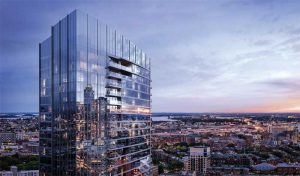
At the Raffles tower, the gaskets are primarily made of silicone, reflecting the flexible but inert nature of the material, which is non-reactive to materials. As with all other elements touching the glass, most gaskets are shop-applied in a controlled factory environment to ensure proper installation conditions. A benefit of contemporary module fabrication systems is how the gaskets can also
be replaced before the units are erected if they
are damaged, without the need for any structural changes to the module. Project teams can easily slide an old gasket out if it is cut or ripped and replace
it with a new piece. However, in general, the only elements which are field modified or modifiable are the interfaces between the panels.
In a related process, to effectively install and secure the curtain wall panels, the team had to choose which types of structural anchors would connect the curtain wall to the building structure. This is another element which warranted careful consideration due to the tower’s curved profile. On a typical building with
a more rectilinear shape, the contractor will cast
or weld anchors into the exterior face of the concrete or steel floor deck and attach the curtain wall to those anchors. However, the Raffles tower’s structure is ovoid and faceted, therefore anchors resembling embedded plates on the horizontal top surface were installed on each floor deck, offering the ability
to adjust them to match the curve of the building.
This system requires a series of specifically engineered clips and hangers designed to parameters and set by the envelope consultant as a result of the wind studies. The anchor assembly begins with the embedded piece itself, essentially a metal box, with reinforcing rebar projecting from its form. Since this is a cast-in-place concrete building, the contractor was required to install the pieces into the formwork before they placed the concrete, allowing the rebar
to be tied into the other floor and become reinforced.
The embed plates themselves are a very thin steel, which helps to shape and form a void in the concrete. Once the concrete is poured and the glass is mounted, heavy-duty aluminum clips hold the curtain wall back to the structure. The T-anchor shape of the clips enable a degree of adjustability. Once they are attached and tested, the void is grouted to be flush with the adjacent concrete floor deck.
Mock-up testing
After establishing the basic facade design of the Raffles tower, there was a rigorous mock-up process to test its viability and performance, with two initial mock-up modules in total. The primary module was built at a testing laboratory in New Hampshire, as a full two-story section of the building, including the terrace doors, an inside and outside corner. Construction of the 12.2 m (40 ft) wide and 7.62 m (25 ft) tall module took a week and it only fit inside the lab facility. The experts, who would eventually handle the final installation at the project site, also built the mock-up module to identify any immediate erection or fabrication issues.