Installation practices
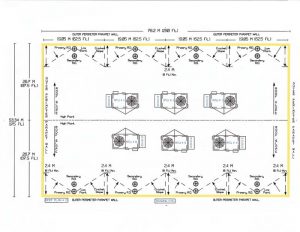
As mentioned earlier, when the roof slopes from the high point to the low section and toward the outer perimeter parapet walls, the leading edge of the tapered rigid insulation board must extend a minimum of 2.4 m (8 ft) out from the inside face of the parapet (Figure 8). This creates a footprint for the crickets that make up the well-defined waterways and provides a way for the elimination of rainwater through the primary roof drains.
In this example, the primary and secondary roof drains are set perpendicular to the parapet walls at the low point of the roof structure. The tapered rigid insulation boards are positioned so the point of entry is directed into the center of the primary roof drains. The secondary roof drains must be elevated a minimum of 50 mm (2 in.) above the finished surface of the completed roof system assembly.
Typically, certain codes require the conductors and horizontal and vertical drainpipes of the secondary roof drains to be plumbed independently and discharged through the exterior wall of the structure at a height between 1.5 and 2.4 m (5 and 8 ft) above ground level. This way, if rainwater is visible to occupants of the building and/or a passerby, it would indicate the primary roof drains are not functioning as intended.
Limitations
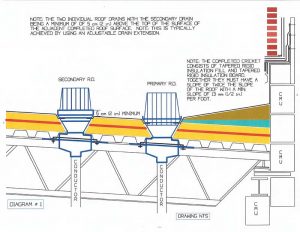
Figure 9 illustrates the components of a well-designed and properly functioning internally drained roof system (contingent on having the roof drains, conductors, horizontal piping, and drainpipe lines sized properly). Briefly, the components of a primary and secondary roof drain assembly include the underdeck mounted cast iron clamps (used to secure the drain bowl to the roof deck, a cast iron ring clamp assembly (utilized to secure the roof membrane to the drain), and a cast iron strainer basket.
In Figure 9, the first item to recognize is the 6-mm (¼-in.) per foot slope of the roof deck is created by sloping the steel infrastructure, which is likely to be the least expensive and most functionally sound method, from a good roofing practice perspective. Additionally, there are two discrete layers of ISO rigid insulation board, installed with the edges offset in both directions by a minimum of 152 mm (6 in.) to prevent thermal bridging. Depending on the specifications, they may be simultaneously mechanically fastened to the metal roof deck. The secondary drain is positioned a minimum of 50 mm (2 in.) above the surface of the completed roof system assembly.
The tapered rigid insulation fill and board, making up the well-defined waterways throughout the roof, must be built to a point to create a cricket measuring twice the slope of the roof deck, with a 13-mm (½-in.) minimum slope.
In the author’s experience, it can be problematic to use lightweight concrete and tapered ISO insulation board during the time of installation, especially in cold climates. The roof deck must be perfectly flat to achieve the required slope for tapered rigid insulation board systems. Additionally, cost would be a determining factor depending on the actual overall thickness of the ISO material making up the roof substrate. Also, depending on the overall thickness at the highest point of the insulation, it could get built-up pretty quickly. For example, in the author’s experience, tapered insulation plans are very much a function of thickness at the high points (with a requirement that it is designed to be installed on a flat metal roof deck). At times, it was observed the screws were 610 mm (24 in.) long to secure the insulation to the steel roof deck. This condition typically occurs on large low-slope commercial buildings. Further, temperature and humidity restrictions exist if some types of expanding sprayed-in-place adhesives are specified for use.
Temperature restrictions, high-wind consequences, and curing time are all factors to consider when using lightweight concrete. The temperature must be above 4.4 C (40 F) for 48 hours prior to and after placing the material. Additionally, if there are high winds during the application, the finished surface could be significantly impacted and uneven much like the surface of water is during high winds, depending on the speed of the winds and the height and location of the building. Also, curing time requires up to 48 hours or more of set up time—this can be affected by wet weather after the initial application, and prior to the installation of the new roof system.
Conclusion
Even though the internal drain system is more expensive than other methods, the benefits far overshadow the difference in initial cost, especially when one considers ruling out the premature deterioration and failure of the roof system selected to protect the building and the structural integrity of the roof deck. However, the most important element is the safety of the occupants.
When all elements of planning, designing, and constructing a low-slope commercial roof with internal primary and secondary roof drains come together, it provides a water handling system with low maintenance, high function, and extended value as the assembly will most likely last until the building structure is decommissioned.
REFERENCES |
● Roof Drainage, authored by Steven Patterson, PE, RRC, Medan Mehta, PhD, and J. Richard Wagner, PE, and published by the Roof Consultants Institute Foundation (RCIF). ● The Manual of Low-slope Roof Systems by C.W. Griffin and Richard Fricklas. ● International Building Code (IBC), 2009. ● Factory Mutual (FM) Global, “Property Loss Prevention Data Sheets,” October 2012. ● The Importance of Proper Roof Slope, by Mark S. Graham. ● InspectAPedia – Roof Drainage Requirements & Specifications. |
Anthony J. Katona, CDT, is president of Alliance Roof Consultants Inc., and has been providing professional services as a building envelope and commercial roof consultant since 1999. With more than 30 years of construction experience, he has an extensive background in determining the source of unwanted moisture migration within troubled buildings. Katona has served as president of the Delaware Valley chapter of the Roof Consultants Institute, now known as RCI, Inc. He has also served as a member of the Editorial Advisory Board of The Construction Specifier. Katona can be reached at alliancerc@comcast.net.
This article is for informational purposes only. Katona does not warrant or assume any liability for the accuracy, completeness, and/or fitness of the article for any project, and readers are strongly advised to utilize their professional experience, knowledge, and judgment, in using the information contained in this document.