Transitions and terminations
One important detail often overlooked in a specification is knowing what terminations and transitions to call out. This varies based on what type of flooring the resinous flooring is finishing up against. For example, if meeting up with a polished concrete finish, the resinous system will need to finish at ‘zero’ or flush with the concrete substrate that is going to be polished.
The most important consideration regarding transitions and terminations is the resinous system cannot be placed thin at these locations. If the thickness is not correct or matching the rest of the system, the terminations will be a weak point in the flooring system and will be the first points of failure either by delamination or chipping. After this has occurred, it can spread to the rest of the system leading to further failure. The correct way to install these terminations is to ‘key’ them in. ‘Keying’ the substrate means to remove a certain amount of concrete to create a void that is the correct thickness to accept the resinous system as it is poured in place.
With the best practices established for all resinous flooring, it is important to also look at the pros and cons of the most common resinous flooring chemistries.
1. Epoxy
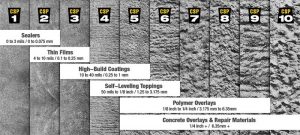
Probably the most well-known chemistry in resinous flooring, epoxy is one specific class of polymers that contain epoxide groups, hence their name. There is an extremely large range of quality in epoxies. Flooring and coatings typically fall in the middle of that range. While these are not the same high-end formulations NASA uses, the space agency sources the same base chemistry as flooring, paint, and adhesive manufacturers.
The number of system designs using epoxy is endless and covers a wide spectrum of styles—from thin mil all the way to troweled down mortar systems. A few pros for using an epoxy system are its relatively reasonable material cost, epoxy systems usually have an attractive high-gloss finish and, depending on the formulation, can have zero VOCs in their make up.
Some cons to using epoxies are not all are formulated or produced with the same quality. For example, there is a difference in residential-grade versus industrial-grade epoxy. Typically, they all have a long cure time (eight to 12 hours) which only amounts to about 95 percent cured. Reaching 100 percent cured usually takes between seven and 10 days. Epoxy is also not UV stable, which means it will eventually yellow and color shift when exposed to UV light. This is especially important when using these flooring systems in an area exposed to sunlight or fluorescent light for extended periods such as grow houses or exterior applications. Although a system may use epoxy, it is rare one will find a manufacturer that will recommend finishing with an epoxy topcoat versus applying a urethane or polyaspartic topcoat due to them having better physical characteristics.
Further, because of the wide variety of epoxy system designs and qualities available, it is important that a specification be very specific. This can include the manufacturer’s system name or, at a minimum, type of resin, the application method, finish selection for texture and color, and an overall system thickness.