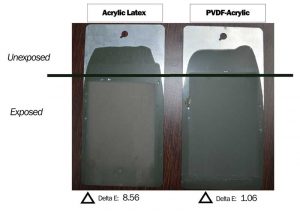
Image courtesy APV Engineered Coatings
While AAMA 2605 was originally written around the performance of 70 percent polyvinylidene fluoride (PVDF) fluoropolymer finishes, SSPC Coating Specification No. 36, Two-Component Weatherable Aliphatic Polyurethane Topcoat, was published to address this polymer type. In terms of color and gloss retention, this standard allows for weathering testing using either UVA fluorescent cabinet accelerated testing (ASTM G154, Standard Practice for Operating Fluorescent Ultraviolet (UV) Lamp Apparatus for Exposure of Nonmetallic Materials), or natural weathering (ASTM D1014, Standard Practice for Conducting Exterior Exposure Tests of Paints and Coatings on Metal Substrates). The coatings are assigned to one of three performance levels based on the number of hours or months of exposure meeting a maximum of 2 ΔE (C.I.E 1976 L*A*B*) (this is the color system used in SSPC Coating Specification No.36, Two-Component Weatherable Aliphatic Polyurethane Topcoat. It defines color slightly differently from the Hunter system that is used in AAMA 2605). Like AAMA 2605, SSPC Paint 36 specifies chalking is measured per ASTM D4214 Method A, but all colors are required to chalk at a minimum level of six.
It is important to note SSPC Paint 36 section 12.4.2 says, “Performance results from accelerated weathering do not necessarily correspond to those from the corresponding level of atmospheric weathering. It is left to the discretion of the specifier whether to accept natural outdoor weathering data from a similar color or to use UVA data in lieu of natural outdoor weathering data.”
Further, section 12.4.3 goes on to add, “Test results for color and gloss of deeper colors (i.e. having a Munsell value below nine) will vary significantly due to differences in pigment weathering properties, and may not meet the requirements of section 7, “Weathering Requirements,” without use of additional procedures such as clear coating. Alternatively, the specifier may accept a greater change in gloss and color for deeper colors.”
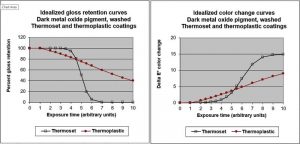
The coatings have identical 80 percent gloss retention times, but the time to significant color change associated with chalking differs by more than a factor of two.
Images courtesy Arkema Inc.
MPI 311, Latex, Exterior, High Performance Architectural, Semi-Gloss, covers “…a high performance white or colored semi-gloss, latex-based paint intended for use on new or previously painted exterior wall surfaces…not intended for application on un-primed wood surfaces.”
For conformance to weathering performance under this specification, the coating must only pass 2000 hours of UVA fluorescent cabinet accelerated weathering testing as per ASTM D4587, Standard Practice for Fluorescent UV-condensation Exposures of Paint and Related Coatings, (similar to SSPC Paint 36 Level 2A), with “no blistering, chalking, checking, cracking, flaking, or loss of adhesion.”
It is important to note these last two standards for field-applied coatings only use white or light-colored coatings to evaluate weatherability. AAMA 2605, which does have the same 10-year natural weathering requirement for all colors, is primarily a voluntary standard for original equipment manufacturer (OEM) topcoats on aluminum. There are currently no standards for field-applied coatings to address the needs of specifiers who want to validate color retention in high chroma or saturated and bright colors. Raw material suppliers and the coating developers have found that the common practice in the industry is to focus on meeting the specification, but not necessarily exceeding or adapting it.
Color retention under the microscope
Several factors determine the length of an exterior coating’s color lifetime and it is important to take a closer look at the chemistry and photodegradation modes of the coating’s polymer(s) (the ‘binder’). The resin chemistry, pigment grades, and the volume of pigment concentration, all determine the impact of radiation, extreme temperature, salt, and the atmospheric moisture on the coating’s gloss and color. In pigmented coatings, reducing the rate of binder loss is an important goal of the formulator, since significant loss leads to chalking, which in darker colors also brings about a change in hue.
It is very important to consider the difference in photodegradation failure modes between coatings made with the highly crosslinked thermosetting resin systems and thermoplastic resin systems with little or no crosslinking. Thermoset materials, such as polyesters and fluoroethylene vinyl ether (FEVE) resins, are low in molecular weight and achieve many of their properties from crosslinks. Once crosslinked, thermoset coatings can maintain many properties very well during weathering. However, as the crosslink density drops below a critical threshold during the weathering process, binder integrity is abruptly lost, resulting in chalking on the surface.
Thermoplastic coatings with little or no crosslinking are based on higher molecular weight resins and achieve binder integrity through physical entanglements. These thermoplastic coatings often degrade through a surface contraction mechanism through which properties gradually change, without any abrupt transition. While some thermoplastic resins (e.g. one-component acrylics) eventually chalk, high PVDF-based thermoplastic coating systems withstand chalking over multiple decades of outdoor exposure (Figure 1).
Figure 2 illustrates the result of an accelerated weathering study conducted on two thermoplastic coatings in dark green, a one-component acrylic latex and another one-component PVDF-acrylic, after 10,000 hours of exposure. This study validates the actual performance of the PVDF formulation when comparing the accelerated results to the natural weathering study in Figure 1. It also demonstrates the more rapid changes in color and chalking of the thermoplastic one-component acrylic in comparison to the PVDF.