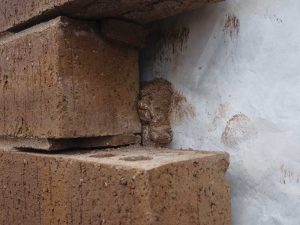
ASTM C207, Standard Specification for Hydrated Lime for Masonry Purposes, outlines four types of hydrated lime:
- N – normal hydrated lime;
- S – special hydrated lime;
- NA – normal air-entraining hydrated lime; and
- SA – special air-entraining hydrated lime.
It should be noted some building codes prohibit the use of air-entraining materials in mortar due to the resulting reduction in bond and compressive strength. Therefore, Types NA and SA should not be specified for masonry mortar. The special types of hydrated lime (S and SA) offer the advantages of higher early plasticity and water retentivity. For these reasons, Type S
is the most commonly specified hydrated lime type for masonry mortar. Depending on the amount of lime used in the mortar mix, bond, workability, water retention, and elasticity can be adjusted.
Sand or aggregate is a filler material and help to reduce shrinkage in mortar. Different sands or colored aggregate can also be used to achieve a specific mortar texture or color. ASTM C144, Standard Specification for Aggregate for Masonry Mortar, specifies aggregate for use in mortar shall consist of natural or manufactured sand, which can be crushed stone, gravel, or air-cooled iron blast-furnace slag. Admixtures can result in a change of properties such as increased workability or a decrease in setting time. They can also be used to achieve a specific color. Water-repellent admixtures are commonly specified for mortar when concrete masonry is used for the veneer. They need to be coordinated with other water-repellents employed in CMUs. Cold-weather admixtures to allow installation of masonry at temperatures below 4 C (40 F) can be used with caution, although specifiers should carefully review the effect on future durability and performance. If any type of admixture is to be used, the same material should be employed consistently all across the project for consistency of appearance and performance.
Pigments could be employed to achieve a certain color, although colored aggregate may be preferable for distinctive or bold hues. The use of an excessive proportion of pigment can also reduce strength or durability.
In addition to mortar components, ASTM C270 outlines four mortar types and recommends in what conditions they should be used. The four mortar types are M, S, N, and O. All of them have different minimum strength, water retention, and air content requirements depending on the type of cement used in the mix. Table 1 in ASTM C270 outlines these requirements and should be referenced when preparing construction documents. Type N mortar is recommended for loadbearing walls. For non-loadbearing walls such as veneer construction, Type N or Type O mortar should be used. Type O mortar can be employed if the wall is unlikely to be exposed to freezing temperatures when saturated or subjected to high lateral loads.
The mortar ingredients (Portland cement, hydrated lime, sand, and any pigments or admixtures) can be blended onsite, although quality control (QC) to ensure consistency between batches can be challenging. Alternately, custom preblended dry mixes with all ingredients for the project are readily available. These mixes only require the addition of water onsite. (Product data should be reviewed to understand the admixtures in the mix).
In addition to selecting the appropriate mortar based on how or where it will be used, it is also important to evaluate how the selected mortar will interact with the selected brick when specifying a mortar type. For example, mortar typically bonds best with masonry units with a moderate initial rate of absorption.
Veneer ties and anchors
In a veneer wall system, the ties are intended to connect the backup wall construction to the outer wythe of masonry, transfer lateral loads, and accommodate in-plane differential movement. An effective veneer anchor system should be securely tied to the backup construction and veneer masonry, have sufficient stiffness to accommodate lateral loads, and be corrosion resistant.
There are many types of veneer tie and anchor systems for new construction including:
- corrugated metal and rectangular ties, referred to as unit ties;
- ladder and truss-type ties, referred to as horizontal joint reinforcing; and
- various types of adjustable veneer ties.
Corrugated metal ties are not recommended unless used in low-rise, wood-framed construction with masonry veneer. Due to the width of the corrugated ties, they may provide an avenue for moisture to bridge the air space. They are more susceptible to corrosion than wire ties and sometimes experience insufficient bond with mortar at joints.
Rectangular, ladder- and truss-type veneer ties are best suited for multi-wythe masonry construction. With these masonry tie systems, the CMU backup wall and veneer are built simultaneously with ties installed at the bed joints. These ties provide strength and stiffness to accommodate lateral forces, but have the potential to restrict expected in-plane movement or deform under service loading.