By Mike Banta
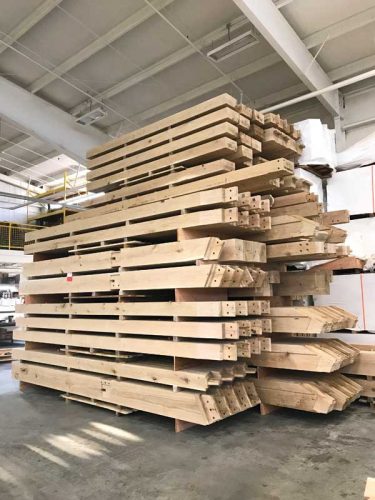
In the construction industry, there has long been a tendency to do things a certain way, primarily because “that is the way it has always been done.” However, as technology advances and projects become more complex—and with labor at a more significant premium than ever—several challenges to the traditional way of doing things on a job site have emerged.
Recent disruptions in supply chains, workforce shortages, and other obstacles to project schedules have led more owners and contractors to look for off-site, prefabricated construction methods to improve the quality and efficiency of their builds. While off-site construction is not new, it is getting a fresh look to increase building projects’ quality, reliability, timeliness, and sustainability.
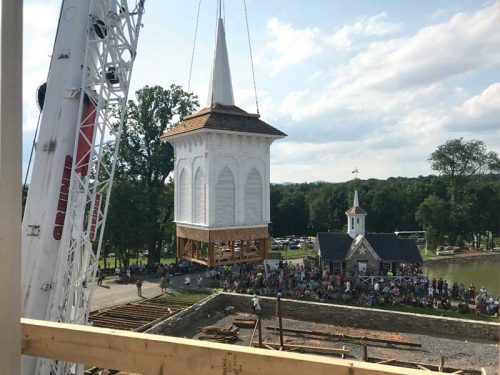
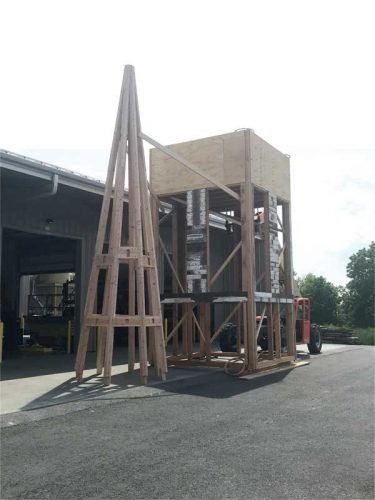
Off-site construction
Off-site construction can be defined as the entire process of designing, manufacturing, and on-site assembly of elements that have been prefabricated in an off-site factory.1 Removing that kind of work from the job site creates less waste, contributes to scheduling efficiencies, and reduces labor and safety concerns.
Using a high-quality, carefully designed system such as heavy timber construction offers many advantages to off-site construction. From a quality standpoint, the kind of tolerances and control possible in the stable conditions of a manufacturing facility cannot be matched on often chaotic sites. Other advantages include the aesthetic quality and durability. Heavy timber stands out as a sustainable building material and is embraced by builders worldwide. Whether used for a luxury mountain residence or a modern college research center, off-site heavy timber, or simple timber, construction is finding its way into several types of buildings.
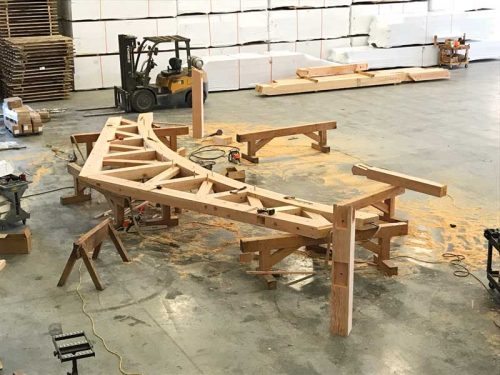
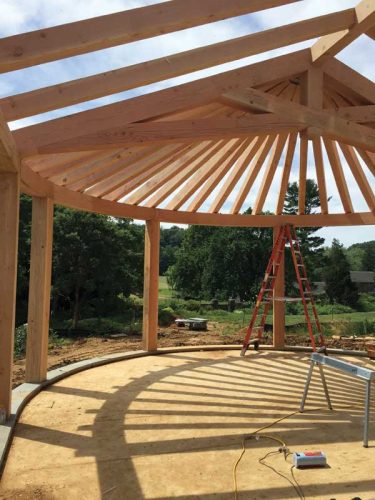
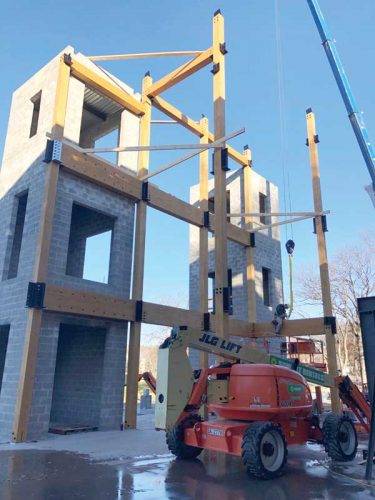
Timber terms
- Heavy timber: Uses large, rustic timbers traditionally held together with mortise-and-tenon joinery; metal plates and concealed fasteners are also used. In many cases, these timbers are left exposed in a finished project, taking advantage of wood’s natural strength and beauty for distinctive buildings that stand the test of time. While heavy timber was used mainly for agricultural buildings and residential properties in the past, today, it is popular for schools and universities, churches, municipal buildings, and commercial buildings.
