Tile, thin-set, and grout are rigid materials. The tiled assembly is going to have substantial movement as the temperature changes and provisions are required to allow for that movement. Industry standards call for ‘soft’ expansion and control joints to be provided as per Tile Council of North America (TCNA) Detail EJ171 or Terrazzo, Tile, and Marble Association of Canada (TTMAC) Specification Guide 09 30 00, Detail 301MJ. These ‘soft’ joints tend to look visibly different than the other grout joints. As a result, some choose ‘form’ over ‘function,’ and suffer the consequence of erupting tiles. The laws of nature always prevail.
Details
Waterproofing is all about the details. Failures seldom happen in the center of a roof or deck, but rather on the perimeters. Special attention should be paid to corners, door openings, posts, pony walls, drains, scuppers, outside perimeter finish, inside perimeter (up the wall behind the siding and building paper), and railing attachments.
Waterproofing or roofing?
While it seems there are many manufacturers providing waterproofing products suitable under tile, only a few offer roofing materials for this purpose. Specifiers may be wondering where the difference lies. After all, a material is either capable or incapable of keeping water out.
The rationale involves the liability manufacturers are willing to take—roofing infers a lot more than waterproofing—and the skills required for properly applying the membrane. This application demands trades professionals be familiar with the intricate details presented by decks and balconies.
In the front of my house I have a second floor balcony off of my bedroom. The out door balcony has a tile flooring and no roof above. When it rains there is a leak coming from tiles and the drain. Water is leaking down into ceiling onto floor outside the front porch near front door on ground level.
I have the same problem as Michael Lawson