by Julie Holmquist, Andrea Moore, and Casey Heurung
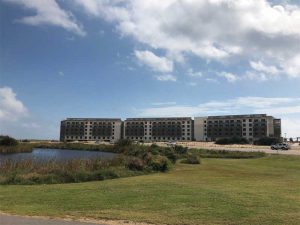
Marine environments are known for posing an elevated threat of corrosion to metal. Engineers take special precautions to address this problem when designing reinforced concrete structures in these regions. Bio-based migrating corrosion inhibitors can be an important design factor when building a sustainable structure in a corrosive marine environment.
The first phase of the Gulf State Park master plan and enhancement project in Baldwin County, Alabama, provides an example of how bio-based migrating corrosion inhibitors are able to mitigate corrosion with an eye to sustainability and resiliency. The project was recognized by Partners for Environmental Progress (PEP) with a 2019 Environmental Stewardship Award, in part for the use of a bio-based corrosion inhibiting admixture in the buildings of the Lodge at Gulf State Park. The project is pending the Leadership in Energy and Environmental Design (LEED) Gold certification. In addition to being in line with the project’s goals for sustainability and resiliency, the admixture had the benefit of providing significant cost savings that helped keep the project within budget. The Lodge serves as a model for other project owners building with similar goals in corrosive environments.
Corrosion problems for reinforced concrete
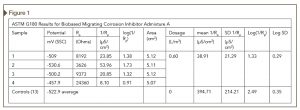
Image courtesy Cortec Corp.
Marine environments, especially those found in subtropical climates like the Alabama Gulf Coast, have a very well-known problem with corrosion. The corrosive combination of high temperatures, humidity, and chloride-ridden sea spray can take a toll on reinforced concrete structures faster than building owners would like.
Andrew Marlin, PE, senior principal at MBA Engineers and the primary structural engineer working on the Lodge at Gulf State Park, explained, “Concrete is going to have cracks, which allow in moisture, and moisture on the Gulf Coast has a high salt content. When the moisture gets on the reinforcing and post-tensioning, corrosion can happen very quickly. When it starts corroding, it spalls the concrete, and then you have got a huge mess.”
The Lodge was one of Marlin’s first projects located directly on the coast. However, from working with those who are regularly involved in coastal repair projects, he already knew millions of dollars go into coastal buildings dealing with corrosion issues, particularly on exposed areas like condominium and hotel balconies. His awareness of the significant corrosion problems on the previous Gulf State Park structure built in the 1960s factored into the search for enhancing durability of reinforced concrete in the new lodge. The original hotel was in serious disrepair, including corrosion damage, by the time that Hurricane Ivan helped finalize its destruction in 2004. Since the structure was so deteriorated, it had become a high priority for the publicly funded project to be durable and long lasting.
Available methods for corrosion protection
There are a variety of ways and different schools of thought on how best to combat corrosion in reinforced concrete. Some methods, such as creating a thicker concrete cover or increasing concrete mix quality, can be effective but prohibitively expensive or impractical. Epoxy-coated rebar is a common strategy for corrosion protection, but adds greater expense that may not fit within the project budget. As Marlin noted, epoxy coating can also chip off this type of rebar when it is being moved around and stored, opening up an eventual corrosion site on the rebar. Cathodic protection is also used to prevent corrosion by either electrically charging a rebar grid from a power source or attaching sacrificial anodes at regular spacing in a rebar grid prior to pouring the concrete. Finally, corrosion-inhibiting admixtures can be easily utilized to prevent corrosion on rebar by being dosed into a concrete batch at a ready-mix facility or onsite.