- Mass timber: A composite product within the engineered wood products (EWP) category, mass timber is manufactured from smaller wood pieces that are glued and/or dowelled together into beams, posts, and structural panels.
- Cross-laminated timber (CLT): Comprised of three or more layers of lumber with knots and checks removed, each layer is glued so that its wood grain is oriented at a 90-degree angle from the next layer. CLT products, thus, have two-directional strength. Useful for all major structural components, including floors, interior walls, exterior walls, and roofs.
- Glue-laminated timber (Glulam): To avoid confusion with CLT, which is also glued, think of Glulam as a parallel product. Planks are laminated so the wood grains are all in the same (parallel) direction. This single-directional strength means GLT products are ideally suited for support structures such as columns, beams, and trusses.
- Dowel-laminated timber (DLT): Pieces are doweled together. They may or may not be glued as well.
- Mass plywood panel (MPP): As the name implies, sheets of plywood are glued together into thicker panels or components.
It is lean
By nature, off-site timber construction has the potential to significantly improve a project’s overall efficiency. Off-site components can be manufactured while foundations are poured and prepared to receive them. Monitored manufacturing settings equipped with precise fabrication tools, automated processes, and standardized workflows create quality control (QC) and consistency levels that surpass what is possible on a construction site. Off-site construction also means a more consistent work crew and a more controlled workflow less prone to disruption.
Components built in a climate-controlled factory virtually eliminate the risk of delays due to weather. Off-site production facilities are also more reliable, making timelines and costs more predictable. Factory construction allows workers to become specialized experts in their craft, leading to higher-quality products.
In the labor sector, manufacturing project components at another location means fewer workers on the site. According to the latest workforce survey conducted by the Associated General Contractors of America (AGC) and Autodesk, “…85 percent of construction firms report they have open positions they are trying to fill. Among those firms, 88 percent are having trouble filling at least some of those positions—particularly among the craft workforce that performs the bulk of onsite construction work.”2 In light of these statistics, requiring fewer workers to complete a project can make a big difference.
Further, safety is an important element in every job. Any opportunity to lessen the potential for injury and harm is helpful. Minimizing the activity and crew needed on the job site decreases the chance of accidents (refer to the “Injury comparisons: Construction versus manufacturing” sidebar on page 13).
It is clean
Taking much of the work off the job site makes for a tidier environment, generating less waste and debris on the site. “Accidents can occur when materials are spread throughout a location, including falls and other dangerous incidents. And coordination is easier with fewer people on-site,” says Sam Ebersol, general manager of Mid-Atlantic Timberframes.
There are also advantages on the job site. With less on-site construction, even tight or remote sites become easier to work with.
“In urban areas, space is at a premium,” Ebersol says. “Storing construction materials and equipment on-site during the building process is not ideal and may not even be possible. Builders can save space by having heavy timber components built in a factory and scheduled for precise, on-time delivery to the site.”
An added benefit of a clean work site is a positive perception of the proceedings by the client and the public, elevating the impression of the construction companies involved.
It is green
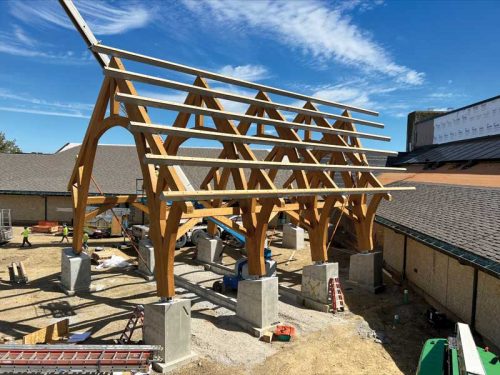
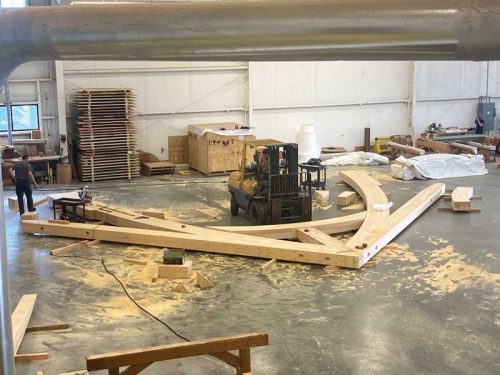
Many companies today are dedicated to reducing the environmental impact of construction. This means minimizing waste and pollution and lowering greenhouse gas emissions (GHGs).
