Is a new standard required?
Many believe the industry needs a new standard. SSPC’s C.1.8 fluoropolymer coatings committee has been active over the past years and has produced a technical update (SSPC-TU 12) describing the two major fluoropolymer resin types mentioned earlier, PVDF and FEVE. These two chemistries are used for highly weatherable topcoat applications. While they differ in some important details, both these resins can be used in several different kinds of coatings, including solvent- and water-borne versions. These coatings can offer, in many cases, service lifetimes for gloss and color retention, which are longer than those attainable with non-fluorinated organic polymers, such as the two-component acrylic urethane systems described above in SSPC Paint 36, or acrylic latex paints as described in MPI 311.
This committee has been collaborating to develop a new specification for fluoropolymer topcoats. The architectural restoration coatings sector has expressed this as a need for a standard that can be used when long-term color retention is important. To-date, standards bodies have been challenged to create new material-agnostic, performance-based standards eliminating the false-positive problem associated with the accelerated testing of a wide range of materials.
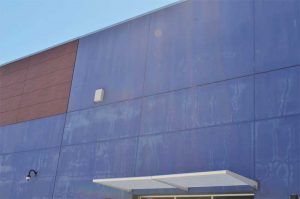
Image courtesy APV Engineered Coatings
From microscope to market
Fortunately for project specifiers, outdoor and accelerated weathering data does exist for high-chroma, PVDF-based coatings. Developers of this technology have tested saturated and dark colors beyond the requirements of specifications and have adapted accelerated studies to help evaluate new and improved prototypes. Until a new formalized standard is in place for pigmented, field-applied systems, some developers and manufacturers are doing their due diligence to ensure the data provides a much needed and reliable source for identifying a high-performance coating’s color retention in field applications for architectural restoration.
The coatings manufacturer can provide this data. Often, product data sheets list test results per the standard, but specifiers can request the test reports to back up the data the specification calls out, such as section 8, “Test Reports,” of AAMA 2605. Many manufacturers, especially developers of premium fluoropolymer-based coatings, have natural and accelerated data on a broad range of saturated and dark colors that have been tested beyond the spec until signs of failure (i.e. significant color fade, loss of film integrity, chalking, etc.). PVDF-based chemistries offering warranties for color retention are a safe and low-risk option for long-term performance for the building owner.
What does this mean for building owners?
From a cost perspective, re-coating structures every few years can get expensive and cause disruption to the occupants of the building during the process. Hospitality properties, office buildings, schools, and other commercial properties can face major disruption-induced costs from a renovation project. There are also soft costs associated with the negative curb appeal of a structure’s faded or chalky appearance (Figure 6).
From a coatings expert’s perspective, the most important risk to eliminate is the damage of the buildings substrate after the aged coating has been compromised from the elements. Failing to maintain a new protective coating on a surface can cause damage to the underlying substrate, an even more costly issue to resolve. After long-term exposure to the elements, standard latex-acrylic and urethane coatings break down and eventually wear away entirely. Although the initial cost of commodity paint may be low, the life-cycle costs will far exceed those of implementing a high-performance coating system.
Conclusion
As one of the most visible indications of performance, the advancements in color retention for exterior-use architectural and protective coating technologies have resulted from the evolution of in-depth science and test standards. Manufacturers and governing associations are continuing to work together to set the bar higher for what ‘high performance’ truly means. Technological advancements must be proven through validated and trusted test protocols taking into consideration the resin and pigment types, material to be coated, and field or factory application. Every entity in the supply chain plays a critical role in bringing long-lasting color performance to the field.