Building durable structures: Considerations for concrete, waterproofing, and longevity
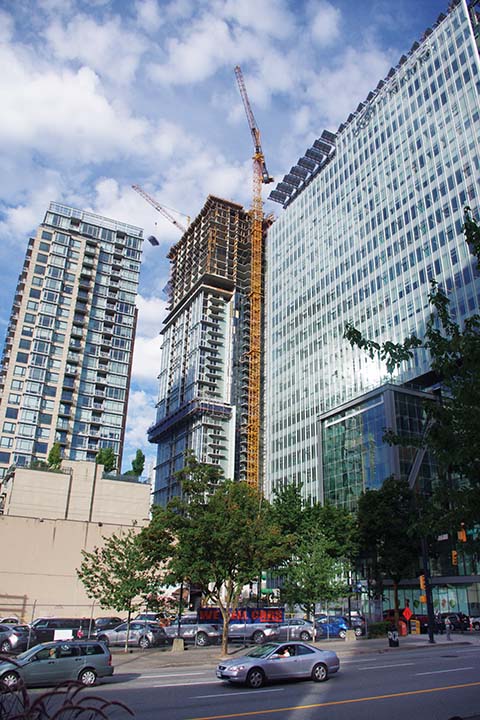
Internal and external waterproofing
To create a durable structure, one must lower the permeability of the concrete. This requires a waterproofing solution—either applied as a layer to the outside surface or internally. The choice for concrete projects is usually between an externally applied product (e.g. a cold-applied polymer-modified-bitumen [mod-bit] sheet membrane or a brush-applied liquid membrane) and an internal crystalline admixture.
The former option continues to be used on more projects around the world than the latter because it is the traditional method. However, crystalline admixtures are growing in popularity as more successful projects are brought into the open. When added to concrete, these admixtures create a reaction that causes microscopic crystals to form, filling the pores, capillaries, and hairline cracks of the concrete mass. As long as moisture remains present, crystals continue to grow throughout the concrete, reaching lengths of many inches over time. Once the concrete has cured, the crystalline chemicals sit dormant until another dose of water (such as through a new crack, or due to humidity in the air) causes the chemical reaction to begin again.
In the recent past, structures were built on land that provided a lot of space, only went a story below-grade, and faced shorter life expectancies than the 100-plus years currently expected. Structures are now built several stories below-grade and do not allow access for an external membrane repair. These buildings are also built in high-density areas, meaning repairs are highly complex, teardown highly specialized, and rebuilding costly. With these new issues comes a call for a change from the traditional.
Application
Traditional externally applied membranes require perfect application and contours; vertical application can also be difficult due to tight space constraints for applicators. Details can be problematic and require both highly skilled and suitably trained installers. These standard products must be installed in dry weather as they will not perform over damp or uncured surfaces. While the materials will protect the positive (i.e. wet side), the negative (i.e. dry side) will be exposed to other deterioration mechanisms.
Internal crystalline admixtures can be easily added directly to the ready-mix truck or at batch plant. No surface preparation or site labor is required, and there tends to be less management hassles and safety issues because less equipment and personnel are onsite. Offering both positive and negative protection, their use means reduced potential for human error and a shortened construction schedule.
For sheet- or liquid-applied membranes, field fabrication requires intensive labor and carefully supervised installation. Integral waterproofing admixtures tend to be less expensive for materials, and additional labor costs are almost non-existent. They also allow for a larger building footprint and reduce maintenance and repairs over the long term.
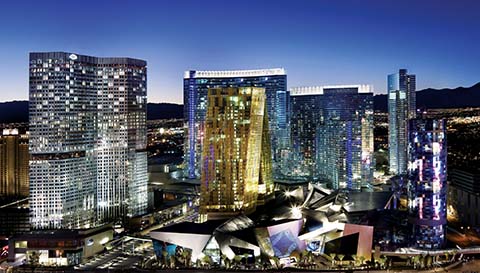
However, integral crystalline waterproofing strategies should not be used in applications under constant movement. This is because during the crystallization process, crystals align in a three-dimensional array that breaks when subjected to excessive movement. This means areas that require flexibility and face recurring movement—such as plaza decks or rooftops—would be better waterproofed another way.
Performance
When using externally applied waterproofing membranes, the protective layer can be easily breached by pinholes or seams. The product can become brittle with age, resulting in cracks and openings. Further, some membranes may include toxic chemical additives.
Historically, hot-applied sheet systems—known as built-up bituminous membranes—were used for below-grade concrete waterproofing. These sheets were made from alternating layers of bitumen and felt. When heated, traditional bitumen—both coal tar pitch and asphalt—releases volatile organic compounds (VOCs) and potentially carcinogenic fumes. Since the early 1990s, the bitumen system’s popularity has fallen due to an increasing number of bans on its use by governmental and regulatory agencies. Substantial steps have been taken by product manufacturers to replace these types of membranes.
Crystalline waterproofing is not affected by surface water, and actually improves over the lifespan of the structure. This is because once the concrete has cured, the crystalline chemicals sit dormant until another dose of water (such as through a new crack) causes the chemical reaction to begin again. The ability to reactivate in the presence of water gives treated concrete the ability to ‘self-seal.’ When cracks form due to curing shrinkage, settling, or seismic activity, water entering through them causes new crystals to form and grow, blocking and filling the cracks. This feature effectively allows the concrete to become even more waterproof over time. Additionally, many crystalline admixtures are certified by NSF to NSF/ANSI 61, Drinking Water Components−Health Effects Conditions, which allows them to be safely used in potable water tanks.