Timber framing boasts a lower embodied carbon footprint than steel or concrete materials.3 This advantage stems from timber’s natural carbon sequestration process: Trees absorb carbon dioxide (CO2) as they grow, storing it within their fibers even after harvesting. Timber production also requires less energy-intensive processing than steel or concrete manufacturing. Timber’s renewability, responsible forestry practices, and efficient construction techniques further contribute to its reduced environmental impact.
Mark Hughes, professor of Wood Material Technology at Aalto University in Finland, notes that building construction accounts for between 30 and 50 percent of material usage.4 In comparison, construction and demolition waste accounted for 32 percent of total waste in the 27 European Union countries (EU 27) in 2012.
Further, timber framing is a champion of waste reduction and recycling, embodying the principles of a circular economy. First, there is very little waste generated in highly efficient production processes. Artisans working in controlled plant conditions can cut all pieces to necessary lengths with great precision, making the most effective and complete Artisans working in controlled plant conditions can cut all pieces to necessary lengths with great precision, making the most effective and complete use of the materials. Second, offcuts and byproducts are carefully repurposed or recycled, reducing the burden on landfills. This sustainable approach aligns with responsible forest management practices, where harvested trees are optimized for use, leaving little to waste.
Additionally, less work on the job site means less air pollution, dust, and noise in areas near other buildings and communities. This is good for the local environment and neighbors who are not eager to be near dirty, noisy, and long-lasting construction projects.
Off-site timber construction: How does it work?
Off-site timber construction has revolutionized the traditional building process by efficiently manufacturing timber components in controlled environments. Embracing this method brings numerous advantages, including reduced construction time, minimized waste, and enhanced quality control (QC).
Here is the standard process:
- Design and engineering—The first step involves designing the timber structure and creating detailed engineering drawings. Architects and engineers work together to ensure the design meets all requirements, adheres to building codes, and maximizes the efficiency of off-site construction.
- Material selection—High-quality timber is selected based on the project’s requirements and design specifications. Timber species offering the desired strength, durability, and aesthetic appeal are chosen.
- Preparation of components—Timber is cut, shaped, and prepared in the off-site facility to create the various components of the timber frame, including beams, posts, trusses, and panels.
- Joinery and assembly—Skilled artisans use traditional joinery techniques or modern connectors to assemble the timber components into pre-engineered sections, ensuring precision and consistency in the construction process.
- Quality control (QC)—Rigorous quality control checks are performed throughout the assembly process to ensure all components meet the required standards and fit together accurately.
- Finishing and treatments—Timber components may undergo finishing processes, such as sanding and applying protective coatings or preservatives, to enhance their appearance and durability.
- Transportation—Once the timber components are ready, they are transported to the construction site. Careful packaging and transportation ensure the components remain in excellent condition.
- On-site assembly—The prefabricated timber components are carefully lifted into place and assembled by skilled workers. This process is often faster and requires fewer workers than traditional on-site construction.
- Integration with other systems—Once the timber is in place, other building systems, such as electrical, plumbing, and HVAC, are integrated into the structure.
- Finishing touches—The final stages involve finishing the interior and exterior surfaces, including roofing, cladding, and interior fittings.
Injury comparisons: Construction versus manufacturing
According to data from the U.S. Bureau of Labor Statistics (BLS), from 2021 to 2022, American construction workers report fewer overall injuries than manufacturing workers.1 However, a deeper look at the data shows that injuries to on-site construction workers tend to be more significant by comparison, requiring more days off from work for recovery. The fatality rate is also higher for construction workers than for manufacturing workers. While there are dangers in any industry, these dangers increase when factors such as transportation, heavy materials, weather hazards, height, and equipment are involved.
