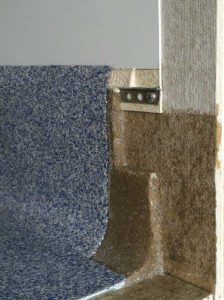
Surface preparation
The most important foundation of a resinous flooring system is the substrate it is being placed on. The most common substrate is a concrete slab that is steel troweled or has a ‘darby’ finish. The top or ‘cap’ of the concrete substrate is the weakest part of the slab. Even if the resinous system can penetrate through the top of the slab, the ‘cap’ still may delaminate from the rest of the slab which would still result in a failure. This is one reason concrete can spall.
To prevent this from being a weak foundation of the flooring system, a concrete surface profile (CSP) must be specified. That specification is on a one to 10 scale with the latter being the most aggressive profile for products that will be laid thicker than a 6.4 mm (0.25 in.). This is important to specify correctly based on the system because the CSP may show through a thinner system, and the substrate may need to be patched to not telegraph through. On the other hand, if a substrate is not prepared well enough, the product applied may delaminate and fail.
How the CSP is achieved is up to the installer as they are liable for the installation portion of a warrantied project. Depending on the specified profile, project size, and specified system, an installer can choose a range of mechanical surface preparation techniques. Even though there are different methods, the entire substrate must be mechanically prepared to the specified profile. Commonly used equipment includes grinders, shot blasters, scarifiers, scrabelers, hammers, and sometimes even needle guns.
Moisture mitigation
The best way to avoid needing to specify a moisture mitigation component is to specify a vapor barrier (a.k.a. vapor retarder) under the concrete slab. A concrete slab on grade acts like a sponge and will absorb moisture from the soil or ground. In some cases, when this moisture is left unchecked, it can force the resinous system off the substrate causing a failure by delamination.
When writing a specification, it is important to include what the highest amount of moisture a resinous flooring or coating system can take before delamination occurs. This way testing can be performed and, if the result is higher than the upper limit of the product, a mitigation solution from the manufacturer can be used prior to the specified system to prevent the rest of the floor or coating from lifting off of the substrate.
The two most common testing methods are calcium chloride and relative humidity (RH) probe/meter. Both provide numbers correlating to the amount of moisture coming through the slab allowing a recommendation to be made to curb the moisture and still allow a successful flooring or coating installation. ASTM International standards for the two testing methods are ASTM F1869 as well as ASTM F2170.
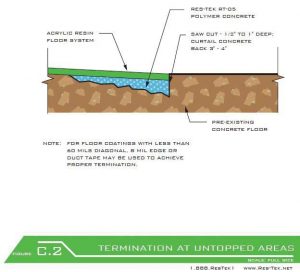
Cove base
One of the most popular reasons for specifying a resinous flooring system is because they are impermeable to water. So, a resinous system can act as both a user-friendly flooring system and as a waterproofing system. An important aspect of creating a floor that has a ‘bathtub effect’ is to specify a cove/wall base.
Typically, projects will only need a 102 or 152 mm (4 or 6 in.) cove base. Most projects will need 102 mm, while commercial kitchens and other wet areas will require 152 mm. Depending on the finish and the chemistry of the system, one may be able to specify that a product goes even higher up the wall.