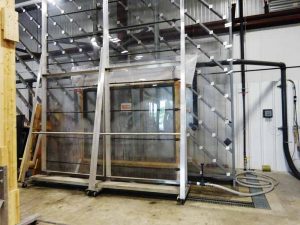
Approving the shop drawings during the submittal process, with the mentality of figuring it out in the field, can lead to owners requesting the design team to complete the review, in order to not hold up production or ordering materials, both of which could result in costly delays. However, an incomplete shop drawing package, which is rushed through the review process, may ultimately cause a longer delay, due to possible window leaks discovered during field testing due to the original design details not being followed.
Coming up with a solution to address the leakage and implementing it may cost the project more time than if the shop drawings were complete and followed from the start. Further, a ‘figure it out on the fly’ mentality can result in inadequate field details that can put the project at risk for condensation or water leakage and no paper trail to hold the correct party accountable.
There is a balance between holding firm on the correct detailing in a set of shop drawings, versus accepting a manufacturer’s typical package without any project-specific detailing to keep the project moving. When it comes to reviewing project submittals and shop drawings, the goal is to provide helpful and actionable reviews without derailing the project budget and schedule with extreme requests. A designer who takes an uncompromising position may end up causing more problems (e.g. delays, costs, or an owner who overrides them) than one who can identify and accept reasonable compromises to the design.
Window testing
The proof test of all the thorough detailing in the design and reflected in the shop drawings is the first window test. This is when the fenestration is put to the test for air and water leakage. However, if conducting a performance mock-up (PMU), additional tests may also include structural components, such as inter-story drift and load testing or condensation resistance modeling.
Ideally, this first test happens during a PMU, but for simple configurations using off-the-shelf (i.e. pre-tested) windows, the first test may be completed in situ. For field testing, only air and water leakage are tested. Another window test that may be done at, or ideally sometime before, the start of the construction phase is a lab test at the manufacturer’s facility to confirm that its internal assembly procedures results in a sound system, or that a particular manufacturing line is producing windows with the same performance as an originally tested sample.
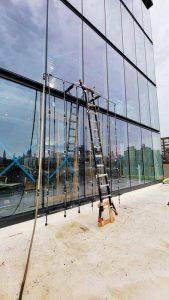
Prior to testing any units on the job, a field-testing protocol inclusive of all the fenestration systems should be documented and agreed upon by the project team. This ensures everyone is on the same page, and that the contractor is aware of all testing requirements early in the construction phase. More importantly, it helps avoid disputes over test results if the passing criteria and test procedures are clearly laid out and agreed to by the relevant parties.
Laboratory testing is a hybrid solution between a fully constructed, project-specific PMU and in situ field testing. A lab test on the window unit can be done for semi-custom systems that may have a unique size or atypical framing/glazing conditions, but are based on a previously tested assembly, where the budget cannot accommodate a PMU; typically, these tests are done at the manufacturer’s facility. This would include air, water, and structural testing of the window unit.