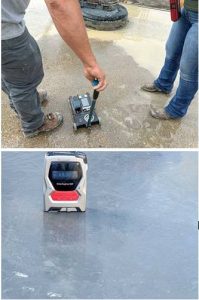
Recommendations for minimum periods of curing from the ACI are generally around the time concrete reaches 70 percent of the specified compressive strength. This minimum level can take shorter or longer periods of time, depending on the aforementioned factors, as well as what manner of curing the team uses. There are many different approaches to curing. They vary in cost of application as well as effectiveness. Wet curing has long been the gold standard for concrete among many contractors, but its cost and schedule demands often lead project teams to choose lesser performing methods. In recent years, internally cured concrete (ICC) used in various projects, such as California’s 415 Natoma by Brookfield Properties, Virginia’s Amazon HQ2, Florida’s DuraMag plant, and Waco ISD’s Kendrick Elementary School in Texas, has developed beyond lightweight clay and shale aggregates to include cellulose fibers (CF), nano modified cements (NMC), certain nano silicas, and other technologies that are proving more cost effective while delivering wet cure-like results in more time effective manners.
Higher curing temperatures can assist in achieving early strength gains, but certain temperatures can also decrease strength. Curing in extreme hot or cold weather requires additional care and preparation. ACI 306.1, Standard Specification for Cold Weather Concreting and ACI 306R, Guide to Cold Weather Concreting, are reliable sources for this issue.
Low-carbon concrete curing
While ASTM C31/C31M, Standard Test Practice for Making and Curing Concrete Test Specimens in the Field, provides a starting point for traditional concrete placement, it has not, as of yet, been sufficiently updated for low-carbon concrete, respecting the impact to massive cement reductions and the changing qualities of supplementary cementitious materials.
Low-carbon concrete is a new material. Treating it like old concrete (i.e. using older curing, consolidating, and finishing methods) will manifest a variety of problems including delayed day of strength requirements, more change orders for repairs, and increased potential for ironically shorter lifecycles, therefore defeating sustainability objectives. A simple indicator that a plan’s low carbon curing might be insufficient are longer than normal curing schedules. Delayed day of strength requirements are not necessary and add significant budget increases that may push owners away from opting for low carbon concrete solutions.
Approaches such as ICC are proving promising in meeting the challenges of low carbon concrete, including earlier strength gains, but also it creates the need for substantial updates to documentation and planning. Construction professionals should also update themselves, setting aside earlier experiences and habits to approach low carbon concrete as a new subject and allow them to learn and become students again.
Architect Kristina Abrams, notes, “If we, as Architects, treat low-carbon concrete the same way we approach traditional concrete, we will not truly benefit from innovation and cost savings.” Teams should research which approaches are most beneficial for their circumstances and keep in mind that low-carbon concrete field is still relatively new. Supplier teams must take responsibility for providing products and materials that can meet the requirements of each of the four steps of concrete production. This is crucial to prevent extended cure times and ensure the production of high-performing concrete.
Protection and usage
Finally, the often overlooked and essential component is protection of concrete once it is cured. Cured does not mean concrete is “good to go,” strength gain can be greatly impaired by leaving concrete to the elements, being wetted by inclement weather, freezing conditions, or high heat. The Concrete Plan must account for and provide equipment and materials necessary to protect concrete during delivery, placing and finishing, and curing from heat/cold, wind, precipitation—anticipating that these conditions could change throughout a scheduled placement.
In addition, the Concrete Plan has to account for the proposed usage of the concrete—based on the needs of floor covering trades, or special finishes applied to the concrete (polished, stained, ground, high performance coatings); or the way the floors will be used, which could require a level of performance for ultimate floor flatness/floor levelness (Ff/Fl) that exceeds normal work practices.