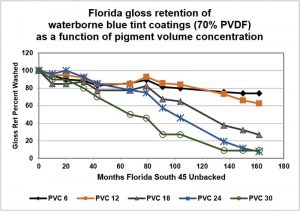
Figure 3 depicts idealized versions of how the evolution of gloss and color retention can differ for coatings with thermoset and thermoplastic binders. The two systems have about 80 percent gloss retention after four units of exposure time. For the thermoset system, chalking occurs at about five to six time units, leading to rapid gloss loss and color change. Chalking for the thermoplastic system in this instance may occur closer to the 10 time units point.
The resin-pigment relationship
Premium fluoropolymer topcoats have been used for decades in outdoor environments because of their color-retention property and the absence of chalking. High PVDF-content systems with a relatively low pigment volume concentration (PVC) allow the pigment to remain encapsulated, even if all the acrylic co-resin is compromised by exposure, as seen in Figure 4 where gloss retention is visible for a series of water-borne paints made with a 70 percent PVDF-acrylic hybrid latex binder, after 10 years of exposure in Florida.
This minimal color change is attributed to the absence of chalking (when a high PVDF: pigment volume ratio is employed), along with the use of color-stable inorganic pigments in the formulation. The color service life of such coating systems can be measured in decades.
Since color-stable inorganic pigments are unavailable in a full palette of bright, saturated colors, many coatings makers turn to organic pigments. While color change is greater for coatings made with organic pigments, the use of a PVDF resin can help ensure the visual effect of the color change is minor (Figure 5). The much greater color change for the non-fluorinated acrylic urethane system is due to both the pigment bleaching and chalking of the binder.
The ‘false positive’ conundrum
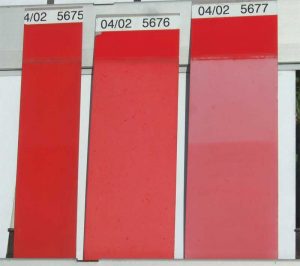
Accelerated weathering testing is the fastest way to acquire information on the service life of a coating. However, an inappropriate reliance on accelerated testing can increase risk, if materials perform well in accelerated testing, but not in natural weathering. These cases are known as ‘false positives.’
The reason why accelerated weathering test methods cannot be correlated with outdoor weathering, independent of material considerations, is rooted in the fact coatings based on different resin chemistries have varied failure modes. It is impossible to equally accelerate all the factors contributing to different failure modes, in any specific test.
Due to these differences, material-agnostic standards, such as AAMA 2603, Voluntary Specification, Performance Requirements and Test Procedures for Pigmented Organic Coatings on Aluminum Extrusions and Panels (with Coil Coating Appendix), 2604, Voluntary Specification, Performance Requirements and Test Procedures for High Performance Organic Coatings on Aluminum Extrusions and Panels (with Coil Coating Appendix), and 2605 for pigmented organic coatings on aluminum extrusions and panels, do not allow alternatives to natural weathering. When accelerated testing is involved, differences in failure modes for dissimilar materials imply there will almost unavoidably be an increase in risk. In such cases, one powerful way to reduce risk is to limit the scope of the standard to a narrower range of materials, where there is a strong defined correlation between field performance and the accelerated test(s) to be used.
This strategy goes against the trend toward material-agnostic standards, but there is a precedent for this kind of approach within the current SSPC standards. For example, SSPC Paint 36 limits its scope to resins as defined by ASTM D16, Standard Terminology for Paint, Related Coatings, Materials, and Applications, Type 5. To that end, identifying an appropriate performance-based standard for low-color-fade fluoropolymer coatings should be restricted to specific fluoropolymer resin chemistries with proven performance, and the accelerated testing criteria for each chemistry type should be selected based on available historical data for how commercially relevant coatings perform under natural as well as accelerated conditions.
Formulations for factory versus field application
There are some differences between the composition of factory- and field-applied engineered coatings using fluoropolymer technologies. Formulating a factory-applied fluoropolymer coating incorporates a catalyzing and backing system to ensure uniformity and proper cure using controlled OEM or plant conditions. Engineered fluoropolymer technologies for field-applied applications use wetting and drying chemistries in the formula to promote proper cure under fluctuating atmospheric conditions to produce quality coatings.
Factory-applied coatings also have many advantages including:
- controlled environmental conditions with clean areas;
- uniform coating thicknesses;
- precise drying; and
- curing temperatures to promote proper crosslinking.
The biggest problem with field-applied coatings is surface preparation before application of the engineered coating. The surfaces need to be properly cleaned and prepped for the coating to have proper adhesion and weathering resistance. Atmospheric conditions such as temperature, humidity, and wind introduce unique drying conditions for the field-applied engineered coating to overcome. Also, the lack of controlled higher curing temperatures produces slower crosslinking times. It may take more than a month to ensure a complete cure for a field-applied engineered coating.