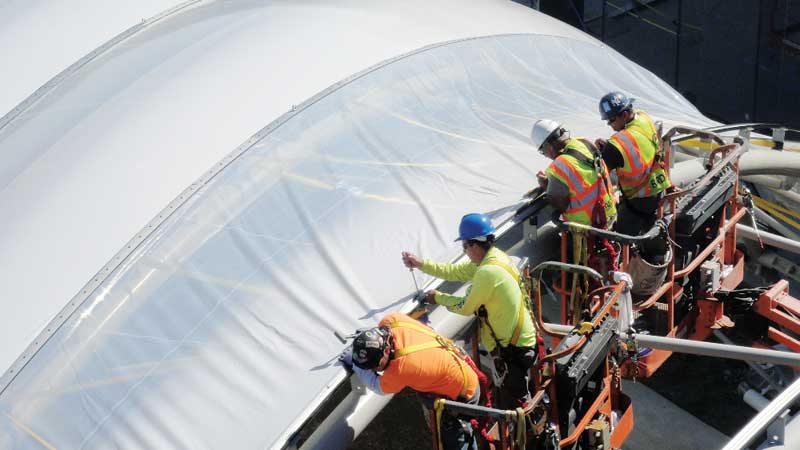
Design process steps
The ability to achieve dynamic designs is a key benefit of tensile architecture. Its two basic forms are single layer, where tension is achieved through mechanically tensioning the ETFE; and double or triple layer cushion constructions, where tension is achieved through pressurization or inflation.
Throughout the design-build process, contractors specializing in tensile structures work with architects to provide project condition details to be used in construction documents or, more frequently, in the design-build specifications included for the specialty contractor.
Making the most of ETFE’s performance characteristics requires interaction between many geometric forms, materials, and tensioning options. Design can be aided by sophisticated software to help architects and engineers create nearly any imaginable design.
Consultation with a contractor that specializes in ETFE architecture is an extremely valuable step. Architects who work with ETFE film structures recognize this cooperative effort as a best practice. Working with a specialty contracting firm, with in-house design, software, data, and fabrication resources, can minimize risk for the client, designers, architects, and engineers.
ETFE structures are generally specified as design-build projects. In designing the structure, the geometry need to be addressed first. Next, testing how the membrane will interact with the support structure helps determine how to meet the load requirements. Throughout the entire design-build process, coordination is critical to the structure’s overall aesthetics and performance.
Tensile contractors
Special software packages used in-house by specialty contractors incorporate finite element analyses to provide detailed output for proposed designs. Full design responsibility typically rests with the tensile contractor and is inclusive of both the membrane and structure, which is usually composed of steel and/or cables.
Membrane products are purchased in stock lengths and widths. The engineering and detailing required to pattern the material should be included in the scope of the tensile contractor’s work. During membrane fabrication, stock lengths are cut to the designed patterns. Then, the patterns are assembled to the desired panel sizes required for installation.
Since most tensile contractors provide design-build services, they are also responsible for detailing all of the tensile structure’s various elements. Detailed drawings of each element are required to effectively produce fabricated elements. Typically, performance specifications are prepared by the architect and engineer. It is the responsibility of the pre-qualified specialty contractor to provide a proposal that meets the outlined criteria.
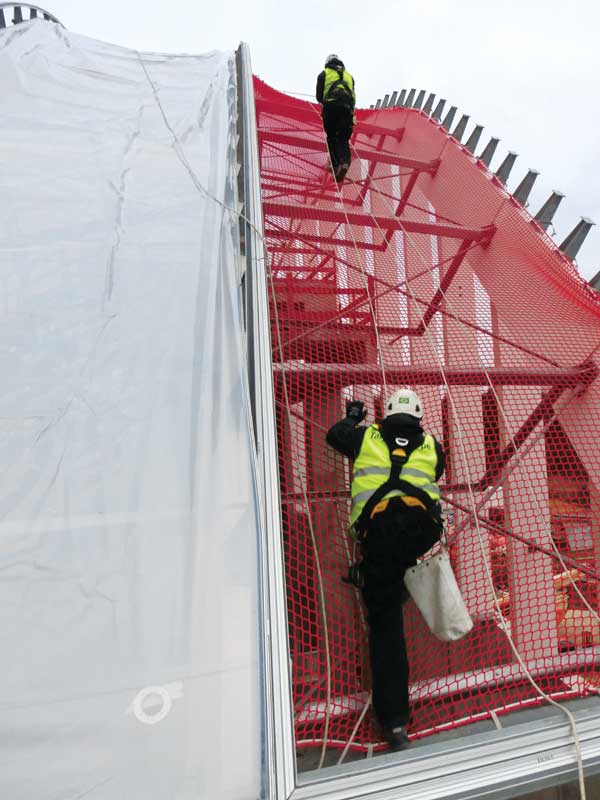
During the construction phase, forces applied to the structure during installation must be analyzed to prevent unbalanced loads. Since the integrity of a structure relies on elements erected and set in tension, detailed engineering and planning is necessary for the membrane, steel, cables, and the methods developed to install the system.
Testing of the membrane
Tests must be completed to evaluate the film’s behavior under load and determine its stress limits. With a sufficient safety factor, the design stress limit will be around 15 N/mm2. Some projects require custom tests to demonstrate adequate fire performance.
A material-testing regimen is also required in the design development process, which is critical to the structure’s life span and quality assurance (QA) processes. These tests should be provided by the specialty contractor through in-house resources or by third-party facilities approved by internationally recognized tensile organizations.
Extensive testing ensures ETFE film strength and flexibility, and that the membrane and selected connections can withstand seasonal weather extremes. A weather machine that produces accelerated weathering effects is used to test the membrane’s ability to withstand UV rays in wet and dry conditions. Light transmission and reflectance are also measured.
Construction and installation
After a project is approved through design development, and manufacturing and testing are underway, the contracting firm’s project managers and engineers collaborate with the general contractor on the construction methodology and coordinate erection procedures and scheduling. Throughout construction, site superintendents manage the installation of the structural supporting steel, extrusions, cables (if required), and the ETFE film. Due to the lightweight nature of membrane, installing an ETFE roof or façade system is a cost-effective solution that requires less structural steel to support the roof compared to conventional building materials, enabling long spans of column-free space.
Since ETFE structures require some maintenance, building owners often work with the contractor to ensure adequate aesthetic and structural longevity of the steel, cables, or tensile membrane, as well as the air inflation system for a pneumatic structure. These services can range from simple cleanings to comprehensive structural reviews and modifications.