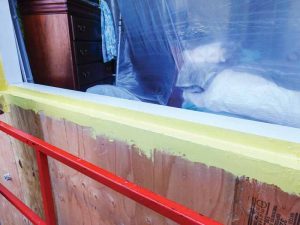
In some instances, with smaller non-domestic manufacturers, addressing leaks can be limited to additional sealant to frame joints, which are not required per the manufacturer’s installation instructions. This makes it even more difficult for the owner to hold the contractor responsible for these repairs since it is not standard protocol. These repairs may also affect the warranty provided by that manufacturer. Larger-scale non-domestic manufacturers have better support and repair options and may have local representatives to figure out the issue.
Unexpected site conditions
Some level of change during construction or unexpected site conditions that vary from the design are inevitable. These can be due to owner-directed or contractor-led changes, or because of unforeseen conditions as the building is constructed. Another potential scenario is where a detail is installed, but it is not similar to the drawings, and the owner is now seeking the design team to come up with solutions—working with what is installed without compromising performance. This results in the design team needing to document the changes and how the field conditions differ from the design in case the change leads to a lower performance of previously approved systems or details. In some cases, it is also on the shoulders of the design team to work with the changes that occur and offer constructive recommendations that will still benefit the project. It is imperative for the design and construction teams to work together to detail surprise conditions effectively and efficiently.
Sill flashing
One detail which is constantly under the threat of being value-engineered out of the project is the fenestration sill flashing. Ideally, the design includes a membrane sill pan with an upturned leg and end dams and a metal sill pan with an upturned leg, end dams, and fully soldered corners. When it is time to price this and the value-engineering process is underway for the fenestration systems, the metal sill pan is often the first thing to go. Common reasoning includes the installer saying they have not used sill pans in the past and have not had problems or the manufacturer not requiring a sill pan. Both arguments can sound very convincing to an owner who needs to reduce their budget, although owners who have experienced window leaks on past projects will be much more hesitant to make this change. The following will describe alternative options in the field in lieu of the metal sill pan flashing.
Membrane sill pan
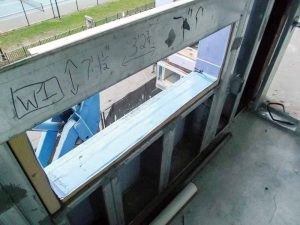
If the metal sill pan flashing is removed from scope due to cost issues or coordination concerns, then the next best option is a standalone sheet membrane sill pan with an upturned leg and end dams. This will still capture any leaks through the window system and prevent them from migrating to the interior as long as the inside corners are properly sealed. This installation is more favorable as the window installer or waterproofing professional can install the membrane sill pan without having to potentially introduce another trade (roofer/sheet metal worker). This can also be installed in the field and is easier to cut and fit in the rough opening compared to a sheet metal sill pan.
Fluid-applied membrane sill pan
Another sill pan configuration often used is a fluid-applied membrane. This is common in exterior insulation finish systems (EIFS) as they regularly use a fluid-applied weather barrier as part of their proprietary system. A caveat to using fluid-applied membrane sill pan flashing is that its installation is very sensitive to workmanship, especially at the inside and outside corners of the sill, and in maintaining the required membrane thickness.