Top three fatality risks in construction (NAICS 23), in descending order:
- Falls, slips, trips
- Transportation
- Exposure to harmful substances or environments
Top three wood product manufacturing (NAICS 321) fatality risks, in descending order:
- Contact with equipment
- Transportation
- Exposure to harmful substances or environments
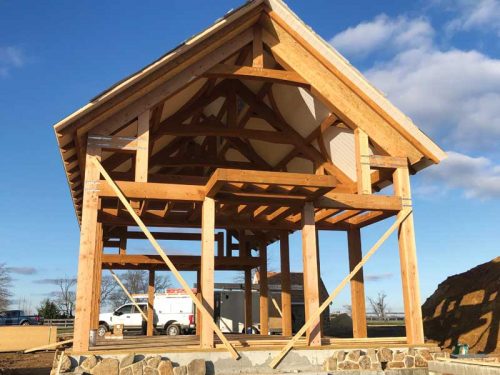
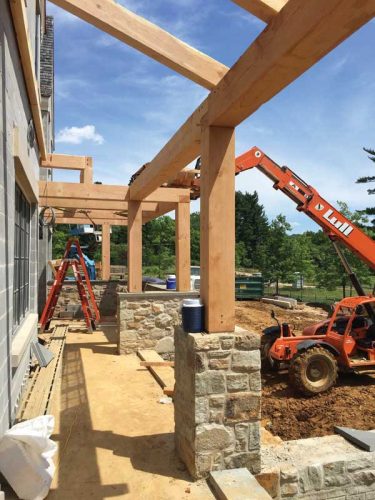
Notes
1 See the number of nonfatal occupational injuries in this datasheet: bls.gov/iif/nonfatal-injuries-and-illnesses-tables/case-and-demographic-characteristics-table-r65-2021-2022.xlsx.
2 This is in line with a frequently cited 1999 Bureau of Labor Statistics (BLS) report titled Work-related Injuries, Illnesses, and Fatalities in Manufacturing and Construction. Read the report at bls.gov/opub/mlr/cwc/work-related-injuries-illnesses-and-fatalities-in-manufacturing-and-construction.pdf.
TABLE 1
Industry | NAICS code | Total recordable cases | Cases with days away from work, job restrictions, or transfer | Other recordable cases | ||
Total | Cases with days away from work | Cases with days of job transfer or restriction | ||||
All industries, including private, state, and local government | 238100 | 25,280 | 1.8 | 1.3 | 0.6 | 1.2 |
Construction | 23 | 2.4 | 1.5 | 1.0 | 0.5 | 0.9 |
Manufacturing | 31-33 | 3.2 | 2.0 | 1.1 | 1.0 | 1.2 |
The incidence rates represent the number of injuries and illnesses per 100 full time workers and were calculated as (N/EH) x 200,000, where N = number of injuries and illnesses; EH = total hours worked by all employees during the calendar year; and 200,000 = base for 100 equivalent full-time workers (working 40 hours per week, 50 weeks per year).
Tables courtesy U.S. Bureau of Labor Statistics (BLS)
TABLE 2
Industry | NAICS code | Total cases | Number of days away from work | |||||||
1 day | 2 days | 3 to 5 days | 6 to 10 days | 11 to 20 days | 21 to 30 days | 31 or more days | Median days | |||
Construction: Foundation, structure, and building exterior contractors | 238100 | 25,280 | 3,030 | 2,160 | 4,280 | 2,790 | 2,780 | 1,600 | 8,630 | 12 |
Manufacturing: All other wood product manufacturing (Manufactured homes, premanufactured wood products, other) | 321990 | 2,270 | 350 | 240 | 400 | 250 | 410 | 130 | 490 | 7 |
Number of nonfatal occupational injuries and illnesses involving days away from work, restricted activity, or job transfer (DART) days away from work (DAFW), and days of restricted work activity, or job transfer (DJTR) by industry and number of days, and median number of days, private industry, 2021-2022, according to the Bureau of Labor Statistics (BLS).
Notes
1 See the U.S. Department of Housing and Urban Development Office of Policy Development and Research. Offsite Construction for Housing: Research Roadmap. Ryan E Smith, Ivan Rupnik, Tyler Schmetterer, and Kyle Barry, huduser.gov/portal/portal/sites/default/files/pdf/Offsite-Construction-for-Housing-Research-Roadmap.pdf.
2 Read Associated General Contractors of America (AGC), “Survey Shows 88% of Construction Firms Are Having a Hard Time Filing Vacancies, Reveals Flaws in Nation’s Approach to Preparing Workers for Construction Careers” at agc.org/news/2023/09/25/survey-shows-88-construction-firms-are-having-hard-time-filing-vacancies-reveals-flaws-nations.
3 Also see “Embodied Carbon 101: Building Materials” by Madeline Weir, Audrey Rempher, and Rebecca Esau at rmi.org/embodied-carbon-101/.
4 Read “Cascading Wood, Material Cycles, and Sustainability” in Rethinking Wood: Future Dimensions of Timber Assembly, edited by Markus Hudert and Sven Pfeiffer, page 31.
Author
Mike Banta is the operations director at Mid-Atlantic Timberframes. For more than 20 years, he has designed timber frame structures. He has advanced expertise in glue-laminated timber (Glulam), cross-laminated timber (CLT), and steel hybrid systems, and other structural components, including structural steel and reclaimed and recycled timber. Banta is also well-versed in sustainable design, 3D modeling and detailing, computer numerical control (CNC) programming, prototyping, and quality control (QC).