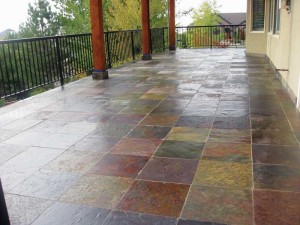
Waterproofing options for under exterior tile
When the deck is over living quarters, there must be a roofing membrane and the assembly needs to be installed with roofing principles in mind. However, even when it is over unoccupied space and there is no specific building code requirement, the installation details should not be less stringent, considering the consequences of leaks.
When researching products for waterproofing decks and balconies to which tile will be applied, specifiers may notice the frequent absence of the word ‘roofing.’ As mentioned, many manufacturers of these systems want nothing to do with the headaches and liabilities involved. There are also details one would never consider using in a non-roofing application, such as finishing a membrane on the flat horizontal surface without turning it over the edge and then caulking the leading edge. Granted, most details are intended for concrete decks and balconies, but for light-commercial and multi-family construction discussed in this article, wood framing is more likely.
In terms of specific ‘roofing’ products, mod-bit materials are among the most common. Mod-bit is asphalt with added modifiers (e.g. atactic polypropylene [APP] or styrene butadiene styrene [SBS]) to give it plastic or rubber-like properties. Rolls of modified bitumen membrane come in widths of 914 mm (36 in.) to approximately 990 mm (39 in.) and cover an area of about 9.3 to 10.4 m2 (100 to 112 sf).
Mod-bit roof systems consist of one-, two-, or three-ply systems (base sheets with no cosmetic finish and cap sheets). The cap sheet membranes may be applied using a torch (the back of the sheet has extra asphalt on it that, when heated, bonds to the substrate) or be self-adhered (removing a release paper on the back exposes a sticky surface which adheres to the substrate).
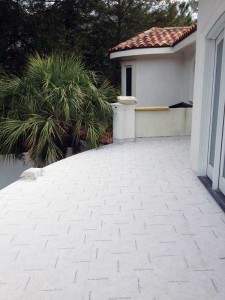
To the best of this author’s knowledge, none of the manufacturers of mod-bit products supports tile installations directly to the roof membrane; therefore, there is no promise it works in these applications. Additionally, the asphalt in these products is incompatible with the mortar in the thin-set or the grout lines; it may bleed through, causing discoloration. An uncoupling system is usually required to isolate the mod-bit membrane from the tile and bond-coat layer.
More importantly, when the mod-bit softens as it heats up, it can be compressed. This could allow the tile or the grouting to crack from the movement from traffic on top. Any product designed to have tile installed overtop will have test results from the Robinson test (ASTM C627, Standard Test Method for Evaluating Ceramic Floor Tile Installation Systems Using the Robinson-type Floor Tester) to verify it is capable of supporting weight of people and equipment. (The Robinson Floor-tester is a unique machine capable of carrying out the test for an ASTM C627 designation. It verifies the suitability of a flooring system for a particular type of installation, such as tile. At the very least, a ‘Residential’ rating should be required.)
The traditional method of providing roofing protection under tile would be to install a suitable roofing product like polyvinyl chloride (PVC), ethylene propylene diene monomer (EPDM), thermoplastic polyolefin (TPO), mod-bit, or liquid-applied urethanes with a thick-bed mortar system on top to which the tile is attached. (It is important to know whether the manufacturer supports use of its product in such a way.)
The tile may be uncoupled from the mortar bed, the mortar bed uncoupled from the roofing membrane, or both. There may be a drainage layer above the roofing membrane to allow any moisture to escape along the drainage plane. This system is expensive and thick (at least [1 ½ in.] above the membrane); it is also complicated—there may be as many as seven or eight layers involved in the system.
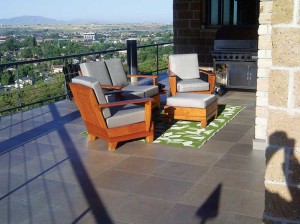
Other components
There is a frequent misconception anti-fracture membranes allow elimination of expansion joints. There must always be soft joints in the tilework to allow for expansion and contraction. Guidelines for expansion joint placement are given in the TCNA Handbook. The exact placement of expansion joints is a function of many items, including:
- exposure to sunlight and the range of high to low temperature;
- moisture;
- aging of the concrete (where relevant);
- structural movement; and
- expected loading.
There seems to be at least two theories about the necessity of a drainage or uncoupling mat. One is tile or stone can be directly bonded to an appropriate membrane with some crack-isolation properties, when used with the appropriate thin-set adhesive recommended by the manufacturer for the specific climatic region and job conditions (i.e. it can withstand the elements and provide the adhesion required even in the presence of moisture).
In the front of my house I have a second floor balcony off of my bedroom. The out door balcony has a tile flooring and no roof above. When it rains there is a leak coming from tiles and the drain. Water is leaking down into ceiling onto floor outside the front porch near front door on ground level.
I have the same problem as Michael Lawson