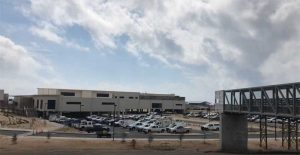
Photos courtesy Andrea Moore
There are two main types of corrosion-inhibiting admixtures. Calcium nitrite (CNI) is one of the earlier ones introduced in the 1970s. This was found to increase the chloride threshold of reinforced concrete, competing with chloride ions to create a passivating layer on the rebar and thus inhibiting corrosion. A major disadvantage is admixture dosage increases significantly based on expected chloride loading, and it is generally 10 to 30 L (2 to 6 gal) per cubic yard. In addition to the large amount of material used, CNI can also accelerate set time, especially with higher doses (read the Improving Durability of Infrastructure with Migratory Corrosion Inhibitors [MCI] handbook by Boris Miksic).
Migrating corrosion inhibitors came on to the scene in the 1980s in the form of amine alcohols with vapor pressure allowing them to travel through concrete pores and form a protective layer at the level of the rebar. The technology reached an even higher level in the 1990s with the development of second-generation amine carboxylate migrating corrosion inhibitors showing a stronger adsorption to the metal surface. These inhibitors are said to offer ‘mixed’ protection by inhibiting both the anodic and cathodic corrosion reactions. Some of these admixtures offer the additional benefit of being partially derived from renewable materials. Several are also certified to meet the American National Standards Institute/National Sanitation Foundation (ANSI/ NSF), Drinking Water System Components – Health Effects, for use in potable water structures. Dosage rate is generally fixed at 0.6 L/m³ (1 pt/yd³). Rather than accelerating concrete set time, migrating corrosion-inhibitor admixtures tend to have a set-retarding quality (unless normal set is desired).
Corrosion inhibitor admixture testing
Concrete chemistry is complex, requiring the engineer or contractor to check compatibility whenever an admixture is included in the mix design. ASTM C1582, Standard Specification for Admixtures to Inhibit Chloride-Induced Corrosion of Reinforcing Steel in Concrete, is used to test-screen corrosion-inhibiting admixtures. One portion of the test evaluates how the admixture will affect the physical properties of the concrete while another section evaluates the corrosion-inhibiting performance of the admixture. Bio-based migrating corrosion inhibitor A, which was ultimately used in the Lodge, passed both test phases, as detailed below.
During ASTM G180, Standard Test Method for Corrosion Inhibiting Admixtures for Steel in Concrete by Polarization Resistance in Cementitious Slurries, testing (one of two optional methods for the corrosion inhibiting portion of ASTM C1582), four corrosion cells treated with bio-based migrating corrosion inhibitor A were compared to 13 control cells that had no inhibitor. On average, samples treated with the bio-based corrosion inhibitor were able to increase the corrosion resistance by a factor of 10, thus meeting ASTM C1582/G180 requirements that the inhibited samples show a corrosion resistance eight times the value of the control specimens in testing (Figure 1) (see “Re: Evaluation of Corrosion Inhibiting Admixture According to ASTM G180, TCG Project 17057” by Neal S. Burke). In the physical properties portion of the ASTM C1582 test, concrete samples treated with the bio-based corrosion inhibitor showed good results, indicating the admixture did not negatively affect physical properties of the concrete mix (consult “Admixture to Inhibit Chloride-Induced Corrosion of Reinforcing Steel in Concrete (ASTM C1582) Concrete Properties Testing Final Report” by Glenn Schaefer). They did tend to show a delay in set time, which can offer a benefit to placement in warmer climates.
Gulf State Park lodge project
The Lodge at Gulf State Park is an example of how a structural engineering firm worked to ensure a quality design with corrosion precautions that would fit into the project’s overall goals and budget.
“This project, more than any other project I have ever worked on, was very concerned about resiliency,” Marlin said. He added the previous hotel (built in 1974) had many corrosion problems and was irreversibly damaged during Hurricane Ivan. The new structure required a longer service-life design that would demonstrate wise stewardship of public funds. Due to the harsh coastal location, many resiliency and sustainability issues were considered, including flooding, storms, strong winds, and of course, corrosion.
Reinforced concrete was the main construction material chosen for the hotel complex. Hence, early discussions of corrosion control focused on the use of epoxy-coated rebar to discourage corrosion, despite the significant cost expected. However, as the project progressed, it was evident this option was not going to fit with the budget, no matter how hard the structural engineering firm tried. Marlin said a new opportunity opened up when the project’s LEED consultant connected him with a local supplier of bio-based migrating corrosion-inhibitor admixtures, who did cost analysis and life-cycle analyses of the different options.